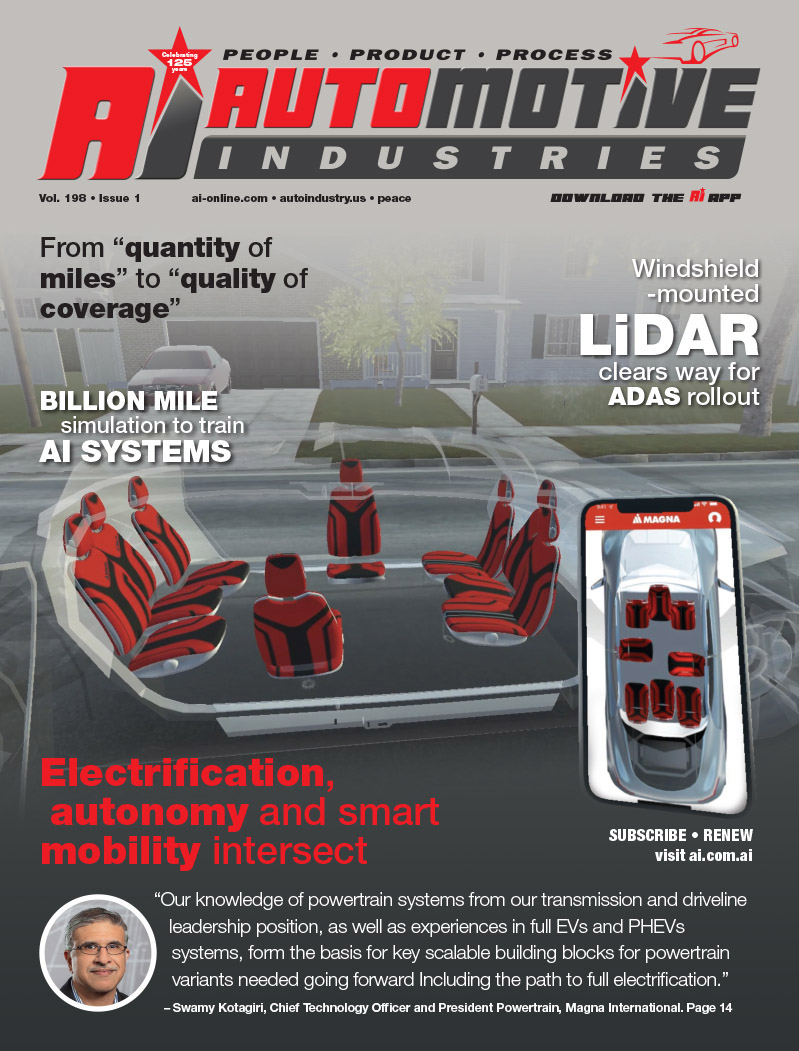

Polypropylene-based components are edging out traditional materials as the auto industry continues looking for new ways of saving weight.
Recently, Austrian-headquartered plastics solutions major Borealis and its joint venture partner Borouge unveiled a new Fibremod™ solution. In developing the instrument panel (IP) carrier for a new sports car, the OEM and its Tier One supplier Dräxlmaier sought a material solution that would deliver very high stiffness and excellent impact performance without compromising other key requirements such as dimensional stability. It was imperative that the materials selected contributed to overall vehicle weight reduction and competitive system costs.
Borealis developed a dilution system based on 50% Fibremod™ GB601HP and 50% BE677AI, yielding a PP-LGF 30% with a welldefined performance profile for the IP carrier. The Fibremod family of engineered short (SGF) and long glass fiber (LGF) compounds was officially launched in September 2013, consolidating the two previous brands Xmod™ and Nepol™ under one name.
Fibremod GD301FE has been used in place of denser engineering plastics for the construction of pedal carriers and front-end carriers. This results in up to 15% weight savings and 10% lower system costs compared to a polyamide (PA) solution. The 30% glass fiber reinforced PP offers improved processing, high performance, and high stiffness with no predrying step.
Borealis has also upgraded its thermoplastic olefin (TPO) Daplen™ EE250AI, which is used for instrument panels and other automotive applications to help achieve tiger stripefree surfaces. Tiger stripes are flow mark issues caused by converting processes which can lead to both exterior and interior surface defects. The Daplen EF150HP grade is the ideal successor to one of the first breakthrough molded-in-color solutions for body panels, ED230HP.
Automotive Industries (AI) asked Jost Eric Laumeyer, Borealis Global Marketing Manager Engineering Applications what are some of the highlights of the Borealis collaboration with Dräxlmaier.
Laumeyer: Collaboration with Dräxlmaier has proven that we can reach the goal of achieving a lighter part which meets all safety-relevant specifications. This has been accomplished through intense customer contact, and making sure all needs and regulations were met.
AI: What were the highlights of Borealis and Borouge’s exhibits at VDI Mannheim this year?
Laumeyer: We love to present technical innovations coming out of Borealis PP. As the use of lightweight material is one of the critical subjects in the automotive industry today, we wanted to showcase a new instrument panel (IP) carrier, the Fibremod™ long glass fiber (LGF) material. Together with our partner Dräxlmaier we displayed the IP carrier for the Jaguar F type, which has been on the road for a couple of months. It is amazing to see how PP compounds have found their way in applications made in the past out of metal or other plastics, such as polyamide (PA).
AI: Tell us about Borealis and Borouge’s strategy for the automotive market.
Laumeyer: The strategy is simply explained: we want to be the partner of choice, no matter where our customers want to be served. Therefore, we are present in all relevant regions either with our own facilities or in cooperation with other companies. We are constantly thinking about new investments and implementing those where it makes business sense for our customers and for us as a company. Within Borealis we have a long history of PP innovations. It is our clear commitment to the market that Borealis will further invest in new material innovations, especially in PP compounds, which drive the automotive business.
AI: Tell us about your company’s automotive primerless paintability solutions.
Laumeyer: Automotive manufacturers have traditionally used a three-layer system combining primer, base and clear coat. Switching to a two-layer, or primerless system offers many advantages, yet makes it more difficult to fulfil stringent quality and aesthetic standards. Driven by the needs of leading OEMs, we have developed primerless paintable bumper and body panel materials capable to withstand tough steam jet test conditions.
Following an investment into an automated paint robot, this major R&D initiative investigates all relevant aspects of paint adhesion – material formulation, pre-treatment conditions, processing and the use of various paint systems. Because the automotive industry is using more and more plastic components in vehicle exteriors to reduce total costs and car weight, this solution is a welcome and substantial benefit to all partners along the value chain. We are currently launching a new lightweight primerless paintable bumper material Daplen EE112AE, which is capable of reducing system costs, optimizing production cycle time and lowering environmental impact.
AI: How closely has your company worked with automotive OEMs – what levels of customization do you offer?
Laumeyer: Our business success is linked to our customers and the relationship we have with them. We have an intense global customer network, focusing on all OEMs and Tiers serving the automotive industry. Our joint cooperation with Borouge is vital in our daily activities, as this results in the availability of our services, innovations and products around the world.
AI: What are some of the surface solutions you offer automotive manufacturers and what new technologies do they incorporate?
Laumeyer: We offer a number of new materials for outstanding visual appearance with cost reduction potential and sustainable appeal. New generation primerless paintable, molded in color and tigerstripe-free tailor-made TPO compounds provide unique solutions for automotive PP applications. The material solutions build on our proprietary Borstar® polymerization technology and decades of compounding expertise. An example would be our new high-end body panel material, Daplen EF150HP, with lowered density, doubled melt flow rate (MFR) and increased stiffness compared to the previous generation, offering significant weight reduction possibilities with outstanding Class A surface aesthetics.
AI: What strategy does Borealis have for the global market, and how does this differ from your European strategy?
Laumeyer: Because our customers are active globally, we must be global too. With our Innovation Headquarters located in Linz, Austria, and our strong global network of engineers around the world developing material and application solutions, we can serve our customers anywhere with tailored innovations. Borealis has followed this strategy for many years and we have been able to gain significant global share with this approach. This strategy is backed up by the recent implementations of new production capacity investments in Europe, Asia and South America.
More Stories
Venti Technologies Wins Multiple Pinnacle Awards for Innovation and Achievement in Technology
Launch of AltaScient.ai: New horizons for Risk and Sustainability Analytics
Expert Tips on Detailing a Car