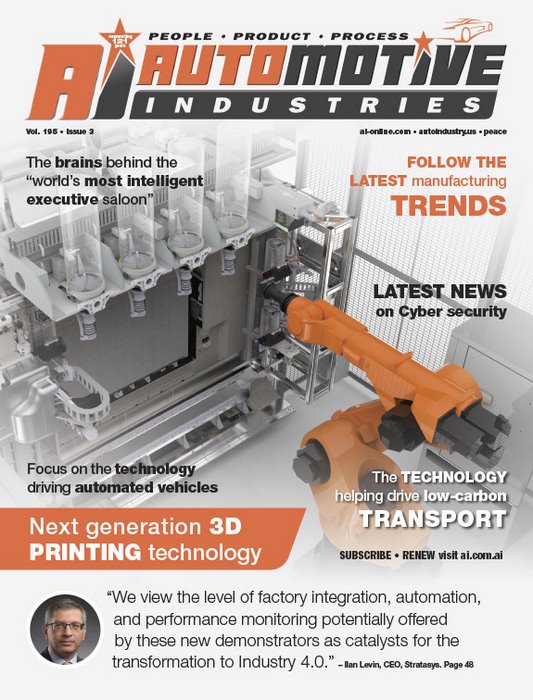
One of the limitations of 3D printing – the size of the component that the printer can accommodate – has been overcome. 3D printing and additive manufacturing major Stratasys has developed the Infinite-Build 3D Demonstrator which turns the traditional 3D printer concept on its side to realize an “infinitebuild” approach which prints on a vertical plane for practically unlimited part size in the build direction.
The Robotic Composite 3D Demonstrator delivers true 3D printing by using an 8-axis motion system that enables precise, directional material placement for strength while also reducing dramatically the need for speed-hindering support strategies. This redefines how future lightweight parts will be built, and provides a glimpse into how this technology could be used to accelerate the production of parts made from a wide variety of materials.
It is designed to meet the needs of aerospace, automotive and other industries for large lightweight, thermoplastic parts with repeatable mechanical properties. “3D printing holds the promise of changing automotive design and manufacturing because it opens up new ways to innovate and create efficiencies in production. Our vision at Ford is to make high-speed, high-quality printing of automotive-grade parts a reality. We are excited about the future opportunities that the scalable and versatile Infinite-Build concept can unlock, and look forward to collaborating with Stratasys to help achieve our goals,” said Mike Whitens, director, Vehicle Enterprise Sciences, Ford Research & Advanced Engineering. Ford is exploring automotive manufacturing applications for the demonstrator. In order to evaluate the technology Ford and Stratasys will work together to test and develop new applications for automotive-grade 3D printed materials that were not previously possible due to size limitations of the more standard approach to 3D printing.
In addition Stratasys has had a long relationship with engineering major Siemens, with both companies having a shared vision of making 3D printing a viable and indispensable component of production manufacturing. According to Siemens this is exemplified in how Stratasys developed the Robotic Composite 3D Demonstrator by integrating its core additive manufacturing technologies with industrial motion control hardware and design-to-3D printing software capabilities provided by Siemens. “Siemens is pleased to support Stratasys in its innovative additive manufacturing initiatives, of which the Stratasys Robotic Composite 3D Demonstrator is one of the most promising. By working closely with Stratasys on motion control and CNC automation, Siemens is helping to create a flexible, multi-function manufacturing workflow that puts 3D printing firmly in the factory. We look forward to continuing to work with Stratasys to build manufacturing solutions that transform industries,” said Arun Jain, VP, Motion Control, Digital Factory US, Siemens in a press statement. Aerospace giant Boeing also played an influential role in defining the requirements and specifications for the demonstrator. Boeing is currently using an Infinite-Build 3D Demonstrator to explore the production of low volume, lightweight parts.
“Additive manufacturing represents a great opportunity for Boeing and our customers, so we made a strategic decision more than a decade ago to work closely with Stratasys on this technology. We are always looking for ways to reduce the cost and weight of aircraft structures, or reduce the time it takes to prototype and test new tools and products so we can provide them to customers in a more affordable and rapid manner. The Stratasys Infinite-Build 3D Demonstrator enables products to be made at a much larger and potentially unlimited length, offering us a breakthrough tool to add to our robust additive manufacturing processes,” said Darryl Davis, President, Boeing Phantom Works. “Stratasys is building on our success in manufacturing with applications such as manufacturing aids, injection molds and composite tooling, and leveraging our relationships with innovative industry leaders to further extend the applicability of additive manufacturing in demanding production environments,” says Ilan Levin, CEO, Stratasys.
“We view the level of factory integration, automation, and performance monitoring potentially offered by these new demonstrators as catalysts for the transformation to Industry 4.0. Stratasys invites all visitors to IMTS to see these new technologies, as well as our field-proven industrial additive manufacturing solutions, in action,” he adds.
More Stories
Sonatus – The industry is shifting gears to software
Cybord warns of dangers of the stability illusion
HERE building trust in ADAS systems