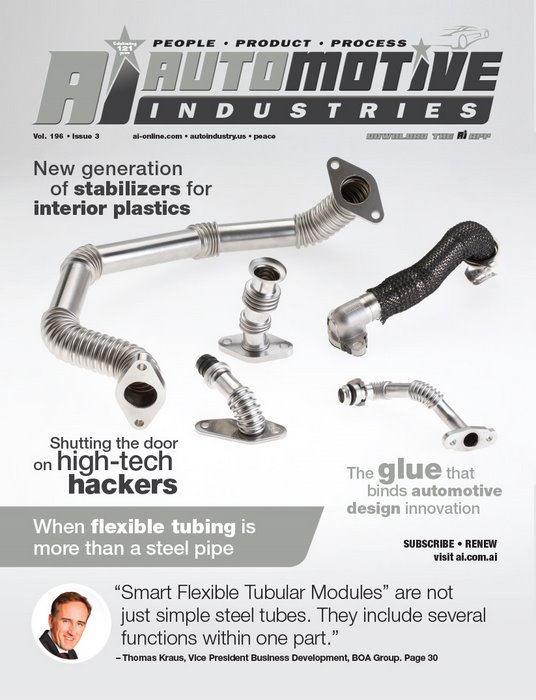
Metal tube systems need to be custom engineered for each application in order to balance their static offset and dynamic motion, and ensure they meet fatigue life requirements for any automotive, commercial vehicle and off-road application.
One of the leading systems developer and suppliers of flexible metal tube technology, bellows, metal hoses, expansion joints and decoupling devices worldwide is the BOA® Group. Its customers include almost all European and North American, and many Asian manufacturers of passenger cars and commercial vehicles. BOA pioneered the multi-ply bellows design which absorbs thermal expansion and vibration in engine and compressor piping systems.
Multi-ply bellows are manufactured from a laminated tube that consists of thin gauge stainless steel plies. This tubular body is formed partially into corrugations by a hydroforming process that delivers close tolerances. The use of thin gauge precision material combined with a number of corrugations per unit length reduces deflection forces acting on and increases the flexibility of the bellows and the “Smart Tubular Modules”.
Automotive Industries (AI) asked Thomas Kraus, Vice President Business Development Automotive, BOA® Group – to tell us where “Smart Flexible Tubular Modules” can be found.
Kraus: Smart Flexible Tubular Modules are different types of metal tube systems that the BOA® Group offers for various applications for passenger cars, trucks and off-road heavy vehicles, like:
- Exhaust Gas Recirculation (EGR) tubes
- Turbo Charger Oil Drain Tubes (ODP) and Oil Feed Tubes
- Engine Air Tubes
- Fuel Tubes
- Cooling Water Tubes
- Battery Degassing Tubes
- Secondary Air Tubes
They are individually designed and engineered for each application: Since they are produced out of thin walled precision stainless steel material they are very light and flexible on the one side, but highly pressure, media and temperature resistant on the other.
AI: How do they work?
Kraus: “Smart Flexible Tubular Modules” are not just simple steel tubes. They include several functions within one part. On the one hand they are flexible due to the integrated convolutions in terms of bellows, which are part of the tubes without interfaces. With these bellows, they dampen vibrations and compensate assembly tolerances as well as thermal elongations. These convolutions assure flexibility and leak tightness over lifetime. On the other hand, they are stiff and strong to withstand resonance, mounting forces and pressure. Smart Flexible Tubular Modules transport media like air, gas, fuel or oil without leakage. Even more, the permeation rate is zero in comparison to plastic tube solution. They resist to mass flow, corrosion, high pressure and pressure pulsation, as well as temperatures up to 1,000°C.
AI: Can they be equipped with different interface technologies?
Kraus: Their interface technology is state of the art for light vehicle and heavy vehicle applications, and is individually adopted, while complying with the relevant standards. A huge variety of rubber hose jumpers, flanges, v-clamp connections and quick connectors is part of the BOA standard portfolio. These interfaces carry very often also the sealing technology in form of O-rings, preassembled gaskets but also integrated sealing components. Individual design to reduce the number of interfaces, weight and assembly time are also used in series applications
AI: Are there other functions that can be incorporated in the modules?
Kraus: Depending on the application the Smart Flexible Tubular Modules can also carry different type of sensors (e.g. temperature or pressure), injectors (e.g. Urea ) or actuators and diffusors. A reduced number of interfaces make our tubes lighter and at higher level of performance than competing products due to the reduced interface failure risk. Different solutions for the insulation function protect the environment or the tube itself, but also avoid the loss of heat that, for example, can be transferred in electrical energy.
AI: How do you ensure that your products reduce emissions and leakage?
Kraus: Emission and leakage reduction is one of the main topics that BOA® Group is focusing on in Automotive but also various other Industries. Just to give you two examples. We offer the unique, patented urea resistant BOA EnduroFlex®, an exhaust system flex hose which allows the injection of AdBlue upstream of the flex. This is completely new to the industry and enhances SCR functionality, enabling car manufacturers to meet coming emission regulations. BOA® Group offers also EGR tube solutions, which is part of the Smart flexible Tubular Module kit, to handle the gas management in the engine. These products make it possible to offer better emission performance. Our expertise allows the successful lightweight design of EGR solutions in highly demanding applications where there are high temperatures and pressures.
The basis for this is our long-term, high level of experience, and the knowledge of our global engineering, testing and operations teams in designing, validating and manufacturing thin-walled stainless steel solutions. They undertake FEM analysis to calculate stress, CFD analysis to analyze and reduce pressure loss, and set welding and brazing specifications to assure durability. The use of high-quality stainless steels which meet BOA’s own material parameters, and 100% testing in production are only some of the measures that ensure our the high quality of our product portfolio which helps to reduce emission levels and avoid leakages
AI: What are the benefits of smart flexible tubular modules?
Kraus: The Smart Flexible Tubular Modules were developed for the increasing pressure, temperature and vibration requirements of down-sized turbocharged engines of light vehicles or modern type high performance engines in trucks. Using thin-wall manufacturing technology in combination with stainless steel materials we can offer solutions that have a reduced weight compared to classic steel tube solution. In some applications our tubular modules are even lighter than plastic or aluminum solutions. The integrated functions enable new configurations of exhaust systems or engine tube systems to meet future emission levels. The integrated flexible bellows reduce the number of interfaces, which improves the endurance performance and reduces the risks of leakage while ensuring quality. The integrated sealing and interface technology also helps to reduce assembly time and quality.
AI: Any success stories so far?
Kraus: The first generation of Smart Flexible Tubular Modules has been in series production for a number of years. Production ranges from small volume, high mix applications for trucks, as well as high-volume projects for light vehicle applications for OEMs in Europe. We are proud to say that we have reached the highest level of quality. In recognition of this achievement BOA has been honored by a major international truck manufacturer with a Quality Performance Award.
AI: What can we expect from BOA in the future?
Kraus: Actually we are in the launch phase of the second generation of Smart Flexible Tubular Modules, which offers more functionality, is even lighter and is developed for a broader range of applications for light and heavy vehicles. Our design and validation teams in our Tech centers in EMEA, US and APAC are involved in development projects at our global customers to create solutions for their post 2020 vehicles and engines
More Stories
Acoustic sensor systems and Fraunhofer measurement technology for in practical testing ͏
OSI Systems Receives $10 Million Order for Cargo and Vehicle Inspection Systems
Mitsubishi Electric Automotive America Launches Guardian Generation 3 Trial with Seeing Machines in North America