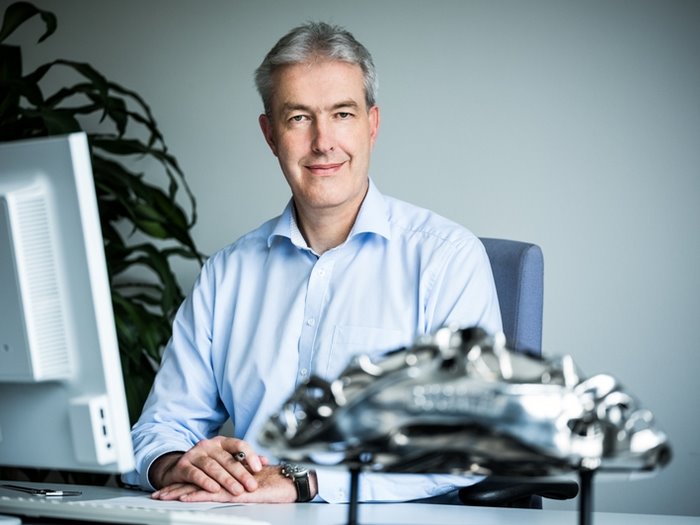
Automotive Industries (AI) asked Frank Götzke, Head of New Technologies in the Technical Development Department of Bugatti Automobiles what the implications are of the new brake caliper for the rest the Volkswagen Group.
Götzke: I currently do not see any direct implications because 3D printing is a technology with very long cycle times.
For example, a brake caliper needs 2.5 days to be printed in 3D versus only a few seconds with the production technologies normally used for large volumes in the automotive industry.
But I do see indirect implications. The only way to influence how new technologies develop is to be an active part of the community of experts driving them forward. So, the special task of Bugatti in the Volkswagen Group is to lay the foundations to make it viable for large-scale production in the future.
AI: Please walk us through the reasoning of using titanium instead of the usual aluminum?
Götzke: Actually, it is not revolutionary anymore when you look at medical sciences or the aerospace industry, where 3D printed titanium parts are common. It is, however, an innovation for the car industry. And this is where Bugatti comes into play as a pioneer, because we take our inspiration for the materials and production technologies we want to use from aerospace and medical applications.
Titanium is a material which is very complicated to handle, so you need proven experts for 3D printing, heat treatment and milling of titanium alloys. The challenge is to find these experts.
For a Bugatti supercar we need parts that withstand very high stress, similar to aircraft or medical implants. For these parts 3D printed titanium alloy is just what we need as it reaches tensile strengths of up to 1,250 N/mm2, which is five times higher than you can achieve with printable aluminum alloys.
AI: What findings have initial tests of the new brake caliper thrown up so far?
Götzke: Before starting the performance tests with the caliper itself we did a lot of material testing. We did a lot of cutting and grinding work on the raw parts which we had produced. This showed that the tensile strength in our production process was
at 1,250 N/mm2 on a continuous basis and the material filling level constantly reached fantastic values of over 99.7%.
AI: What advantages does additive manufacturing offer?
Götzke:It gives us the opportunity to make the best even better. All parts in a Bugatti are completely optimized to be super stiff, extremely stable and very light. To achieve that, we are using the best virtual simulation and calculation technologies that are now available and we are working with digital twins and virtual prototypes.
In addition to that we are developing our own calculation methods. So, when looking at our brake caliper, it is quite an chievement to make a part that is already perfect and by an additional 41% lighter by using titanium and 3-D printing.
AI: How is AM changing the way cars are manufactured?
Götzke: Additive manufacturing is changing the way cars are developed and molds, tools and equipment are made. It helps to get better prototype parts much earlier in the development process, which dramatically speeds up and improves the entire development process of a car, and also makes it more cost-efficient.
I expect additive manufacturing technologies to work much faster in the future than today’s selective laser melting, which means that the way cars are manufactured will change completely. It is still a very long way to go and it will take many years for that, but this future has begun and we at Bugatti are working with the right experts to push this development forward.
AI: How are the technologies coming out of the Bugatti’s R&D division helping the rest of the VW Group?
Götzke: On the one hand you have large-scale production, for which you need very reliable and cost-efficient parts made by the best production technologies now available. On the other hand, you have the group’s research department which works with external scientific institutes and which really looks far ahead into the future. Bugatti acts as a bridge between these two extremes.
We are the Volkswagen Group’s laboratory for applied cuttingedge and future technologies, we speak with these scientists and
look into other industrial sectors to find new technologies that are advanced and ready to be used and could be adapted for the
car industry. We look at those technologies which in our eyes will have the chance to reach the status of a large-scale production
technology in the next 10 to 15 years.
AI: What are some of the other components that are being developed by Bugatti using AM technologies?
Götzke: We have tested lots of different AM parts. We developed and Active Cooling Console for the Chiron, which is made from aluminum. It is a little mounting bracket with an integrated water cooling circuit and is able to reduce the temperature of the electric gearbox shifting pressure pump by over 40°C. This is the first metal 3D printed functional component ever made for a production car.
Allow me also to mention our latest most ambitious project in the field of simulation and calculation as well as new materials and productions technologies. It is the extremely lightweight yet ultra-rigid rear wing travel and adjustment system for the Bugatti Chiron, which we developed with Siemens Digital Factory and presented at the Hanover Fair. It is the world’s largest hybrid functional assembly to date based on 3D printed bionic titanium metal components and ceramic-coated high-modulus carbon
fiber tubes and is more than 53 % lighter than the system we are currently using in the Chiron production car. I am very proud
of this project.
More Stories
What You Should Know Before Filing a Car Accident Claim
Injured in a Car Accident in St. Louis? Here’s What to Do Next
Historic Sportscar Racing (HSR) and Goodyear Announce Multi-Year Partnership