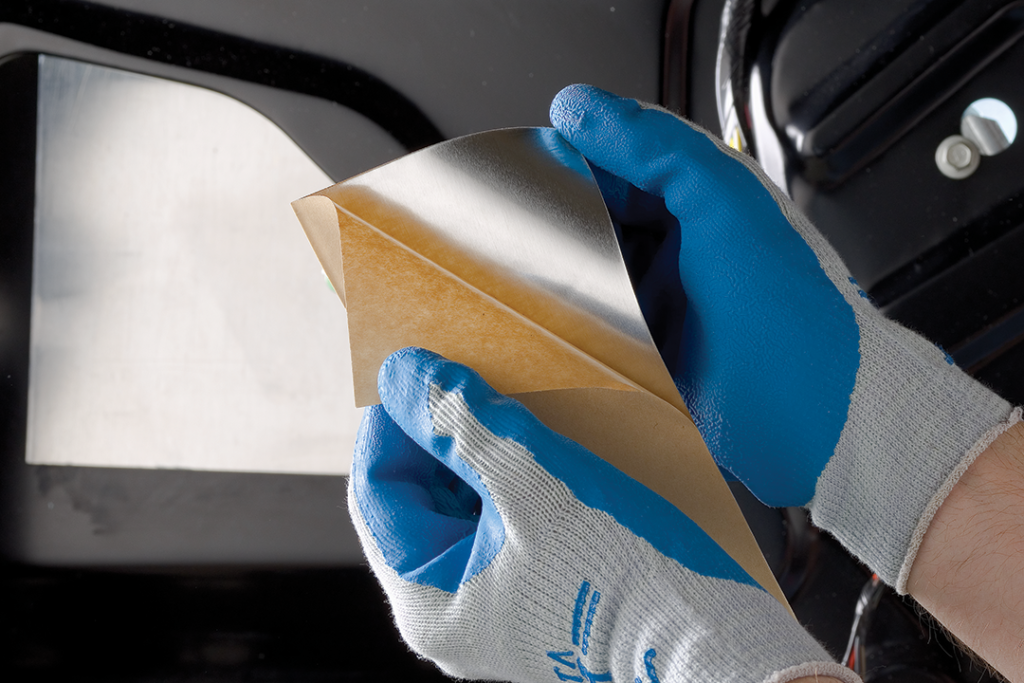
There is a growing need for materials that both bond components and damp sound and vibration.
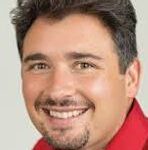
A new generation of high-performance adhesive tapes is changing the way vehicles are designed and assembled.
The tapes are being used to secure a growing range of both safety critical and cosmetic components.
To find out more, Automotive Industries (AI) interviewed Michael VanHaerents, Automotive Business Development Manager at Avery Dennison Performance Tapes.
AI: For my generation, duct tape is the universal go-to for securing just about anything. What are the design possibilities created by the new generation of tapes?
VanHaerents: Duct tape is a great tool and we all love the adaptability. Avery Dennison adhesives are highly engineered adhesive tapes at the other end of the spectrum. Each of our 300 adhesive and tape constructions consist of a variety of chemical characteristics specifically focused on different applications.
The primary function of adhesives and tapes is to bring things together, to bond them, join them, or affix something. In many instances there are secondary functionalities, including:
- Antimicrobial properties in the vehicle interior fabrics or foams. The agents are used with open cell foam that absorbs and traps moisture which can be a breeding ground for molds and mildews
- Fluorescence additives are used to indicate that the adhesive has been applied correctly using fluorescent lights. In China, all VIN labels need to be covered by a tape with a UV additive in order to identify tampering with the VIN label.
- Bonding of dissimilar materials with differential tapes. Here, there is one type of adhesive on one side and a different adhesive on the other. This chemistry could bring dissimilar materials together without the added weight of a mechanical fastener.
- Bonding foams together, with silicone or rubber tapes depending on the surface energy
- Pressure sensitive adhesives (PSA) reduce noise and vibration at the same time as joining materials, providing automobile manufacturers and Tier suppliers with a lightweight alternative to
traditional butyl and liquid applied sound dampers. A PSA provides 30% to 50% weight savings over butyl - Installation time and cost-savings can also be reduced with PSA. The tapes can be applied via robotic or automated methods, while butyl must be applied by hand and often can be messy.
- Flexibility of PSA is another benefit: automotive applications include door and roof assemblies, firewalls, trunks, hoods and floor pans – delivering rigid performance anywhere there is thin
gauge metal that can vibrate. In addition, Avery Dennison’s soundBond™ offers the unique ability to tune adhesives to specific frequencies in order to maximize its effectiveness.
AI: What is the science behind pressure-sensitive (PSA) adhesive tapes?
VanHaerents: There are two primary factors for PSA tape bonding to a substrate. The first is the PSA rheology, or deformation and flow of materials that are both elastic and viscous. These materials have solid and liquid-like properties.
Everyone remembers playing with toy putty: it bounces when you ball it up, but it also flows when you stretch it out. PSAs are very much the same. When pressed onto a substrate, the PSA will
dwell or flow over it, maximizing its bond.
The second factor is what is known as the surface energetics between the PSA and the substrate. The energetics are a combination of intermolecular forces such as Van der Waals’ interactions.
The higher the attraction between the PSA surface and the substrate, the better the surface bond. In general, low surface energy materials, like polypropylene and polyethylene, are more difficult to bond to because the surface attraction between the PSA and the substrate could be weak. To overcome this, a “softer” or high flow PSA would be recommended. A “firm” or low flow PSA like pure acrylic would likely not form a strong bond with low surface energy materials.
Some very LSE plastics don’t allow things to bond to them, they repel them. That’s why specialty adhesive products have been developed in order to bond to certain surfaces, while still maintaining relatively good strength.
AI: Where is this technology being used in serial production?
VanHaerents: PSAs are used in a number of applications:
Heat shielding products: Bond or attach flexible heat shielding materials to LSE plastics such as fuel tanks instead of stamped aluminum/steel heat shields attached with steel fasteners
- Interior / exterior mirror bonding: Anti-shatter properties for mirrors attached to the housing, and to keep them in place.
- Venting: The bonding of a Polytetrafluoroethylene (PTFE) vent will provide a temperature resistant seal for microporous venting materials. Vents used on components, such as a front headlight, need to be able to expand and contract. A hole in that material is covered with a breathable material that allows air to flow in and out, but not moisture. The tapes are used to secure the PTFE material to the housing itself and provide an air- and water-tight barrier. This solution also allows electroniccomponents under the hood to breathe. This is a growing application area being driven by the adoption of end use of EV batteries.
- Seat heating: High-performance bonding tapes are used in the manufacture and assembly of vehicle seat heaters. The complex open cell materials need to be bonded to the seat,as well as be able to withstand high temperatures.
- Sheet metal and interior vibration damping: Some vehicle applications are more demanding than others for pressure sensitive materials. Specifically, body-in-white soundBond damping material needs to bond to oily metals as well as survive phosphate baths and paint shop oven conditions. The Avery Dennison soundBond solution was designed to meet these requirements while also reducing weight as compared to LASD or butyl materials.
- Foam bonding: Pressure sensitive adhesives are used to attach foam to reduce noise, vibration and harshness.
AI: What are the main automotive industry trends driving the increased use of high-performance tapes?
VanHaerents: A significant trend is the need to increase fuel economy / electric vehicle range. Electric Vehicles (EV) have a unique set of requirements compared to vehicles with internal combustion engines. You have the white noise of the engine with regular cars that you don’t have with EV cars, but passengers are still affected by the sounds of road and structure-borne vibrations that require adhesives for noise abatement. The reason adhesives and tapes are key is due to the fact they are lighter and more noise resistant than heavier metal fastenings.
Then there is vehicle light weighting using LSE plastics – different components that were historically made of steel or aluminum are now made of plastic featuring lower surface energies. Tapes or adhesive
chemistries have been changing in order to meet the difficulties the lower surface energy materials present when it comes to bonding.
When steel is used, it’s being down-gauged to a thinner steel for lightweight vehicle construction. Adhesive tapes are used to dampen noise and vibration that come with thinner metals.
AI: What new applications are you working on?
VanHaerents: Our team has been developing an EV battery portfolio that will be formally introduced later this year. In this area flame retardancy is extremely important. Accordingly, we will be seeking the important UL™ 94 V-0 rating for burning and afterglow of materials for these products.
Within that portfolio are:
- Solid state lithium-ion batteries (LIB) adhesives tapes: Flame-retardant tape which prevents thermal runaway. If a LIB gets punctured or malfunctions, they can heat up beyond 1,000° C and catch fire. Runaway protection is primarily provided by ceramic materials that are adhered to battery cases, battery modules and battery cells themselves
- Cell to cell bonding: This involves bonding aluminum encased LIB cells together with flame-retardant pressure sensitive adhesives together, within the battery module
- Pouch cell cushioning: This involves bonding of different layers of compression pads between pouch cells. When the pouches are charged, they expand so they need to be encompassed with something that provides compression to the polyester bags that hold the electrolyte and cathode anode. The PSA bonds the compression foam to the polyester pouch cells
- Flexible busbars laminates: Flexible busbars consist of electrically conductive ink protected by a number of layers of flame-retardant PSA adhesive and laminated with PET to protect it electrically and thermally around the busbar.
More Stories
MESSRING completes new crash test facility for Mahindra in India
ROHM Develops an Ultra-Compact MOSFET Featuring Industry-Leading* Low ON-Resistance Ideal for Fast Charging Applications
More than 30 of the top 50 global suppliers have production facilities in Turkey