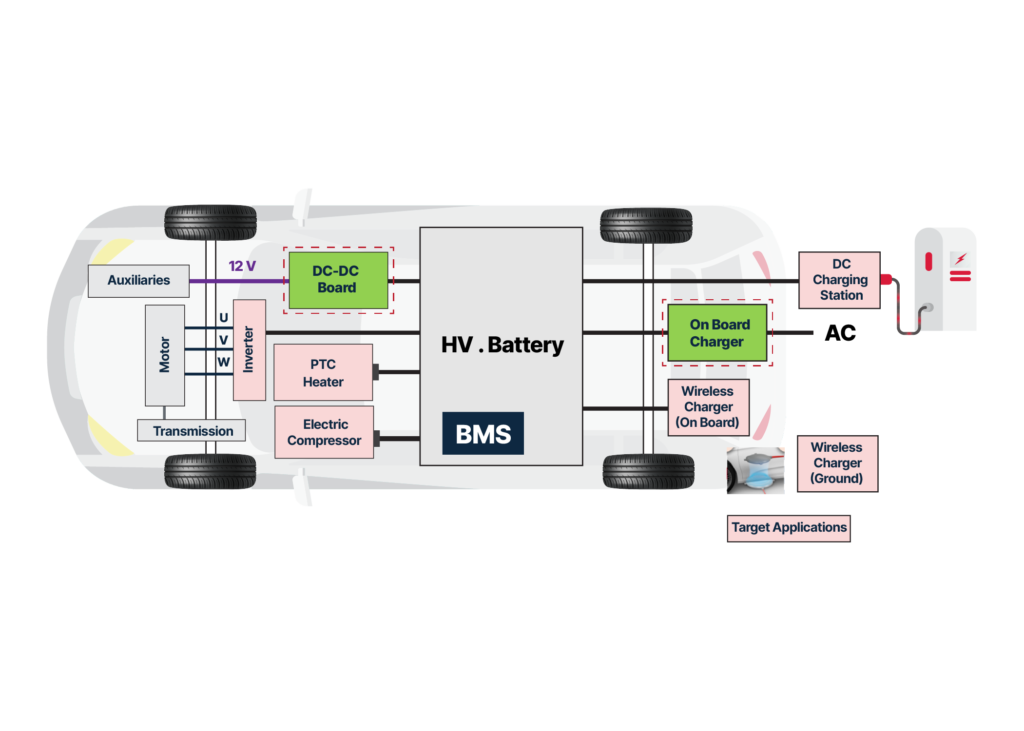
Industry’s Changing Needs
The rising use of high-voltage electric vehicle (EV) automobile onboard chargers, DC-DC converters, solar inverters, and energy storage has resulted in a demand for systems with improved energy efficiency, power density, thermal conductivity, and compliance with electrical safety regulations. Low-loss, high-thermal performance silicon carbide (SiC) metal-oxide-semiconductor field-effect transistor (MOSFET) devices are an ideal solution. This is because they are more efficient, more thermally conductive, and able to operate at higher switching frequencies than silicon-based devices. Conventional packages for SiC MOSFET include through-hole type and surface-mount type devices such as TO-247 and TO-263. The recent trend of integrating SiC MOSFET transistors into topside-cooled surface-mount packages can provide even better thermal management options and facilitate the automatic assembly process.
The Need for Safe, Reliable, and Efficient High-Voltage Energy Components
Advancements in renewable energy, automobiles, and other technology are defining a future in which we will generate, store, use, and rely on electricity in a number of new ways. The devices and appliances that are driving this change — EVs, solar power systems, and more — require high-voltage power converters, which in turn comprise several internal and critical electronic components that perform the power switching function. This trend has resulted in a demand for safe, reliable, low-loss, efficient, and thermally conductive high-voltage power switches for:
- EV automobile onboard chargers: Converts grid-based and other alternative current sources into the direct current required to charge an EV’s battery. Increasingly, these chargers come with bidirectional capabilities, allowing energy to be returned from the EV battery to provide power to a grid, home, appliance, or another EV.
- DC-DC converters: Electronic devices and circuits that convert the high voltages from an EV battery to a lower level (e.g. 12V) to power the auxiliary loads in the vehicles.
- Solar inverters: Converts the DC-based clean energy captured directly by solar panels into the standard AC power used by commercial and consumer infrastructure such as homes and businesses. Energy captured by solar technology would be mostly unusable without this critical component.
- Energy storage systems: Traditionally only seen in large-scale industrial capacities, the ability to store electricity has become more common as a number of consumer and professional battery-powered and renewable-energy devices are now on the market. Examples include home batteries for excess solar generation, transportable or handheld backup generators, and recreational power supplies.
Figure 1. Example of electric vehicle power system architecture
Because of the technology requirements, complexities, and safety compliance issues that must be addressed in such systems, traditional silicon-based power switches are increasingly challenged by advanced semiconductor materials for these kinds of use cases. In particular, SiC MOSFET, a highly efficient power switch made of a wide bandgap semiconductor, are ideal solutions for such power converters because of their higher efficiency, and ability to operate at higher switching frequencies.
Figure 2. Advantage of SiC over Si for high-voltage power switching devices
SiC MOSFET: Low-Loss, High-Frequency Power Transistor Performance
ROHM has been continually working to accelerate the performance and adoption of SiC MOSFET transistor technology since its research into the technology more than two decades ago. From the first mass production of full SiC power modules in 2012 to its low-loss devices of today, ROHM has crafted technology and processes to meet industry’s ever-changing needs. Having transitioned from the planar gate structure used in its earlier generation devices, ROHM’s 4th generation SiC MOSFET is designed with a double-trench device concept to allow for a drastic reduction in specific on-resistance and switching losses.
Currently offered in a complete lineup of 4th generation standard discrete products at both 750 V and 1200 V, the benefits and improvements seen in this generation also include a high gate threshold voltage. This is to prevent unintended shoot-through current during switching, and enable safe gate driving without a negative bias requirement. A unique MOSFET cell design improves the trade-off relationship between short-circuit withstand time (SCWT) and specific on-resistance, reducing the possibility of component damage if a short circuit event should occur. When compared to the previous generation of equal chip size, the 4th generation devices provide the following benefits:
- 40% reduction in on-resistance
- 90% reduction in reverse transfer capacitance (Crss)
- 15% reduction in output capacitance (Coss)
- 50% reduction in switching loss
In addition to the industry-standard TO-247 and TO-263 type products, ROHM has now integrated these transistors into topside-cooled surface-mount packages to better facilitate the automatic assembly process and to provide additional improvements to thermal efficiency and thermal management options.
Figure 3. ROHM’s topside-cooled surface-mount devices (TSC3PAK) feature significantly longer creepage distance than competitor products and support high-voltage electrical safety standards without additional insulation measures
Combining Topside-Cooled Package with ROHM’s Gen 4 SiC MOSFET
Topside-cooled surface-mount devices allow for the same automatic assembly as conventional surface-mount device products, with the added benefit of dissipating heat away from the primary circuit board (PCB). A conventional surface-mount device has a heat dissipation pad facing the PCB, creating challenges and complexities for its thermal management, whereas a topside-cooled device allows the heatsink to be attached directly to the thermal pad area. By utilizing this thermal-friendly topside-cooled design, ROHM has built upon the performance advantages of its 4th generation SiC MOSFET technology. Its topside-cooled SiC MOSFET packages offer excellent electrical and thermal performance, compatible pin layout with other products on the market, and a significantly more usable creepage distance design. They are AEC-Q101 (automotive) qualified and suitable for onboard chargers, DC-DC converters, and other applications. Key benefits and specifications of the packages also include:
● 750 V 13~65mΩ and 1200 V 18~90mΩ products for industrial and automotive applications
● Compatibility with existing on-market products, allowing sourcing without PCB redesign
● Convenient thermal management and assembly
● Supports automatic assembly and improved heat dissipation
● Low RonA reduces cost and conduction loss
● Low switching loss
● Long creepage distance supports high-voltage design such as 800 V EV onboard chargers
● 1200 V class devices can be used in pollution degree 2 environments at 800 V VRMS without extra insulation measures
Figure 4. TSC3PAK combines the advantages of automatic assembly as conventional SMD packages and the direct heat sink attachment as THD packages
Assembly Considerations for TSC3PAK
Engineers often face the challenge of coplanarity for components when using multiple discrete devices on a circuit board. Due to package height tolerance, heatsink flatness, and other factors, a gap exists between the top of the device and the heatsink. This gap could jeopardize thermal conductivity. To mitigate this challenge, an effective approach is to use a thicker, softer thermal interface material as the contact layer to the heatsink. Additionally, most applications require the heatsink to be electrically isolated from the device electrodes, including the drain-connected heat dissipation pad on the top of TSC3PAK. To ensure optimal insulation performance, it may be necessary to insert an isolation foil or ceramic plate in addition to the thermal sheet. Here, the ceramic plate is often a preferred option for its lower thermal resistance, as shown in the figure below.
Figure 5. Assembly example of TSC3PAK to a heatsink using ceramic plate isolation
Furthermore, the assembly method for TSC3PAK varies by application and mechanical design. Given this, the creepage and clearance distances should be carefully evaluated between the package pins and the heatsink based on individual cases. Optimal interface materials should be selected to provide electrical isolation as well as desirable thermal performance. To support these needs, ROHM has created TSC3PAK application solution guidelines and provides engineering assistance to customers for specific mechanical designs, along with material product recommendations.
Meeting the Challenge
The rising demand for high-voltage systems must be met, but with components designed for energy efficiency, reliability, convenient thermal management and assembly, and electrical safety compliance. ROHM’s topside-cooled surface-mount SiC MOSFET devices are designed to meet this challenge, providing industry with low-loss, high-thermal performance, and safe solutions for the most demanding high-voltage energy systems.
Figure 6. ROHM offers a complete lineup of discrete SiC products based on the 4th Generation SiC MOSFET technology, including the latest topside-cooled TSC3PAK package
More Stories
What You Should Know Before Filing a Car Accident Claim
Injured in a Car Accident in St. Louis? Here’s What to Do Next
Historic Sportscar Racing (HSR) and Goodyear Announce Multi-Year Partnership