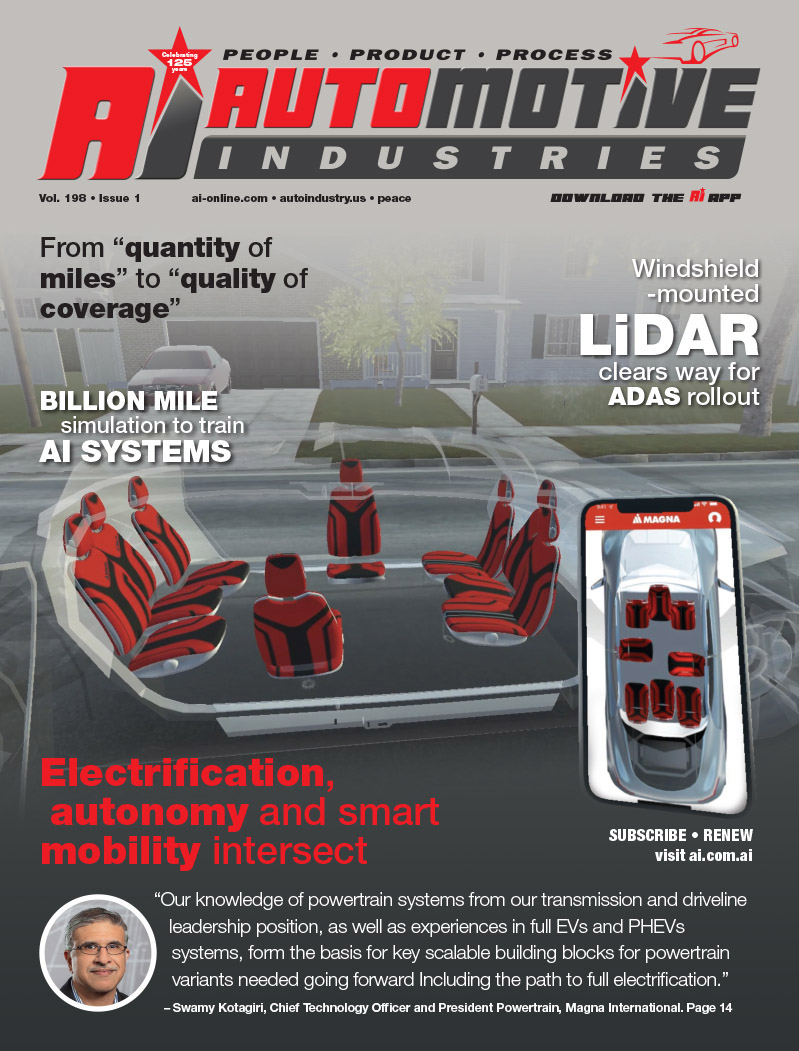
Ubisense has successfully completed the implementation of a new Tool Assistance System (TAS) at BMW’s production facility in Regensburg. TAS is based on the Location Identification System, which, as the name implies, is designed to locate and identify production assets. LIS/TAS has been developed jointly by Ubisense and IBS AG and is the result of bringing together the Ubisense real-time location system
(RTLS) and the IBS software systems, which provide the link between the location system and the existing BMW IT environment.
The Tool Assistance System rolled out in Regensburg provides automatic recognition of the vehicles being assembled as well as automatically detecting their proximity to production automation equipment such as intelligent tools and test equipment. TAS eliminates both the need to scan barcodes on vehicle work-orders, in itself not a value adding activity, as well as manually generated defects arising from scanning the wrong asset. The system works by evaluating the spatial relationship between production automation systems and the vehicles continuously in real-time. A positive “relationship event” is generated when a mobile tool enters a pre-defined zone around the vehicle or when a vehicle enters a zone around an item of automation equipment.
LIS/TAS is fully integrated into BMW’s production IT environment via the IBS Communications Platform which provides all the necessary interfaces to the relevant systems. In particular this includes the administration of the tools and vehicles as well as passing on the tool control events via IP telegrammes. A relationship event causes a new vehicle-specific program to be loaded into the tool or starts an automation system with the correct program for the particular vehicle detected. Typical tools and equipment in this context are torque tools, riveting hammers, diagnostic equipment, and programmable logic controllers.
The system is in production across the entire Regensburg assembly plant where around 120 tool systems are used to produce approximately 1,000 cars per day. The vehicle location in 3D is performed in real-time via Ubisense tags located on the cars. These tags are small transponders which are located using ultra-wideband radio technology by sensors mounted at fixed locations along the production line. The location and identification information is analysed for relationship events and the information passed on directly to the BMW IT environment. Ultra-wideband technology enables high precision location by transmitting extremely short pulses with very low energy (less than 0.1 milliwatts per m2) which means there are no negative effects on other systems or the health of the staff.
“The introduction of LIS/TAS has resulted in the elimination of the need to scan vehicles in order to identify them”, comments Andreas Lehner, project manager at BMW in Regensburg. “All the project objectives have been met on time and within the planned budget. From the standpoint of value creation, the project is a complete success”.
Richard Green, CEO of Ubisense, is very pleased with the results achieved. “Ubisense, together with our partner IBS, is the only RTLS vendor able to fulfil all BMW’s requirements and LIS/TAS is a unique tool for the automotive industry. We have here a clear differentiator and are delighted with the praise from BMW.”
More Stories
Hexagon’s MAESTRO reinvents CMM systems through digitization
Avery Dennison PSA tapes support rapid evolution of EV batteries
BRANO and DOMO join forces to replace aluminum with TECHNYL® polyamide