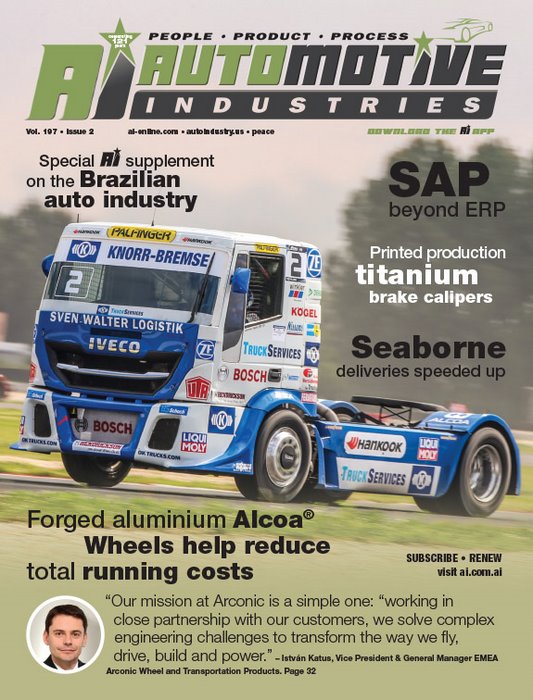
Automotive Industries (AI) asked István Katus, Vice President & General Manager EMEA Arconic Wheel and Transportation Products what the trends are.
Katus:We see a number of trends that will certainly shape the commercial vehicle sector going forward.
In the medium term, the trend remains increasing the efficiency of road transport and enable further CO2 reduction. Road freight transport accounts for around 6% of the EU’s total CO2emissions and is growing. The EU has a stated goal of reducing overall CO2emissions by 30% by 2030.
They will not succeed without seriously tackling transport. This is likely going to mean further implementation of a wide variety of fuel saving (support) technologies such as TPMS, aerodynamic improvements, alternative powertrains with the current focus on electrification, connectivity – with the help of big data – leading to vehicles constantly communicating with each other and, to make this all possible, a continued focus on light weighting.
In the nearer term we detect an increased interest in weight reduction as a means for fleets to improve their financial performance. Euro VI added 125kg to the average truck and reduced its payload capacity by an equal amount. Fleets need to cut as much weight as possible to regain that lost revenue generating capacity. We have seen the penetration of Alcoa Wheels into the market grow rapidly in the last years as fleets look for ways to cut weight.
Other trends that are brought into the spotlight are fuel saving, durability, sustainability, reduction of the total cost of ownership (TCO) and tire wear. All these topics are in one way or another connected to each other. TCO can be brought down by reducing the number of wheel and tire replacements, as well as through fuel savings.
AI: Arconic recently announced the building of a new wheels manufacturing plant in Hungary. What would the expansion bring in terms of capacity and production?
Katus: Due to the increased focus on light weighting and the ongoing growing demand for Alcoa Wheels by the market we decided to expand the current production facility in Hungary. It will significantly increase Arconic’s capacity to produce forged aluminum Alcoa Wheels. The US$130 million investment will enable us to double our capacity in Europe over time, to cater for growth in key markets in Europe, Latin America, Australia and Asia.
This greenfield expansion will also positively influence Arconic’s footprint in Székesfehérvár. Production is expected to begin at the end of 2019. Arconic’s Wheels business entered the commercial transportation market in Europe 22 years ago with just 32 employees, and has grown to more than 500 today in Hungary. The new facility is expected to bring approximately 200 new jobs to the region.
AI: There is a new wheel in your product portfolio. What are the benefits and who is it for?
Katus: We indeed recently expanded our European product portfolio with a new Alcoa Wheel; 19.5”x14.00” with 120 mm
offset. This wheel is indispensable for the segment of volume transportation. What makes this wheel so distinctive is that it is the
lightest in its class. It only weighs 21.6 kg. Steel equivalents vary around 44 kg. The Alcoa Wheel 19.5×14.00 offset 120 is brought to market in 2 finishes; LvL ONE® and the easy to maintain DuraBright® EVO.
AI: What other innovations can we expect from Arconic?
Katus: We are continuously working on new developments and product launches. Innovation is in our DNA. Particularly in the aerospace and ground transport markets we are currently bringing various innovations to the market such as next
generation Micromill® materials, various bonding techniques (Arconic 951 / RSR joining system), aluminum-lithium alloys, new
commercial vehicle wheel models (backed up by our recently announced significant expansion investment in Hungary) as well
as a significant drive to offer 3d printed durable and high quality printed parts to aerospace customers.
AI: What is the future of metal 3D -printing powders and processes and what can be achieved?
Katus: With the innovation of our metal 3D -printing powders and processes, we’re pushing the boundaries of production technologies for aerospace’s – and other markets’ – highperformance components. We have deep expertise in metal alloy development as we have invented most of the aluminum alloys used in aerospace today.
We can rely on a 100-year history in aluminum metal powder production, primarily for rocket fuel, paint and other products.
We bring a century of traditional manufacturing experience required to design and produce aerospace parts—
both directly with 3D printing machines, or by combining additive and traditional processes through our patented Ampliforge™
process. We also offer advanced processing technologies, such as “Hot Isostatic Pressing”, to increase the strength and durability
of components. And once the parts are machine-finished to exact specifications and checked for mission-critical quality, they’re
supplied and fitted to the world’s most advanced commercial aircrafts and ground transport vehicles.
AI: What’s next for Arconic?
Katus: Our mission at Arconic is a simple one: “working in close partnership with our customers, we solve complex engineering challenges to transform the way we fly, drive, build and power.”
Sometimes this means pushing great advances in groundbreaking techniques and technologies, whether that be our world-leading work in 3D printing or our research into robotics, big data and AI. At the same time, we continue to be very much
aware that it’s also the small, incremental advances that can have a big positive impact on our customers’ businesses.
Light weighting commercial vehicle components through the transition from traditional materials to aluminum is one of these
examples. By “simply replacing” a heavy component – such as a steel wheel – with a lighter and stronger, forged aluminum alternative we offer the potential to drive truly remarkable improvements in fuel efficiency, safety and lifecycle cost reduction for commercial vehicle manufacturers and operators. At a time when cost is still king, and efficiency is the name of the game, it is these types of innovation that the industry will continue to be focused on.
More Stories
What to Do After a Motorcycle Accident to Protect Yourself
Injured in a Motorcycle Crash? Talk to an Attorney Now
Danisense launches ‘Online Calibration Portal’ to offer brand agnostic calibration services for current transducers and smoothen the whole process