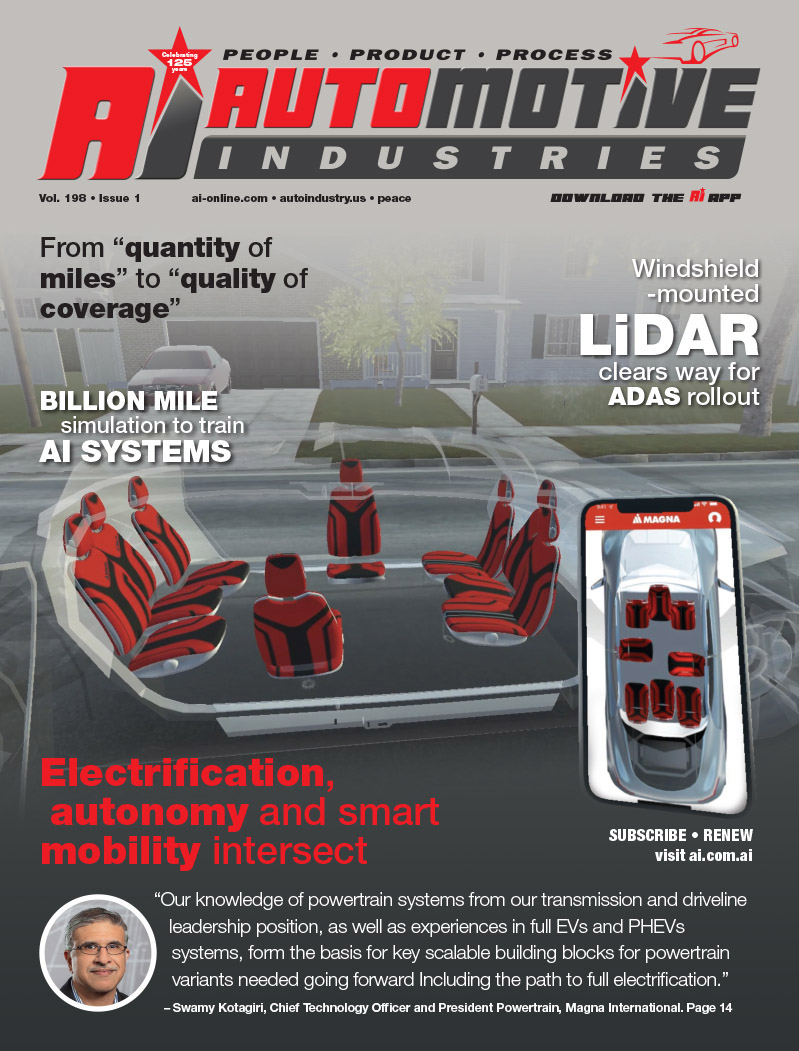
Current trends in automotive engineering include modular technology and mechatronics.
As a leading global supplier of engineering plastics, Ticona is involved in both developments. Automotive Purchasing News talks to Ulrich Haack, head of the Application Development Team, about innovative problem solutions achieved with Ticona high-performance polymers.
Automotive Purchasing News (APN): The content of engineering plastics in motor vehicles is continually increasing. Where can Ticona polymers be found?
Haack: Virtually everywhere. Under the hood, in vehicle interiors and also in exterior applications. Let me point out some examples: speaker grilles, fuel feed units, filter housings, gear selector components, tank filler necks and many other parts are moulded from our Hostaform (POM). Direct ignition modules, windshield washer arms and fuse holders are made from Celanex (PBT). Dashboard carriers and underbody protection are produced from the long-fibre-reinforced thermoplastics (LFT) Celstran and Compel. Because of its excellent heat resistance, Fortron (PPS) is suitable for intercoolers, water pumps and throttle valves. Vectra (LCP) is used in many electrical applications, in solar sensors for example (see Figure 1) or connectors. The list of examples could go on and on.
APN: What makes engineering polymers the preferred material for these and similar applications?
Haack: There are three key criteria. Firstly there is a general requirement to reduce weight (and therefore emissions). Secondly, more cost-effective production and assembly techniques must make their contribution to cost saving. Thirdly, innovations are needed to drive development forward and gain competitive advantages. If you want to save weight by replacing metals in applications involving harsh service conditions, such as high temperatures, aggressive fuels or high impact stresses, high-performance polymers are often the only solution. Their properties can be optimised for specific requirement profiles and to a certain extent they can be tailored to the application.
APN: Can you give some examples of application-specific optimisation of polymers?
Haack: Let me take our polyacetal Hostaform as an example. In a two-year development project, working closely with Siemens-VDO, we developed a hot-diesel-resistant Hostaform grade for the latest diesel engines (common rail and pump jet technology), which is now used in these modern fuel feed units. But at the same time there are also special grades of Hostaform that are modified to meet, for example, the strict requirements of VDA 275 (German Association of the Automotive Industry guideline) on emissions and odour in vehicle interiors.
APN: You mentioned cost reduction. What role does modular technology play in this?
Haack: This is an important trend that affects virtually all areas of a motor vehicle. By using modules containing a wide variety of different functional elements integrated into a complex component that has been developed and produced by a supplier, automotive manufacturers can achieve considerable cost savings. Modular technology relies to a very high degree on engineering polymers. They can meet crucial criteria such as high heat and chemical resistance, offer good slip properties and are ideally suitable for efficient assembly methods. For this reason, Ticona high-performance polymers are used, for example, in front end and fire wall modules and electric gas pedal modules.
APN: Are door modules another example?
Haack: Yes, you are quite right. Here we are very closely involved with our plastics. Let me give you an example. In the new Jaguar XJ, the door module carrier plates are produced from long-fibre-reinforced Celstran (see Figure 2). Moulded parts made from this LFT have high dimensional stability and excellent mechanical properties. They are a match for metals in terms of load bearing capacity but are considerably lighter in weight. They also enable important functional elements to be directly integrated as, for example, the door opener and speaker in the door module for the Jaguar. Celstran fulfils other important criteria specified by Automold, the system developer based in Gloucestershire, England. The Celstran door module acts as a water barrier, a job normally performed by plastics film, and gives the door additional torsional rigidity.
APN: Now to the buzz word “innovation”. What predominant trend can Ticona identify at present?
Haack: It is difficult to speak of a general trend here. No area is safe from new ideas – and that is a good thing. The potential of mechatronics is impressive. The intelligent combination of mechanical engineering, electronics and software is continually leading to innovative solutions in applications ranging from vehicle safety through drive technology to telematics and comfort. Think of airbag sensors, distance radar and electric steering and braking – all these are mechatronic problem solutions requiring special technology, which can very often only be implemented by using engineering plastics.
APN: Can you describe a specific example of a mechatronic application for us?
Haack: Active cornering headlamp systems that follow the steering movements of the driver and ensure better illumination on corners are attracting considerable interest at present. These active cornering lamp systems from lighting specialist Hella are being fitted in the new Mercedes Benz E class and the new BMW 5 series. The key component in the cornering lamp is a swivelling headlamp projection module controlled by a microcomputer. For the swivel mechanism (see Figure 3), Hella uses liquid crystalline Vectra (LCP), a polymer which is new to this area of application. It withstands the high temperatures to which the high-precision gearwheels are exposed. Vectra is also used in this headlamp system to produce the slide bearing for a movable shutter that switches between low and high-beam mode.
APN: As a polymer manufacturer, how closely are you involved with new processing technologies?
Haack: Very closely, because we are always looking for possible advantages in this area. Two years ago, for example, we launched the first PPS blow moulding grade for commercial application. With its very high melt strength, Fortron 1115LO can be processed on conventional blow moulding machines into complex blow moulded parts, which are used, for instance, in hot-air ducts for diesel engine turbochargers (see Figure 4). Another example is microcellular foam technology, in which minute gas bubbles are introduced into the component, therefore cutting material consumption and weight. At the same time, this also often enables production tolerances to be significantly reduced. We have tested this process with our own MuCell machine, adjusted the parameters to suit our own materials and passed on our experience to customers. Our machines are, of course, also available for customer trials.
More Stories
8 Best Plastic Welding Techniques for Automotive Manufacturing
5 Big Reasons to Choose LED Bulbs for Your Car Headlights
How much does it cost to ship a car on Amtrak Auto Train?