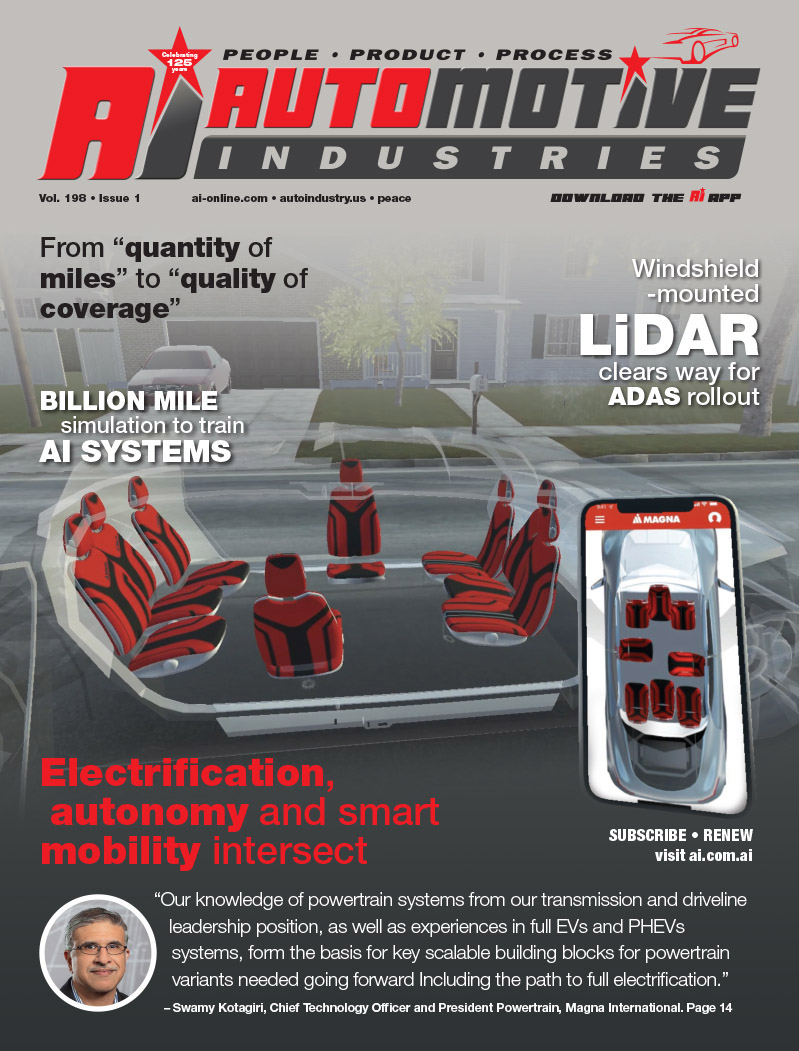
Automotive manufacturers around the world are focused on implementing the “Lean” concept into their plants and work forces. Toyota is the wellspring of the Lean concept, and has been proving that reducing waste and improving quality are not mutually exclusive. In fact the two outcomes can support each other.
Why stop the application of “Lean” at the entrance or exit to a manufacturing plant? says Gary Kowalski, chief operating officer of Menlo Worldwide, the supply chain management arm of U.S. firm CNF, Inc (NYSE:CNF). We think Lean has application throughout any supply chain. And Menlo has proven that by applying it in assignments we receive from our clients in the automotive industry.
The lean concept revolves around the continuous involvement of employees in identifying opportunities to remove waste from a process. The company says that the key to making “Lean” work is a formalized plan and a long-term commitment to constantly searching for improvement. The big hits come early. Continuously finding and modifying the small, incremental improvements is where the process and the commitment come in.
The assumptions in a Lean environment are: 1) the market controls price, 2) the company controls cost, thus cost is easier to control than price so profits are increased by reducing cost/waste. You cant do the same thing over and over again and expect different results. . Lean thinking is out of the box thinking.
In a traditional environment Price = cost + profit and profit is increased by raising price.
In a Lean environment Profit = price less cost.
The first thing we did was make a management commitment to the Lean philosophy, says Kowalski. We hired Jeff Rivera, an engineer with strong background and experience in Lean Manufacturing in the auto industry and had him lay out all the rules for the process. The company started by training their warehouse operations manager in the process (the company also refers to it as a philosophy).
The best way to see how “Lean” is practiced is to review the every-day procedures at the Menlo Worldwide warehouse located in Brownstown, Michigan. Its a 265,000 sq. ft. facility located just south of Detroit to serve clients in this key automotive city. Its one of eight Lean warehouses that Menlo maintains at strategic locations throughout the United States and Mexico. The Brownstown facility is a multi-client operation and currently houses programs for four separate clients. All of the clients are in the automotive business.
Menlos Brownstown operations manager Bob Blevins says his first task was to train his staff and then the warehouse employees. Success is dependent on total employee involvement. The workers who actually perform the every-day tasks are the eyes, ears and ideas for eliminating waste. We had to start by giving the workers time to talk about it. After the first idea was volunteered then the lights went on and others began to understand how the process worked. says Blevins.
Within the Brownstown facility there are work teams assigned to each client. The tasks and the product lines for each client can be quite different. Every Wednesday the facility shuts down for one hour to focus on continuous improvement opportunities. During that hour a team leader facilitates the discussion and the voices of all associates are heard. The one hour of down-time displays the level of commitment of the management team to empower associates to identify and eliminate wastes. Employee empowerment and buy-in to change are critical to sustaining improvements long term.
After a project for waste elimination is agreed to, a study team of employees is formed and the real work begins. Data documenting the targeted waste is gathered. Statistical tools are used to chart and define opportunities for improvement. Cost reduction details are calculated and compared to any possible investment that may be required to achieve the savings. Any recommended change must produce a return on that investment
The company says it helps the study teams with the statistical tools by providing technical help when needed, but has also trained workers in the use of statistics so they understand the process and take a greater role in the analysis. We don’t hire too many college graduates with mathematics degrees to work in our warehouse, says Blevins But you’d be surprised how the basic math from high school takes on a new meaning when it is translated into real job activities. The involvement, excitement and ownership is fun to watch.
Lean leadership vs. traditional leadership is very different. Envision the traditional organizational pyramid turned upside down with customers at the top (widest part of the pyramid), then Hourly and Salaried workers at the bottom in the rest of the pyramid. Supervisors and other leadership are actually outside of the pyramid. In a traditional pyramid the order is: Organizational Head, Senior Staff, Middle Management, Supervision then the Hourly and Salaried workers at the bottom, widest part of the pyramid.
The objective is to remove waste, not cost.
o Wasted movements
o Wasted time
o Physical/material waste
o Wasted protocol or procedures
o Reduce damage to products which end up as unusable waste
Sometimes the study teams find the answer to waste reduction may lie outside their warehouse. Packaging, storage patterns in containers, and product volume flows can all affect the time and process of receiving product into a warehouse. In these cases the team will draw up recommendations to send to the manufacturer and ask them to consider changes.
Other waste reduction opportunities may involve the packaging, protective dunnage, trailer loading pattern and timing for delivering parts to assembly lines or after-market parts distributors. The team will send its waste reduction proposals to those receiving products from their warehouse.
Were not bashful about sharing our teams recommendations with our clients, says Kowalski. And we dont have thick skin when it comes to receiving Lean recommendations from our clients. As a 3PL we aim to be an active participant in our clients supply chains. Its impressive how waste can be driven out when we communicate and cooperate.
RULES FOR MAKING LEAN WORK:
In a Lean warehouse mistakes are to be investigated (root cause analysis) and understood so that corrections can be made in a positive environment. Immediate feedback is given to the customer and Menlos hourly associates.
Change is best achieved by continuous improvement vs bold stroke approach
Every person in the warehouse is to be respected
Everyone in the warehouse can be a change agent and is expected to be one
o The on-floor hourly person is viewed in Lean Warehousing as a Doctor who operates and should be given the proper instruments to operate
There are stages to the process of change
o First awareness
o Understanding
o Commitment
o And finally habit
Lean Warehousings Fundamental Goal
Reduce the process lead-time associated with any process. Eliminating non-value added steps in the process will improve responsiveness, while reducing costs and improving quality.
Five step approach:
o Identify value from the voice of the customer
o Map the value stream for each product family
o Make the product flow
o So the customer can pull
o As you manage toward perfection (continuous improvement)
Lean Leadership vs Traditional Leadership
Is very different. Envision the traditional organizational pyramid turned upside down with customers at the top (widest part of the pyramid), then Hourly and Salaried workers at the bottom in the rest of the pyramid. Supervisors and other leadership are actually outside of the pyramid. In a traditional pyramid the order is: Organizational Head, Senior Staff, Middle Management, Supervision then the Hourly and Salaried workers at the bottom, widest part of the pyramid.
The Importance and Implementation of Standardization is Critical because
Standardization is a good training tool
Standardization is a very good way to identify waste
Standardization is a quality control measure to identify variation
Standardization helps to build a predictable process to meet the customers expectation
Standardization givers control to the planning process and integration process
Standardization allows for easy measurement against goal, establishes a baseline from which improvements can be made
Standardization allows for expectations to be set and measured
The Importance of Workplace Organization
Foundation to process stability
A place for everything and everything in its place
o Simple theory that saves steps, thus saves waste
o Treat operator like a doctor. A surgeon doesnt search for a scalpel, an associate shouldnt be searching for tools.
The Importance of Visual Process Management
Foundation to process stability
Critical part of continuous improvement process
Critical information shared with team, all on the same page all with same goals
Time Management Strategy
Is predicated on Takt Time which is the time available per day divided by the volume required by the customer per day. This determines task cycle times.
Allows management team to resource plan effectively and quickly shift resources as customer demand changes.
The Lean warehousing house
The roof of the house is comprised of:
S Service
Q Quality
D Delivery
C Cost
M Morale
Other Operating Terms
Kaizan- Japanese term for continuous improvement
Jidoka- to separate man from machine automation with a human touch
Genchi Gembutsu Go look. Go see
Kanban- Japanese term for a pull system, a signal that tells the upstream process that one more unit is needed for replenishment
Poke Yoke – Error Proofing- any change to a process or product that helps the operator reduce/eliminate the chance of defects.
More Stories
8 Best Plastic Welding Techniques for Automotive Manufacturing
5 Big Reasons to Choose LED Bulbs for Your Car Headlights
How much does it cost to ship a car on Amtrak Auto Train?