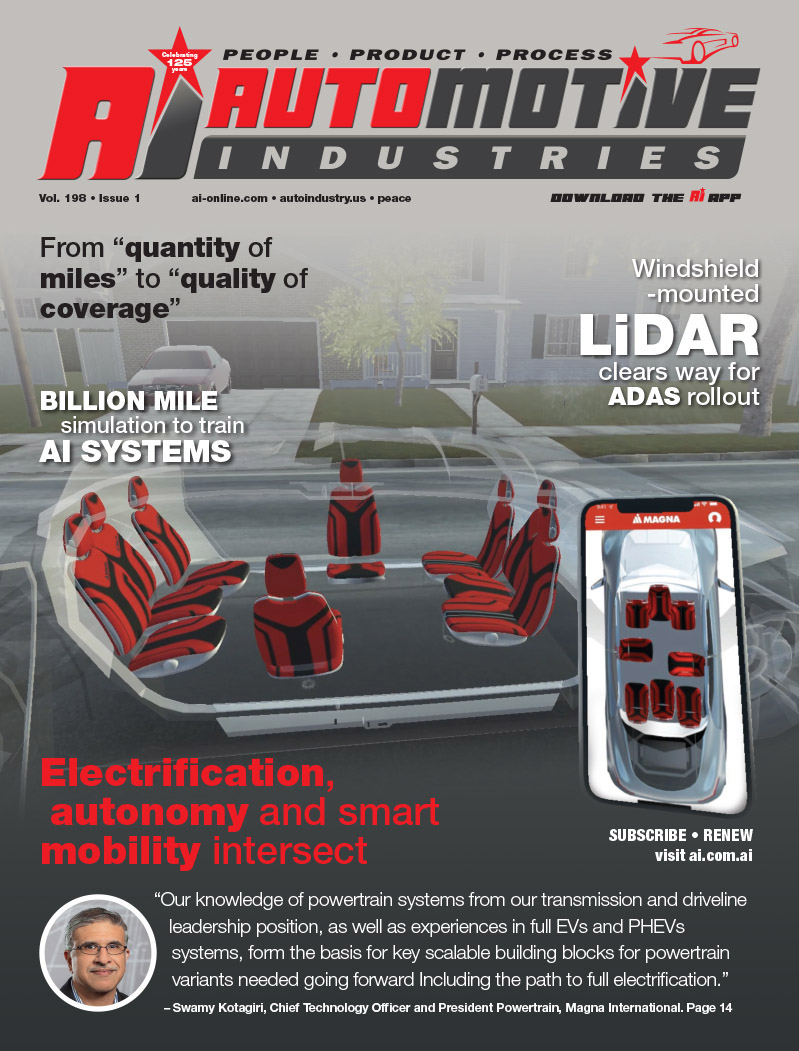
Telezygology and Textron team up to usher in the new age of point and joint.
“Picture an auto repair shop where you want to replace a body panel like a fender,” posits Seshu Seshasai, executive vice president of technology, Textron Fastening System.
![]() |
Chips embedded in the fasteners have individual addresses and respond to signals from a remote electronic tool. They assemble and disassemble on command and document each process. |
Think about an air bag assembly, an entertainment/ climate control stack, an instrument panel. Nest the parts together, give the command and all the parts are secured.
Again, no tools are required, no physical contact needed, no complicated assembly gymnastics to perform. Fasteners are non obtrusive and also tamper proof. You need the codes and protocols or nothing happens.
Potentially turning the world of mechanical fasteners upside down is a company named Telezygology, or TZ Inc. from the land down under in Sydney, Australia., which has teamed up exclusively with Textron Fastening Systems, Troy, MI, to bring this technology to the automotive sector on a worldwide basis.
“Our intelligent fasteneing technology represents the future of fastening, an all new way to design, assemble and service products,” said Rick Clayton, president of Textron Fastening Systems, at a recent press conference. “Intelligent fastening technology has the potential to be the fastening protocol for all automotive sub-assemblies.”
There is quite an array of technology and devices in this new fastening arsenal. There are simple fasteners in pin, strip or seal configuration that are locked by an energy source such as a magnetic field, infrared radiation or ultrasound. Energy causes the locking or unlocking to occur.
![]() |
Intelligent fasteners in airbags consist of shape memory alloys that return to a predetermined form when heated to a specific temperature. |
There are also interactive fasteners that add on-board processing power (a self contain chip) and software to manage the assembly/disassembly process. These can be networked or integrated into a wired or wireless network system.
Embedded microchips have secure addresses and respond only to encrypted signals, thus only accessible to authorized service outlets. Aftermarket implications are incredibly attractive for achieving OEM control.
Say goodbye to air bag theft. The stolen air bag could be rendered useless by unauthorized removal.
Fasteners can be internal and integrated with the part and allow pre-finishing of the part. Critical assembly sequences are reduced. Tool damage to the part during assembly is eliminated. The assembly process is de-skilled.
Further, they control the access and log of assembly/disassembly and service procedures. They speed assembly eliminating the need for fastener stations. They can monitor a part and log failure modes. They can provide secondary switching, say to hold a light in place and also turn it on and off. They facilitate part replacement or customization and reduce tool access space.
The interactive fasteners use various kinds of smart materials that change shape or material properties when stimulated with the application of heat or electric current. The types of smart materials include shape memory alloys, shape memory polymers, electrostrictive, magnetostrictive and piezoelectric materials. The most common will be shape memory alloys and polymers, it is thought.
“A new world is opening and we don’t see very many limitations. High temperature (above 150 F) is to be avoided with some types, but that’s about it,” Seshasai told us. “If you build these in at the basic design stage we can achieve a range of clamp loads that cover so many assemblies and joints.
“Then if one considers the end of life issues facing the auto industry, the green vehicle challenge, disassembly will be as easy as assembly. Those are the biggest benefits of this technology.” So like the ubiquitous beer can opener (aka: church key) of old, looks like screw drivers and such might soon be headed for some dusty shelf in the Smithsonian.
More Stories
8 Best Plastic Welding Techniques for Automotive Manufacturing
5 Big Reasons to Choose LED Bulbs for Your Car Headlights
How much does it cost to ship a car on Amtrak Auto Train?