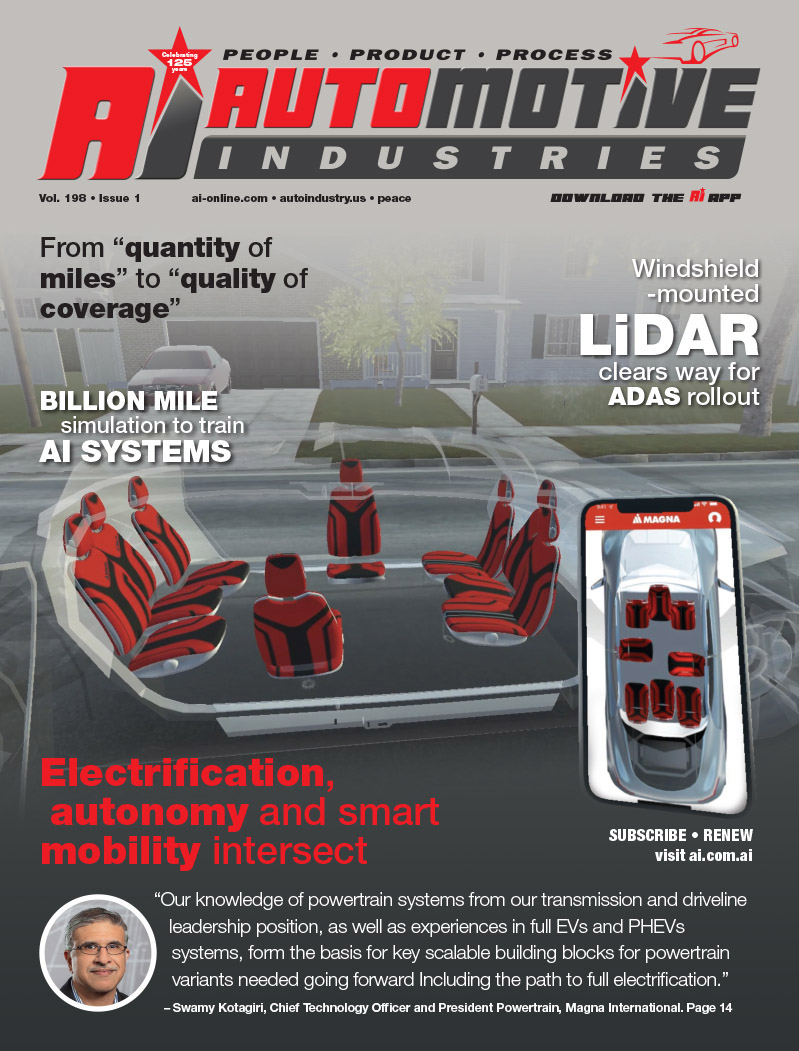
Heading into Fernando Alonso’s home turf and holding two of the top spots in a three-way tie for the 2007 Drivers’ Championship, Vodafone McLaren Mercedes is emerging as one of the teams to beat in 2007. Infused with comprehensive design modifications from more than a year of R&D and wind-tunnel testing, the Vodafone McLaren Mercedes MP4-22 is clocking top lap times, delivering consistent peak performance and leading the field in the race for this year’s Constructors’ Championship. Innovative solutions from Henkel play an invisible yet important part in this.
As an Official Supplier to Vodafone McLaren Mercedes, Henkel provides increasingly more products and technologies used to construct the Vodafone McLaren Mercedes MP4-22, helping the team to implement design modifications quickly and reliably. Throughout a 13-year association with the team, the number of different applications of Henkel products on the car has grown from around 50 to more than 300 today.
As part of a continuous testing program, Vodafone McLaren Mercedes engineers have discovered the optimal “grades” of innovative Henkel brand products for new applications — such as Loctite(R) 246, an adhesive that is specially sourced from the USA and currently used on the Vodafone McLaren Mercedes MP4-22 in twelve distinct applications on a variety of ‘exotic’ materials used in building the components of the car — from the brake pads, to the driveshaft, to the rear wing assembly. After thorough testing specified by Vodafone McLaren Mercedes engineers and carried out last year by engineers at Henkel in the UK, Loctite(R) 246 has helped the team solve a long-standing assembly challenge: securing components with an adhesive that is strong enough to withstand extreme conditions yet still allows for easy disassembly and re- use of components. Created by Henkel’s U.S.-based R&D team, Loctite(R) 246 exhibits superior resistance to high temperatures despite its medium-grade strength. The advantage is that engineers can replace parts easily using standard hand tools during a race weekend or at test sessions — without having to scrap the parts after removal and with the assurance that the replacements will hold fast for the duration of the race.
“In Formula One racing, change is a constant and innovation is a necessity,” said Martin Whitmarsh, CEO, Formula One, Vodafone McLaren Mercedes. “In such a fast-paced and unpredictable sport, it is all the more important to have reliability, flexibility and speed in engineering processes. Henkel provides Vodafone McLaren Mercedes with proven, innovative products and technologies that we can depend on to make modifications quickly and flexibly – whether in the race bays at the McLaren Technology Centre or at the circuit just hours before the car takes to the track.”
Speed, agility and reliability are important not only on the track. The perfect mix of aerodynamic performance for the straights and optimal downforce for agile and reliable cornering demands ongoing innovation. As up to 80 percent of a Formula One car’s grip is achieved by aerodynamic downforce, Vodafone McLaren Mercedes engineers continuously adapt the car’s bodywork to the unique characteristics of each track. This can include re-designing molded parts such as the front and rear wings to reduce drag on circuits with long straights or making modifications to improve downforce and grip for tracks marked by a mix of high and low-speed corners, such as Barcelona’s Circuit de Catalunya.
The Fast-Track and True Course of Ongoing Innovation
Henkel products and technologies play a key role in the team’s continual process of innovation to gain the competitive edge in aerodynamics. In wind- tunnel testing, Vodafone McLaren Mercedes engineers determine optimal aerodynamic settings using 60 percent scale models of the MP4-22, created with the help of the Henkel product line used in creating the racecar. For example, Loctite(R) 420 instant adhesive is used to bond plastic parts to the model’s rear wing. This low viscosity adhesive quickly “wicks” between the parts, leaving no excess residue that would affect the airflow during testing, enabling engineers to draw reliable results.
Design modifications resulting from wind-tunnel tests are then quickly executed on the car’s bodywork moldings, using Henkel’s Syncore(R) brand epoxies, which add stiffness to parts and only minimally increase weight. Henkel’s Hysol(R) EA9686 film adhesive is used in the “lay-up” of materials, in which patterns are cut to size to form specific parts. This Henkel product is chosen for its excellent reliability and resistance to the extreme conditions on the racetrack.
The newly modified car then takes to the track for testing before race day. Performance analysis of pre-race test sessions are passed on to the design team at the McLaren Technology Centre in Woking, England. If further modifications are necessary, engineers at the center quickly mold parts to the new aerodynamic specifications — and ship them to the circuit in time for the race. Through such continual modifications, by the end of any given race season, the car’s components can have changed by as much as 75 percent compared to those in the car that started the year.
“Like Henkel’s ongoing commitment to leading manufacturers in diverse industries around the world, our engagement with Vodafone McLaren Mercedes is more than a one-off contribution,” said Alois Linder, Executive Vice President, Adhesives Technologies, Henkel. “This team effort enables us to continually prove and refine the reliability and performance of Henkel products in a racing sport driven by continual change. It also helps us feed the insights gained into new product development and to further innovate the way we support companies of all industries with state-of-the art products, technologies and manufacturing processes.”
More Stories
8 Best Plastic Welding Techniques for Automotive Manufacturing
5 Big Reasons to Choose LED Bulbs for Your Car Headlights
How much does it cost to ship a car on Amtrak Auto Train?