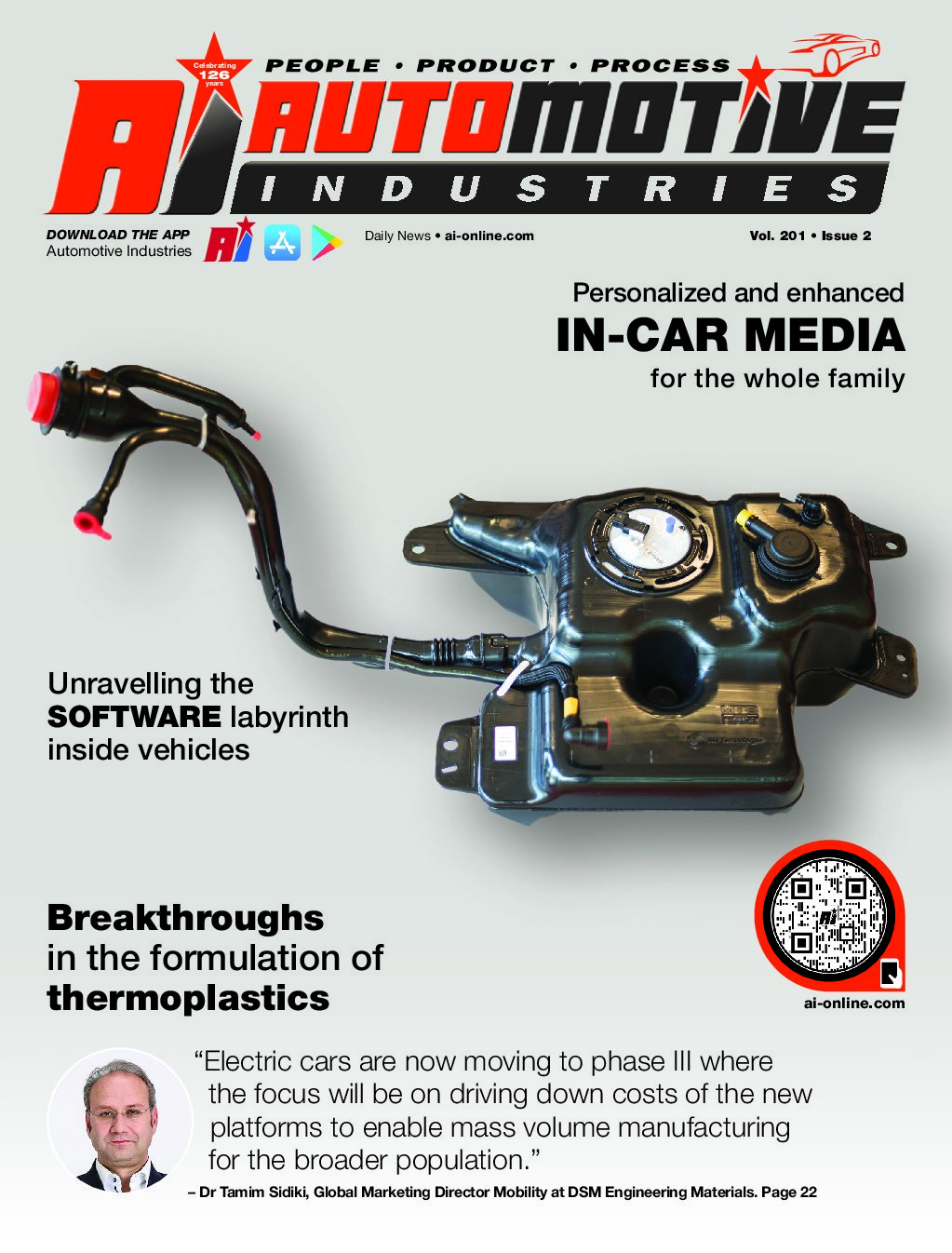

Breakthroughs in the formulation of high-performance and sustainable thermoplastics are supporting the move towards a new generation of electric, hybrid and fuel cell power trains. Specialist companies are investing heavily in the development of new formulations of polyamides, high temperature PAs and elastomers in order to help automotive companies meet emission and sustainability regulations and targets.
Automotive Industries (AI) asked Dr Tamim Sidiki, Global Marketing Director Mobility at DSM Engineering Materials, for his thoughts on prospects for the motor industry.
Sidiki: In the short term the industry is impacted now by all the geopolitical issues around the world. But, the geopolitical impact is just a temporary thing. Whether it takes one or two years, it will definitely disappear. Industry experts see unit sales recovering to the former pre-Covid status by the 2024 / 25 timeframe.
Technologically, the move towards connectivity and electrification is further speeding up. After initial feasibility proof in phase I and the launch of a few high-end expensive cars in phase II, electric cars are now moving to phase III where the focus will be on driving down costs of the new platforms to enable mass volume manufacturing for the broader population. This is vital as the prices of electric vehicles has risen over the past few quarters to the point where there maybe be some consumer resistance to purchase.
AI: What about hybrids?
Sidiki: Hybrid cars are an important intermediate step towards fill electrical cars and are very popular with consumers. DSM has partnered amongst others with Renault to develop the world’s lightest and most decomplexed gasoline tank for hybrid cars. Using Akulon® Fuel Lock, DSM’s high-performance ultra-low permeation and low-carbon-footprint PA6 material, the fuel tanks can be produced with a blow molding monolayer construction that significantly reduces weight versus any alternative metal tank and cost versus competing HDPE alternatives without compromising safety or risking additional emissions.
And the beauty is that it is a drop-in solution which provides a second life to the monolayer blow molding machines used for the manufacture of diesel fuel tanks. In most cases, the cost of these machines has already been amortized and rather than staying idle with the drop in Diesel demand, molders can re-use them to produce advanced gasoline tanks for latest generation hybrid cars.
AI: What about sustainability?
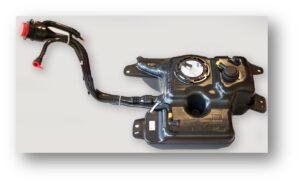
Sidiki: Sustainability used to be a nice differentiator companies could use as a marketing tool to boost their image while doing something good for the environment. But now it increasingly becomes a true qualifier. If you do not score high on sustainability, OEMs and also consumers will not select your solution.
Globally, Europe is currently setting the pace. It has overtaken even California in the US with the European Green Deal, as well as the strict regulations which are forcing the industry to move to electric power trains and to adopt more sustainable manufacturing practices. The Green Deal and the upcoming revision of the end-of-life directive are two key drivers.
As DSM we focus on sustainability via multiple levers, from biobased and biomass balanced materials to fully recycled materials. EcoPaXX for instance is a high-performance aliphatic, biobased polyamide that uniquely balances the benefits of typical short and long chain polyamides, such as low moisture uptake and high mechanical performance. EcoPaXX, which has been in the market for more than 10 years, has wide applicability and is especially popular as a PA66 performance booster since it can be processed in the same tools.
Recently we also launched a 100% bio-based PA46, the first high-temperature polyamide in the world. PA46 Stanyl® B-MB is a fully ISCC+-certified mass-balancing solution, and delivers exactly the same characteristics, performance, and quality as conventional Stanyl®. This is a full drop-in solution as no tooling or design changes are required and customers can immediately switch even for existing applications with existing molds.
So, companies can switch and score on sustainability without having to requalify the materials or applications.
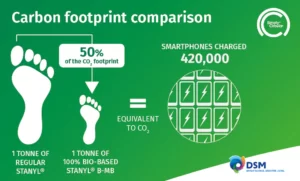
AI: What about the bus and truck sector?
Sidiki: Looking in into the transport industry as a whole, something like 25% of all emissions are produced by the transport industry. Within the transport sector, about 40% comes from buses and trucks. And it is easier to deliver on sustainability targets for trucks rather than passenger vehicles because volumes are lower, there are fewer players and the additional cost is less of a factor.
The transport industry is taking a multifold approach to sustainability. First, the powertrain is being electrified. This is where fuel cell technology is seen as a very, very strong value driver. I think the market is at this moment roughly about 50/50 in terms of fuel cell technology versus pure battery electric drives.
For fuel cells the choice of right materials is vital. Fuel cell systems need to use materials that are very pure and no hydrolytic or heat aging should occur. A fuel cell is nothing more than two cathodes with an electrolyte in between. If materials in contact with the media leach out ions, it leads to an efficiency drop and the membrane in-between can get clogged leading to a significant fuel cell performance drop over time.
So, it is super important to use materials with very low ionic leaching. DSM’s tailor-made 4080HRE Xytron PPS is the purest material solution on the market today and has the lowest leaching of all the materials that customers have tested within the PPS world but also in comparison to other suitable polymers.
Our low ion leaching PPS compounds support the entire fuel cell system, whether it is the, manifolds, end- and side plates or auxiliary components like humidifiers, dehumidifiers, or ion filters. The current transition to EVs is characterized by three phases.
In Phase 1 EVs were proven as a very feasible technical solution. Phase II saw the launch of various high end and very expensive models. With the recent steep raise in material cost, EVs are however not yet affordable for the broader population.
Phase III with the required transition to mass volume production will therefore require significant effort to reduce the cost of EVs and make them really affordable. One way to reduce the cost is to reduce the volumetric size of the e-axle.
By reducing the size of the e-motors while keeping its power the same, you save on space, weight and cost by taken out expensive metals and magnets. Such a downsizing will reduce the torque but increases the rotation speed of the motor.
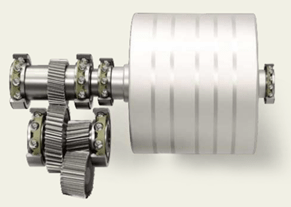
To achieve the same power levels, you need to increase the rotation speed of the of the motor. So, the next generation of EVs will have smaller e-motors running at much higher rotation speeds. From the present approx. 10,000 RPM, it goes to 20,000 RPM and above. This impacts on the bearing cages as the higher motor speed generates a lot of heat which can deform the bearing cage. Also, the used bearing lubrication needs to be suitable for such high speeds.
So, you need to have materials which have a very high stiffness over temperature. Our customers have tested various high performing materials and Stanyl PA46 has shown extraordinarily good performance. Its superior stiffness over density at high temperatures allows increase of rotation speeds up to 20.000 rpm without bearing deformations. Stanyl PA46 also delivers high ductility, excellent chemical and temperature resistance for the dedicated high-performance greases used with continuous use temperatures up to 180°C
AI: Tell us about your material advisor that was recently launched.
Sidiki: The Material Advisor is an interface between our customers and us. It provides fast-track material advice in five minutes by asking eight questions.
Our objective is to allow our customers to reduce costs and shorten time to market by cutting down development times and avoiding multiple design iterations by getting the material right first time. The material advisor was developed after our research found that about 70% of engineers prefer a self-service option to face-to-face interactions.
Engineers may find inspiration in a lab over the weekend or late in the evening. Our material advisor is available 24/7 and 365 days a year to provide support ranging from a simple material catalogue to accessing dedicated material data like strain-stress curved or carrying out various simulations. This data will give the engineer a feeling of how the material will perform under their application requirements.
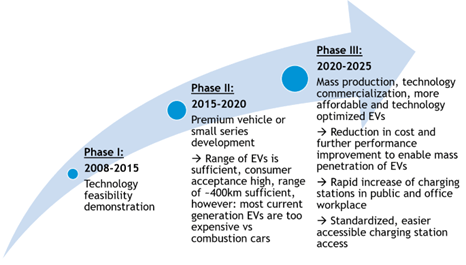
It is an intuitive, easy-to-use tool, which provides engineers with reliable recommendations to guide them to selecting the best materials solution for the application they are designing. We start with a checklist based on the set of questions that the customer needs to answer for the application. This tool recommends the material and the compound that the engineer can start working with and testing.
AI: What next for DSM?
Sidiki: We will continue with the inspiring innovation and strong application focus path that we are on, and I think we will become even more inspiring in the future by increasing our digital service even more. We will have many more new technologies and applications to offer. There is a strong focus on the mobility segment, which is seeing it’s fastest changes over the last 100 years. It is an industry which is never boring.
More Stories
What to Do After a Motorcycle Accident to Protect Yourself
Injured in a Motorcycle Crash? Talk to an Attorney Now
Danisense launches ‘Online Calibration Portal’ to offer brand agnostic calibration services for current transducers and smoothen the whole process