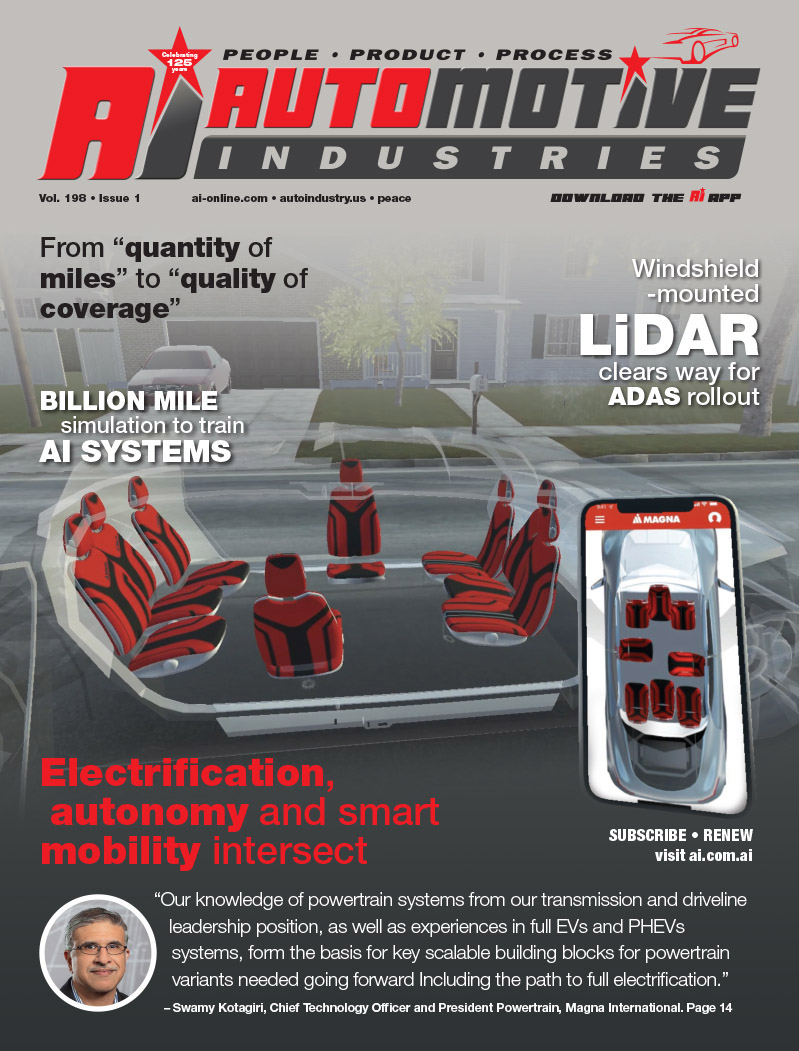
Magna Steyr is stuctured like an OEM without a brand.
Back in 1998, Magna International of Toronto acquired Steyr-Daimler-Puch, an Austrian automotive company established in 1934 after the merger of three different Austrian companies with roots in the nineteenth century.
![]() |
Magna Steyr builds 250 Jeep Grand Cherokees and Voyager minivans a day. The line is sequenced for one Jeep and two Voyagers. Components are delivered to the line in color-coded trolleys. |
The new Magna Steyr management started reorganization by selling all OEM activities such as the production of military off-road vehicles, agricultural tractors, marine engines, etc. and structuring the company as a dedicated partner to the automotive industry offering product and services.
Engineering services are provided by four engineering centers located in Graz and St. Valentin, Austria (commercial vehicle engineering 4X2, 4X4, 8X8, engine integration and application, driveline engineering and testing), Sailauf, Germany (ACTS-Advanced Car Technology Systems, safety and module engineering) and Detroit, Mich., U.S.A.
The largest engineering center is in Graz where 1,200 engineers are developing components, systems, modules and complete vehicles. This is a process oriented engineering organization with project management competencies up to complete vehicle manufacturing. The engineering team works in close cooperation with major OEMs on the development of derivative and niche model vehicles up to the point of setting up low-/extra-low-volume vehicle production lines (<5000 vehicle/year).
The close cooperation between development and production results in a continuous increase in know-how and experience which distinguishes Magna Steyr from mere engineering companies, ensuring the company a competitive edge.
![]() |
Workers on the Mercedes E Class 4Matic assembly line (above) install the fullyassembled engine with the Magna Steyr front axle module attached. Magna has been assembling the Mercedes G Class since 1979 and is still putting out 25 units daily. (below) |
![]() |
Just to give an idea of the expansion in car manufacturing in Graz, at the time of the Magna International takeover in 1998, annual production was in the range of 40,000 for various brands, in 2003 production surpassed the 120,000 mark and forecast for the present year is reaching 200,000 units, thus becoming the largest car manufacturer in the world without its own brand.
The newest assembly line in Graz is for the assembly of the BMW X3, a so called all-wheel driven “Sport Activity Vehicle” which started production in the last quarter of 2003.
Saab 93 Cabrio (convertible) was launched on the European market in mid-2003 and is now produced at a rate of 102 cars per day. The front part of the body is identical to the sedan. Everything rearward from the front door on the body has been developed and manufactured by Magna Steyr directly and reaches the assembly line from the painting shop.
All mechanical components are assembled on electrically-operated “marriage trains.” After 300 minutes from the start of the assembly process, the marriage train is placed under the body and the driveline connected to it. From that point on, the car moves along the line on its own wheels.
At the 450-minute station, some 25 independent electronic controls, up to that point neutral, are then programmed according to the legislation in force in the nation to which the car will be exported, and including the accessories and the owner chosen options.
At the end of the line the car is submitted to an 8-minute water test in a cell to ascertain the tightness of the hood and of the whole body. During the water test, the car receives an amount of water representing the yearly average- amount of rain of Middle-Europe.
Roughly after 1,200 minutes from the start of the assembly process, the Saab 93 convertible cars are on the truck starting for the distributor destination.
Wolfgang Vlasaty, central manager general assembly division, Saab, explained to us during the visit that convertible car sales are concentrated during the good season and that labor flexibility permitted by the Austrian law allow them to adjust production to market requests within ±17 percent of rated capacity.
![]() |
Magna Steyr can build up to 120 Saab 93 Cabrios a day, though production can be altered as sales slow during winter months. |
At the Graz plant, the automatic transmission is provided with an extra transfer case, the engine original oil sump (full of oil) is dismantled and replaced with a purposely shaped sump that leaves space for the Magna Steyr front axle module.
The PTO, with angle drives, is placed under the rear part of the engine block at the back of the new oil sump. A shaft parallel to the transmission- engine axis connects the transfer casing to the angle drive powering the front wheels.
In parallel with the growth in vehicle production, the company has grown in the manufacture of car components: mechanical parts, chassis modules, body parts up to complete bodies in white, complete cock pits, mirrors, etc. Magna Steyr has an unmatched experience in all wheel drive (AWD) systems which were pioneered by Steyr-Daimler-Puch in the mid 1950s and have become now a core business for the company handled by the subsidiary Magna Steyr Powertrain.
The company works in close cooperation with the OEM to develop innovative all-wheeldrive concepts and system integration into the OEM’s vehicle to reduce time to market and ensure a competitive price of the vehicle. Magna Steyr Powertrain operates four plants, one in Lannach where the headquarters and component production is located, 12 miles west of Graz, a second in Ilz, 26 miles east of Graz for the assembly of 4X4 components and systems as well as mass-balancing units.
For the American market, a component shop is based in Atlanta and a chassis module plant in Saltillo, Mexico. Magna Steyr Powertain has its own sales office in Detroit. The Lannach plant was inaugurated in 1999 and the production area, next to the office building, has a square shape with production plant managing offices in the middle, to be equally distant from all production departments working according to the Six-Sigma quality program. Due to the nice environment around the plant, personnel turnover is minimal and skilled workers account for over 70 percent of the working force.
The plant is equipped with seven automated aluminum die-casting cells for the production of transmission and differential housings, mass-balancing housing and housing covers.
More than 50 flexible machining centers, combined in cells, are used to machine the aluminum housings as well as numerous state of the art machinery for the production of gears, transmission and balancing shafts. They have automated feeding devices and are integrated with washing and leak test stations.
About 35,000 finished pieces are shipped each day from Lannach to the Ilz plant for assembly into powertrain components (transfer cases, angle drives, axle differentials, allwheel drive couplings) and successive assembly of chassis modules.
All powertrain components are submitted to functional and noise tests before shipment. Individual components are shipped directly to major OEMs: BMW, DaimlerChrysler, General Motors, Renault, Land Rover, Volkswagen, just to name a few.
More Stories
8 Best Plastic Welding Techniques for Automotive Manufacturing
5 Big Reasons to Choose LED Bulbs for Your Car Headlights
How much does it cost to ship a car on Amtrak Auto Train?