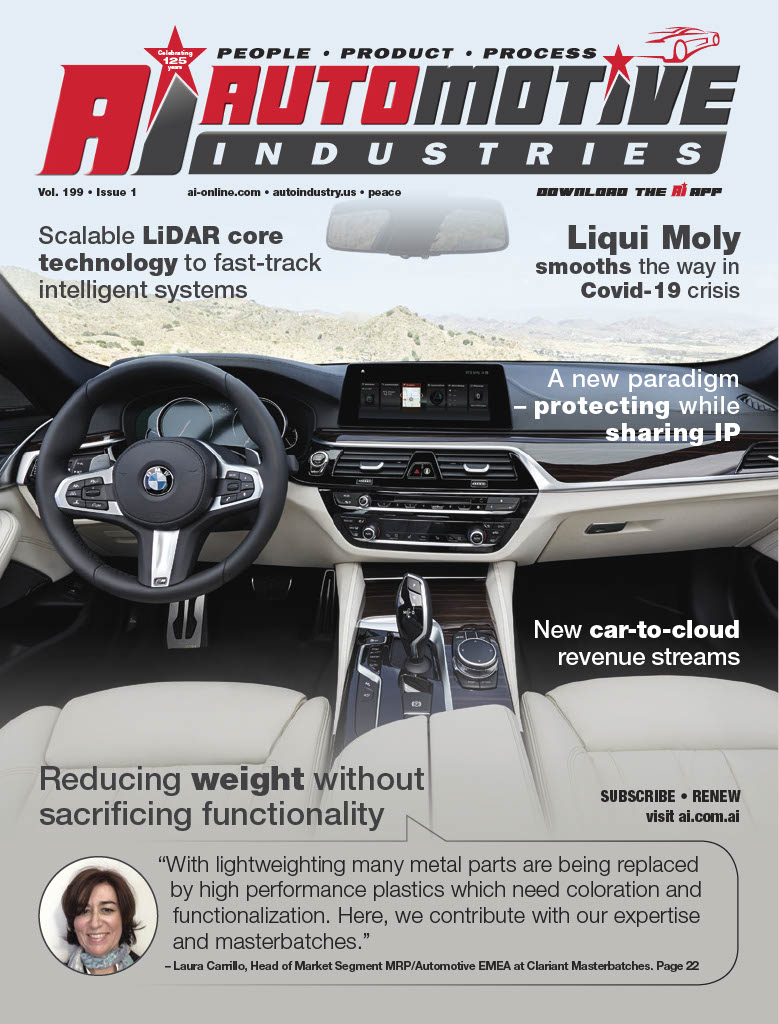
Chemical foaming agents (CFAs) are a well-known technology for density reduction in plastic applications. Advances in the formulation of the agents are expanding their use.
These advances were highlighted in a talk by Joachim Melzig of the BMW Group in a presentation at K 2019 titled “Injection molding of structural foam. A Clariant and BMW success story”. He detailed how BMW is using Clariant HYDROCEROL chemical foaming agents (CFAs) to reduce weight in the dashboards in almost all of their vehicles, including the 3 series and 5 series.
Automotive Industries (AI) asked Laura Carrillo, Head of Market Segment MRP/Automotive EMEA at Clariant Masterbatches how Hydrocerol® chemical foaming agents (CFAs) help reduce dashboard weight.
Carrillo: Added to plastics during processing, Hydrocerol® forms a cellular foam structure inside the plastic part, while the outer skin remains solid. Because the gas replaces some of the polymer, less plastic is needed to produce the final part. As BMW showed in our booth at K2019, the weight reduction achieved in their dashboard carriers is around 20%. Clariant CFAs are used in combination with core-back technology – a process that opens the mold slightly to reduce pressure and allow the foamed core to expand. Hydrocerol® has been specified in the drawings of several BMW vehicle models for a number of years.
AI: What mechanical properties can HYDROCEROL improve?
Carrillo: Hydrocerol® improves the stiffness-to-weight ratio when used with core-back expansion. Bending stiffness can be increased by making parts thicker, while they remain lighter. In contrast to the classic low-pressure process, with core-back technology the cavity is completely filled volumetrically and the cavity is enlarged, which leads to a drop in pressure and expansion of the gas-laden melt.
AI: Is it suitable for large parts?
Carrillo: We have reduced the weight reduction of big parts like lift gates in the vehicle trunk. Other benefits provided by foaming are sink mark reduction, easier mold filling and warpage reduction. Sink marks and voids are caused by localized shrinkage of the material in thick section parts. Plastic molded parts contract as they cool. In large parts this results in localized shrinkage as thicker part sections cool more slowly than the thinner sections. Hydrocerol® eliminates sink marks due to gas expansion and the cell structure avoids the formation of voids. It improves the flowability of polymers as well. The generated CO2 gas acts like a lubricant.
Warpage is caused by material stresses during injection molding process which results in distortion of the finished part. Hydrocerol® leads to a uniform cavity pressure and reduces material stresses caused during filling and holding pressure.
AI: What are the processing advantages of HYDROCEROL?
Carrillo: Our customers report productivity improvement through cycle time reduction of up to 20%. This is a result of optimized mold filling and the replacement of holding pressure by gas expansion and gas cell growth. With Hydrocerol® the holding pressure phase can be reduced or even eliminated. It also contributes to overall energy savings because it allows the molders to reduce the clamping force.
In automotive applications, polymers containing mineral fillers are often used to improve mechanical performance. Hydrocerol® can be processed with long glass fibers without reducing their length – something that is not possible with other technologies such as physical foaming. In addition, Hydrocerol® does not require large capital investment. It is a plug-and-play technology, which can be used in existing machinery by adding 1-2% Hydrocerol® granules to the processing polymer.
AI: How does HYDROCEROL contribute to Clariant’s program to support a more sustainable plastics industry?
Carrillo: Global megatrends such as climate change, energy, demographic changes and resource scarcity led Clariant to launch the “Portfolio Value Program” (PVP) in 2013. We understand sustainability across three main pillars: People, Performance and Planet. The Portfolio Value Program consists of the systematic evaluation of our full product portfolio according to 36 criteria in the areas of environment, society and economy. These criteria include topics like raw material safety, energy spent during production and also sustainability over the entire lifecycle of the products. The sustainability performance of a product and the relative sustainability in comparison with its competitors are assessed. Hydrocerol® is one of the product ranges that is awarded Clariant’s internal ECOTAIN® label, which reflects best-in-class performance in terms of sustainability.
It is important to mention that chemical foaming agents included in Hydrocerol® are non- hazardous. We do not recommend mixing Hydrocerol® with exothermic foaming agents based on hazardous chemistry and which generate unpleasant amine odors. We are working to replace exothermic foaming agents like Azodicarbonamide (AZDC) in certain applications.
AI: How closely do you work with automakers and tiers?
Carrillo: We run projects together with resin producers, OEMs and Tier 1 and 2 suppliers. Normally all the partners need to be involved to make the project succeed. The majority of resin producers are developing new grades suitable for foaming. During trials we provide support to ensure the maximum weight reduction and balanced mechanical properties are achieved in the part. Our added value is to connect the different stakeholders and make sure everybody perceives and achieves the benefits of this technology.
With lightweighting many metal parts are being replaced by high performance plastics which need coloration and functionalization. Here, we contribute with our expertise and masterbatches. We can improve properties like UV resistance, antistatic behavior or flame retardancy.
AI: How do you see the transition to a circular plastics economy?
Carrillo: All partners in the plastics value chain need to work together to meet the challenges of the circular economy. Plastics are a very valuable and versatile material which need to be used rationally, but at the same time companies need to invest in new technologies and materials to provide solutions for a less polluted world.
Clariant has invested in an innovation center for plastics recycling called CycleWorks. It is a small pilot plant for Post-Consumer Recycling materials (PCRs). This will be our platform to get a better understanding on how our products can contribute to circular economy and market needs, and to develop innovative solutions for the plastic recycling value chain.
We are mainly driven here by the packaging industry, which is under higher pressure than the automotive sector to recycle. We are also working on a PCR color prediction tool to support our customers with their color choices when using recycled materials. This tool is currently being used for packaging applications, but we are studying its applicability to industries like automotive as well.
What’s next for Clariant?
Carrillo: With regards to foaming, we see two directions. One is the use of Hydrocerol® for thin wall injection molding on airduct systems and partial core-back foaming of thinner parts. Another is the foaming of visible parts, like door panels. Aesthetics are then an important consideration. We expect Hydrocerol® to be in series very soon with not only structural, but also visible parts in the car interior.
Regarding other trends like electric vehicles and autonomous cars, we see the car interior as the main focus in terms of design and new requirements with regards to durability, comfort, hygiene and safety. Aligned with these overarching trends, we have recently launched our CESA®-scratch portfolio for PP parts, that improves scratch resistance and durability of interior parts. Our new portfolio of scratch resistance additives is siloxane-free, which will potentially be declared a SVHC (Substances of Very High Concern).
Another work stream is odor management. Odor and VOC reduction in the passenger cabin are a big concern for car makers and we are confident that we have a good solution which will soon be available commercially. We expect to launch a new odor scavenger for polypropylene within the next year.
More Stories
Automotive Industries (AI) Newsletter April 2025
Bangkok International Motor Show 2025 – The Talk of Sensuous Automotive
Dürr Systems on paint supply: The foundation for high coating quality