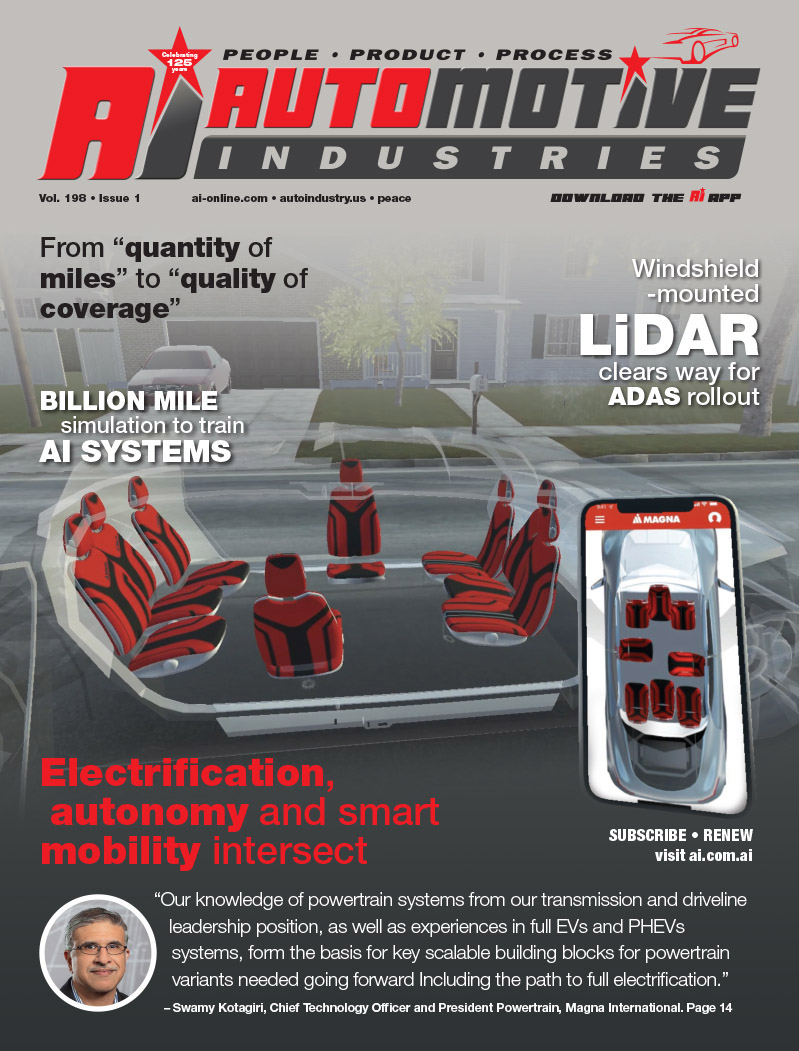
The drivers for flexible manufacturing in the supply base may not be what you think.
Flexible manufacturing is largely ignored by high-volume processoriented manufacturers in the auto industry, despite all of the talk about flexible manufacturing by vehicle manufacturers. It is often ignored because flexible manufacturing is misconstrued to mean one-piece manufacturing. And, because process-oriented manufacturers correctly recognize that vehicle manufacturers adopting flexible manufacturing will not necessarily need part suppliers to do the same. But standardization of modules and component sets will accelerate sourcing from low manufacturing cost regions, leaving behind products for domestic manufacturers to compete that involve local customization of a global vehicle or products subject to frequently changing customer preferences. This will drive a need for more flexibility in the manufacturing supply chain.
Flexible manufacturing does not mean one-piece manufacturing
North American vehicle manufacturers have been pursuing and promoting the ability to produce a variable mix of models with the same body shop and assembly line, for example switching between a sedan and an SUV on the fly. Vehicle manufacturers want to avoid repeating DaimlerChrysler’s situation when they could not produce enough PT Cruisers in Mexico to meet demand, despite having another plant in Belvedere, Illinois, building the Neon on which the PT Cruiser was based. Instead, vehicle manufacturers want to emulate Toyota, which can produce multiple models and styles from the same plant, or move models to different plants around the world with its Global Body Line (GBL) manufacturing system. Although the flexible manufacturing systems of OEMs such as Toyota, Nissan and Ford may enable them to manufacture different models one at a time, the driver is to better utilize their capital to meet changing market demands.
Many suppliers with high-volume manufacturing processes, such as metal stamping or plastic molding, dismiss “flexible manufacturing” as something irrelevant to their business. They typically view flexible manufacturing as something only relevant to machining companies with CNC milling centers, or sequenced assembly companies, who can change the process from one part to the next. To be certain, changing plastic injection molds or progressive stamping dies from one part to the next is impractical and full of waste. However, the need to get the most out of manufacturing capital under fluctuating market demand is still very relevant. Achieving flexibility in manufacturing operations will become more important with today’s industry trends.
Fluctuating Releases
Obviously, as vehicle manufacturers incorporate more flexibility in their assembly plants, it will enable more variability in the production mix, which will drive more variability in component releases. This trend alone is unlikely to drive flexible manufacturing into high-volume manufacturers. The product mix produced may vary significantly from planning volumes, but steady-state week-to-week production will likely stabilize as the market preferences become known. Batch production will continue at high-volume suppliers, with inventory management absorbing any fluctuation in release schedules from one week to the next.
Globalization of Modules Meets Niche Nameplates
One trend that will drive flexibility deeper in North American manufacturing is the combination of module globalization and niche nameplates, more so than flexible OEM assembly plants. Clearly, vehicle manufacturers have attempted to gain economies of scale in development and manufacturing through global platforms. However, the ideal “one world, one car” dream has proven to have its limitations, in that each continent has different tastes and regulations. Therefore, the focus has shifted from globalizing platforms to globalizing the major modules and component sets of the vehicle, such as the strategy announced and pursued by VW. Global modules of items such as brakes, radiators, transmissions or even portions of the body can be used across vehicle nameplates and platforms in multiple markets, thereby reaching volumes of millions and providing great economies of scale. With global applications, these standardized modules and component sets may be produced in multiple regions or the one region that offers the lowest cost. Meanwhile, the vehicle itself may be engineered around these modules to meet the wants of the local consumers or even a subset of consumers. Vehicle manufacturers are seeking to capture profit opportunity through niche vehicles with high appeal to smaller segments of the market.
The 2004 Toyota Solara may be an example of such a vehicle. With an anticipated peak annual volume of 50,000 units, it is not a highvolume vehicle. It was engineered in the U.S. for the North American market to appeal to sport specialty buyers. Yet, within the vehicle are components shared with the very high volume Toyota Camry. Some of the Camry components are produced domestically, while others are produced in other regions for global consumption.
As select modules and components reach very high volumes through standardization across multiple regions, it becomes much more attractive to produce the very high volume in regions with lower manufacturing costs.
However, those components that are particularly region specific, low volume, or sensitive to consumer fashions such as interior trim colors, do not warrant the added inventory and logistic challenges of overseas production. On vehicles where the design center of excellence for an OEM is outside of the U.S., this will likely limit opportunities for domestic manufacturers to lower volume components unless they can offer the lowest global price. Surviving with three to five times the quantity of part numbers to achieve the same sales volume will drive the need to adopt more flexible manufacturing techniques and tools among batch processing stampers and molders.
Attacking the Numerator or Denominator in Capital Utilization
Once again, the objective of flexible manufacturing is to better utilize capital under more frequently changing market demands. One approach is to get greater productivity out of the capital that’s employed. This may mean shorter downtime due to changeover, or increasing production rates. Or, better capital utilization may be achieved through reducing the capital spent per program. Flexible manufacturing will likely spark more creativity in tooling for high-volume processes. For example, several parts and service parts may be manufactured with essentially the same die or mold, with some replacement or adjustment of select die or mold components. This would lower the investment for the program to just the tool steels that are different. Other investment reductions may be through reconfigurable floor space, or investing adjustability into secondary processes, such as welders or assembly fixtures. Standardization in product and process design may also be used to a greater extent to reduce the number of variables in production. An example may include reducing the number of metal coil widths and thicknesses a plant handles, which impacts the stamping die design and strip layout.
Reducing program investment is aligned with the customers’ anticipated expectations. Customers will want to pay significantly less for a tool on a 50,000 unit program than a 200,000 unit program, even though the part and therefore the die or mold is identical.
Looking Ahead for Yourself
Orders being filled today are the product of OEM thinking four to seven years ago. Since then, the industry has become much more global. More products are subject to global modularization. More nameplates are being generated from fewer platforms, which cross continents. More companies have experience manufacturing in or sourcing from other continents. Thinking through today’s trends will provide clues to industry sourcing three to seven years from now. With global pressures shrinking margins, the higher return on investment will go to the manufacturer with the flexibility to better utilize financial and intellectual capital under changing market demands.
Applicable Flexible Manufacturing Techniques to High-Volume Processes
•Re-use of equipment
•Reconfigurable or re-useable tooling
•Standardization of manufacturing process elements,
e.g., packaging, set-ups, raw materials, locating points
• Standardization of product design hard-points
• Reconfigurable floor space and/or working areas
Jason C. Brewer is a manager in the Automotive Supplier Consulting Services Practice of Plante & Moran, PLLC in Southfield, Michigan. Jason.Brewer@plantemoran. com.
More Stories
8 Best Plastic Welding Techniques for Automotive Manufacturing
5 Big Reasons to Choose LED Bulbs for Your Car Headlights
How much does it cost to ship a car on Amtrak Auto Train?