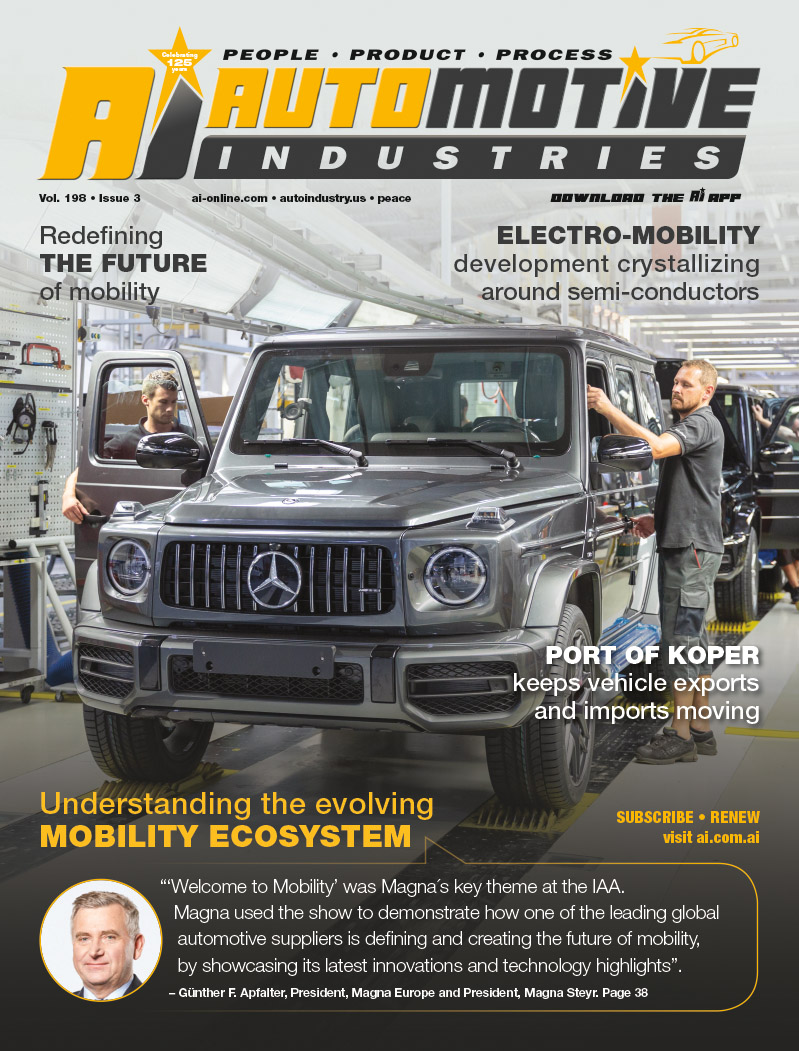
Plastics making vehicles lighter, quieter
Plastics are helping vehicle designers to reduce emissions while improving driver and passenger comfort.
Underbodies from Mannheim, Germany-based Röchling Automotive help reduce road noise in the new Mercedes S Class. Röchling technology is also found in the new C class in the form of wheel arch liners. BMW has commissioned Röchling Automotive for several system developments for the purpose of further reducing exhaust and noise emissions, including the development of SCR systems. For its Chinese production, BMW is using Röchling wheel arch liners, injection-molded parts for the underbody area and a front wall package.
Röchling also delivers degas bottles for the premium all-terrain vehicles. Nissan makes use of controllable air duct systems. Mazda also rides with Röchling: In June 2013, production of air flap control systems for the “Axela” and “Atenza” models was launched in Japan. Production takes place at “Starlite,” Röchling Automotive’s Japanese partner firm.
Toyota has selected Röchling as the future supplier of charge-air tubes, which are already being used in several models. Röchling is also demonstrating its lightweight expertise for the Italian truck manufacturer Iveco. Thanks to Röchling technology, 30,000 “Iveco Stralis” trucks are benefiting from weight savings of 250% (Ed: correction 25%) by using plastic covers. Plastic has replaced aluminum in a new “blow-by” cover. Chang’an Ford, a joint venture of the American and Chinese automobile manufacturers Ford and Changan is using air flaps, deflectors and windshield cowls produced by Röchling Automotive at the Chengdu, China site.
Automotive Industries (AI) asked Erwin Doll, Chief Executive Officer Röchling Automotive, what he considers to be the breakthroughs in plastics technology over the past few years.
Doll: Innovations to optimize airflow have contributed enormously to eco-friendly driving. Let me just name the active grille shutter systems that have pioneered active aerodynamics and contributed to a more effective thermal management. Secondly, the optimization of the underbody by the use of low weight reinforced thermoplastic engine and body under shields, which have added efficiency and driving comfort to the vehicle. And last, but not least, the new solutions for air intake systems such as the integration of a water cooled charge-air coolers into the air intake manifold, the generation of customer specific sounds, and the reduction of weight have demonstrated the potential of combining expertise in airflow, acoustics and thermal management.
AI: How is this innovation supporting OEMs?
Doll: Measuring the results by comparing them to existing benchmarks is no longer the only way to prove efficiency. For example, the prediction of filter lifetime using software enables the carmaker to drastically reduce the number of air filter variants. It’s also worth knowing that an active grille shutter being part of a thermoacoustic engine encapsulation can double the advantageous effects on fuel consumption and acoustics. A broad family of lightweight materials in combination with modern, state of the art manufacturing technologies helps the OEM to find the optimum solution that fulfills all specifications and expectations, but achieves even more weight reduction, even better thermoacoustic insulation or even higher mechanical stiffness than offered by someone else. This is the kind of added value that really delights the customer.
AI: How “green” are plastic parts?
Doll: Plastics are sustainable, but their functionality inside of a system makes them even greener. Their biggest potential is weight reduction by integration, as well as incorporating new and better functions into a system. For example, we have received a large number of orders for our robust and lightweight SCR tank system solutions. Röchling Automotive has received the SPE-Award 2013 of the American Society of Plastics Engineers for economical lightweight construction of flexible charge air lines. Stratura, where we combine inner floor, body and underbody panel in one part is a new approach. Plantura parts, based on special grades of polylactic acid with fillers, are ready to replace polypropylene if the carmaker is going for an optimized carbon footprint.
AI: What is the driving force behind the expansion of Röchling’s global footprint?
Doll: Generally, we would like to grow on all markets. With eight new production plants built in the last three years we follow our concept to serve our customers globally with products lowering fuel consumption and emissions. North America, in particular, is one of the regions where the reduction of emissions is very important and thus Röchling Automotive sees growth opportunities.
AI: Please tell us about Röchling’s commitment to skills development.
Doll: We are continuously learning to understand and use the cultural differences among different people around the world for our ongoing growth. We are developing our competences in electronics and thermal management as we are convinced of the innovation potential coming from having knowledge in these areas. And we are looking for multilingual engineers with a special spirit of innovation.
AI: Where next for Röchling’s automotive technology?
Doll: The optimization of the underbody is an interesting field of innovation, both for cars and trucks – especially with regard to aerodynamics, weight saving and the integration of new components. We are able to provide our customers with solutions for battery stacks and housings, as well as various fuel cell components. Röchling Automotive has developed active grille shutters for pure electric and hybrid cars. Better thermal management will lead to new solutions at the front of the car and the engine compartment. Acoustics will also remain important. Products developed for the upper segment will find their way into the cheaper cars. In addition to all this new technology, OEMs want to save time and money. Delivering components at high speed at high quality is achieved by having a very high level of simulation and calculation expertise in all areas of our business.
AI: Some blue sky thinking – will we ever have an all plastic car?
Doll: I believe the multi material approach is the best way to produce good and affordable cars for the mainstream. I’m convinced that technical solutions using polymers will continue to expand their market share. In some niche markets, plastic parts have the potential to reach and exceed 30% share of the weight of a car.
More Stories
Automotive Industries (AI) Newsletter April 2025
How to Create the Ultimate Off-Road Vehicle Garage: A Practical Guide
Bangkok International Motor Show 2025 – The Talk of Sensuous Automotive