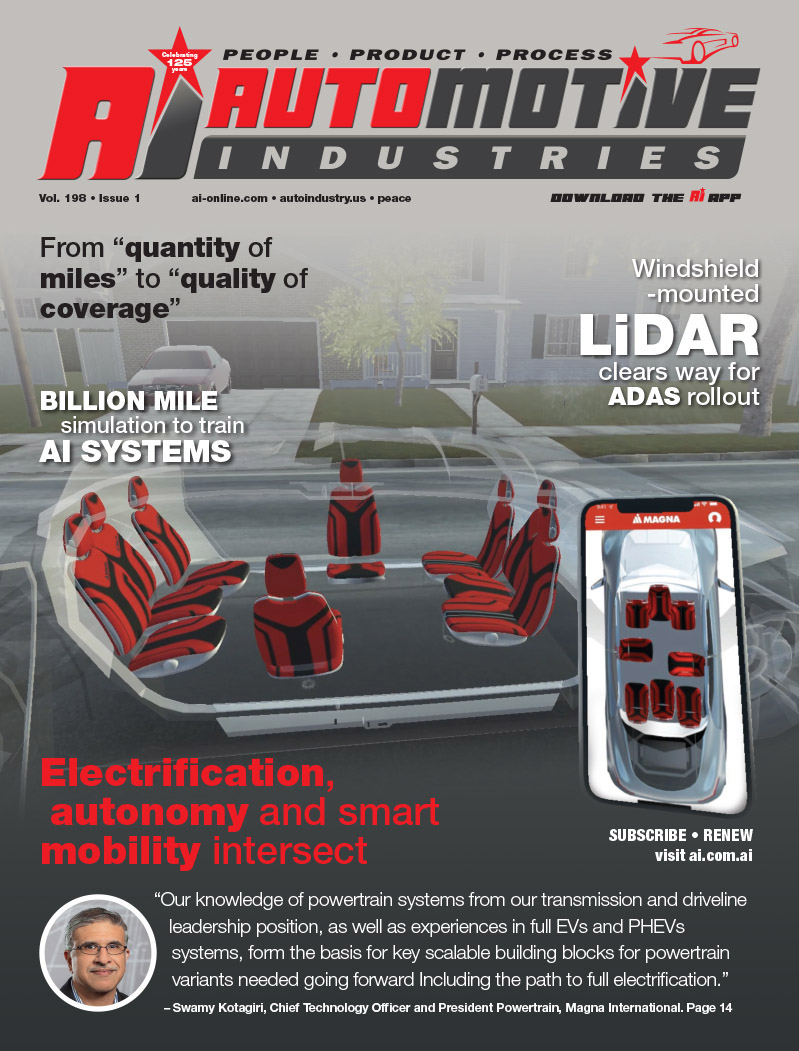
The Energimyndigheten or Swedish Energy Agency predicts that nearly 100,000 electric and plug-in hybrids will be running on Sweden’s roads by 2020. Through the Swedish Hybrid Vehicle Centre (SHC), solutions to the high cost of vehicle batteries are being developed.
The SHC was set up by the Swedish Energy Agency in partnership with three Swedish universities (Chalmers University of Technology which is the host university, Royal Institute of Technology and the Lund Institute of Technology) and six Swedish companies including AB Volvo, Volvo Car Corporation, Saab Automobile, GM Powertrain Sweden, Scania CV and BAE Systems Hägglunds.
The SHC, through a team of 40 researchers, is currently running 15 research projects addressing the energy management of hybrid vehicles, diagnosis of hybrid systems, vehicles with autonomous wheels, and the development of electric motors operating with integrated charging. The Centre has also begun research into drivelines based on an electric motor combined with a small additional energy source, and is studying the demand for power in auxiliary systems in hybrid vehicles.
A major challenge regarding hybrid-electric and electric vehicles is the development of energy storage with sufficient capacity, thus giving a vehicle a sufficiently large operating range.
“Lithium-based batteries are seen as the next generation of batteries for hybrid vehicles and electric vehicles. At SHC, we are running projects focusing on the battery cell, trying to find material combinations that will improve the energy output and also the safety,” said Lennart Josefson, director of the Swedish Hybrid Vehicle Centre in an earlier interview with AI. “We have also started projects dealing with the performance of battery systems. There are two challenges hybrid vehicles and electric vehicles face. Firstly, the safety of the energy storage must sustain normal operations and impact loads. Secondly, there is a demand for lower vehicle weights (to accommodate batteries) and thus, new active and passive solutions will be necessary.”
Volvo’s V60 Plug-in Hybrid was unveiled at 2011’s Geneva Motor Show, and will be commercially launched in 2012. It is a diesel hybrid vehicle incorporating critical inputs from the SHC. It has a 5-cylinder turbo diesel driving the front wheels, and a 70 hp electric motor at the rear axle. The electric motor receives power from a 12 kWh Li-ion battery pack. The vehicle can be run as an electric vehicle (with ac range of 50 km) and as a hybrid combining the ICE and electric motor.
In January 2011, during the North American International Auto Show held in Detroit, Volvo president and CEO, Stefan Jacoby unveiled a crash-tested C30 electric incorporating Ener1’s EnerDel battery. The car on display was tested at Volvo’s crash test laboratory in Sweden. A fully charged EnerDel Li-ion battery was subjected to a 40 mph offset frontal collision with a barrier. The test produced the results expected by the company’s engineers. The front deformed and distributed the energy from the crash. Both the batteries and the cables, which are part of the electric system, remained intact after the collision.
“Our tests show that it is vital to separate the batteries from the electric vehicle’s crumple zones to make it as safe as a conventional car. We are the first vehicle maker to show the world what a truly safe electric car looks like after a collision with high-speed impact,” said Jacoby at a press conference.
Automotive Industries spoke to Lennart Josefson, director of the Swedish Hybrid Vehicle Centre (SHC) and asked him about the new technology that will allow parts of a car body to double up as its battery.
Josefson: The StorAGE project is headed up by Imperial College in London. The material used in the new technology is a carbon composite consisting of woven sheets of carbon fibers which are made rigid using a cured resin. To enable this material to store electric energy, two layers of woven fibers are made into a sandwich, separated by a thin layer of an insulating material. The resin within the carbon layers is laced with Lithium ions, so that each layer acts like an electrode. The composite behaves more like a super-capacitor than a battery. It currently has an energy density of 0.005 Wh/kg which is expected to increase within the project to some 20 Wh/kg. The potential to use this material in cars is large, with the battery (or super-capacitor) being load carrying.
AI: What are some of the breakthroughs in battery technology that you see revolutionizing the vehicle manufacturing industry?
Josefson: We foresee no immediate breakthrough when it comes to Li-ion based battery technology. The available energy density is restricted by chemical principles, and only minor improvements are to be expected in the near future. The development of reliable battery systems with low manufacturing costs is a challenge. There is, however, a strong push towards the development of continuous, inductive and conductive charging of electric vehicles. This is an alternative means of reducing the need for large amounts of energy stored in the vehicle.
AI: Where do you think the SHC’s research has been particularly successful – in its work with energy storage or other areas like systems and electrical drives and machines?
Josefson: So far, the development of integrated charging of plug-in hybrids is one of the most successful contributions from SHC, in combination with an increased understanding of the control of hybrid vehicles.
AI: Tell us about the SHC’s contribution to Volvo’s V60 plug-in hybrid project?
Josefson: Volvo, together with Vattenfall, demonstrated the development and manufacturing of a plug-in hybrid. SHC will use the results from this project for its battery system models.
AI: What are the safety issues that need to be tackled when it comes to developing hybrid and electric vehicles?
Josefson: The impact safety of hybrid and electric vehicles must be guaranteed. There are also issues when it comes to the reliability of the battery system in ordinary use. Safety in handling high voltage components during manufacturing, in operation, and in case of accidents must also be assured.
AI: What progress needs to made as far as vehicle weight is concerned for electric vehicles?
Josefson: It is necessary to reduce the weight of the electric vehicle in order to increase the driving range as well as the cost of the energy storage.
More Stories
Automotive Industries (AI) Newsletter April 2025
GlobalLogic Pioneering Software-Defined Vehicles, AI Innovation, and Sustainable Solutions for the Future of Automotive Mobility
Cybord TCI – The Future of Manufacturing Integrity