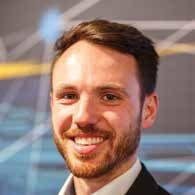
Series production of metal components using 3D printing technology has been described as evidence of a digital industrial revolution that is transforming the $12 trillion manufacturing industry.
Automotive Industries (AI) asked Martin Friedrich, Project leader Pre-development Additive Manufacturing Center Non-metals, how additive manufacturing (AM) has matured since BMW started using it in 1990.
Friedrich: This early adoption of AM using stereolithography has helped us gain an enormous knowledge in applying 3D printing. Today we use additive manufacturing in areas such as spare parts for classic vehicles, tools for assembly lines and parts for series production of our cars. Most recently we matured AM technologies to produce series parts for the BMW i8 Roadster such as the fixture in the tonneau cover for the soft-top. It is made of aluminum alloy and the printed item is lighter than the plastic injection-molded equivalent. It is also significantly more rigid. With this part we became the first carmaker to 3D-print a production run of several thousand metal parts. The window guide rail is manufactured by HP Multi Jet Fusion Technology, a relatively new, high-speed method now approved for series production of vehicles. A window guide rail became the one-millionth AM part produced by the BMW Group. Also, our Mini fans are been able to customize indicator inlays known as side scuttles and trims for the passenger side in the interior. Meanwhile we handle nearly 30,000 internal prototype orders and deliver more than 200,000 components annually. Looking to the future we have invested more than 10 million Euros in the building of an AM Campus. We have invested in AM unicorns such as Carbon and Desktop Metal via our BMW i Ventures Team.
AI: Are there different design criteria for AM components?
Friedrich: When producing parts for series production one of the most important criteria is to design parts with reproducible properties in the most efficient way. AM technologies provide many opportunities when it comes to improving the part’s performance and reducing costs without additional effort. Another determining factor is the production method you want to apply later on. The soft-top fixture for the BMW i8 Roadster was not only optimized for mechanical performance, but can also be built without almost any support material. This is pretty unique and requires new ways of design thinking and a completely new approach to engineering. We also use the technology to optimize parts that will later be produced by conventional production methods such as injection molding. We can use internal lattice structures in parts, print them with elastomeric materials and simulate the behavior of conventional foams. We do this for prototype seats in concept cars or bikes and dashboards to mimic the assembly process.
AI: Which components do you feel lend themselves best to AM?
Friedrich: AM has become essential in vehicle development and production of prototypes. In series production, small complex but also individualized parts are door-openers for AM. There are also bionic structures – geometries that are inspired by forms found in nature such as the BMW i8 Roadsters fixture of the softtop and parts with added function such as internal structures (e.g. for cooling). I believe that this is still just the beginning. Currently, costs are a limiting factor in AM due to high raw material costs and a relatively slow production speed compared to tool-based techniques. In addition, we still see lots of manual effort and tasks along the process chain which add to the cost. We believe cost effectiveness will improve through new production processes which are in development at the moment. We think the most important task in the automotive industry will then be to integrate AM technologies in fully automated production lines.
AI: HP has introduced metal jet platform. Has metal powder AM caught up with plastics?
Friedrich: Using the HP Jet Fusion Technology is something very special for us as we have been involved in the early development of the first systems and thus gained a lot of experience with this technology in the beta test phase – before anybody else had access to this method. This kind of collaboration is one of the most important and exciting aspects of my job. Just as with plastics, metal 3D printing is an established technology from prototyping up to serial production. The main production process used at the BMW Group today is laser powder bed fusion. The technology is a decade younger than most plastics processes, but is on a steep incline in application. The main field of application today is prototyping. Our internal customers use 3D printed parts as a tool-free substitutes for series design. The parts can be produced in comparable material to conventional parts such as cast components. This allows designers to conduct fully functional tests without the need to go into expensive and time-consuming tooling. In series production we can utilize the lightweight potential that AM provides. By saving weight we reduce production costs. We see massive productivity gains over the next few years, which will decrease production costs and lead to a broader application range in prototyping as well as in series production. One example of a new production process is binder jetting where a raw part is being printed in a powder bed and then sintered in a furnace. The process adds a lot of speed in the raw part production. We are evaluating the geometric flexibility and the material properties of every process to identify the optimal application for our products.
AI: How important is software?
Friedrich: Software in future will be like using a tool, technology or a material. Your choice will very much depend on the application. What will be important is that the software tools used to design parts can also be used through other development stages. This means that machines also need to start communicating in a standardized way via protocols, like OPC-UA. Only then will we be able us to fully integrate AM technologies into existing production lines and exploit the potential for automation and predictive maintenance.
AI: Can the speed of AM manufacturing compete with traditional processes?
Friedrich: There are some examples in which AM technologies can provide a batch of parts in a really short timeframe. However, AM is not yet on the level of traditional processes. We see that AM technologies are getting faster and faster, but the real benefits are not only characterized by faster cycle times. You don’t need to consider tool design and production times to get first parts or short runs.
AI: Where will we see the first series production of highvolume components using AM?
Friedrich: We have a group of design and automotive experts in the BMW Group that is working closely together with our Additive Manufacturing Center to evaluate each part that could have the potential to be 3D printed. We are also trying to find new manufacturing technologies and collaborate with software, machine and material suppliers to increase the usability and economics of AM. This is why we entered into strategic partnerships and investments on the polymer and metal sides. Affordable materials combined with fast, flexible and reliable production systems will drive the change. Therefore, new process chains have to be set up for producing high quality components in large volumes. From our point of view, it is just a matter of time when cost effective additive manufacturing machinery for large series production will become available and raw material prices will reach an acceptable level.
More Stories
Automotive Industries (AI) Newsletter April 2025
GlobalLogic Pioneering Software-Defined Vehicles, AI Innovation, and Sustainable Solutions for the Future of Automotive Mobility
Cybord TCI – The Future of Manufacturing Integrity