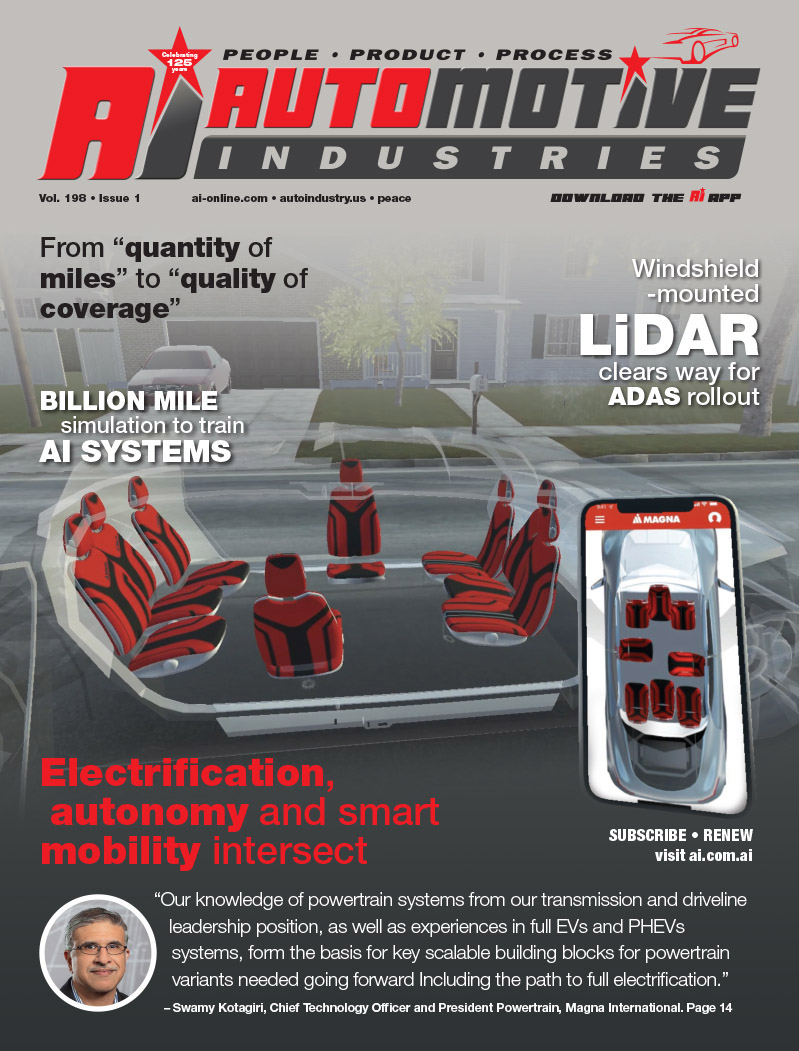
Dana Corp. supplies innovative axle technologies to Nissan’s big trucks.
![]() |
The Dana Model 205 independent front axle was designed to meet Nissan’s stringent standards. The unit features the first use of a cast-aluminum carrier and integrated tube on a component of this size. |
Nissan turned to Dana Corp. a supplier to Nissan’s Frontier pickup and Xterra SUV, to provide technological innovations for the driveline of the Nissan Titan pickup and Pathfinder Armada SUV.
The Dana Model 205 independent front axle features the industry’s first-use of a onepiece aluminum independent front axle (IFA) carrier with an integrated tube and patented oil flow design.
“This is something that hasn’t been done on a truck before,” says Frank Metelues, design engineer for Dana’s Automotive Systems Group, referring to the manufacturing of an integrated tube into the axle body by die cast process. Metelues says that the technology not only pushes the design and technology envelope, but also involves some innovative manufacturing technology to incorporate that kind of change.
Metelues says that packaging was the driver to go with an integrated tube design. Dana says that laboratory tests have confirmed a significant improvement in strength over traditional axle designs of this size, and the use of aluminum over cast iron resulted in a weight savings of 35 pounds. Dana has also patented an advanced oil flow baffle design that ensures constant lubrication to the ring gear, pinion and pinion bearing even at grades of +/- 35 degrees.
“That was one of the challenges,” says Metelues. “They wanted our axle to perform under severe angles at low speeds.” NVH was reduced by increasing the number of teeth on both the front and rear axle ring gear and pinion sets, allowing for smoother gear operation. Nissan worked with Dana on the sealing of the pinion and the cover plate. “It was kind of a joint venture,” says Metelues, “trying to optimize both design and materials.”
A decision was made to use a derivative of a Dupont-trademarked elastomer called Viton, for the pinion seal. This is the first use of this material, normally used for engine sealing, in a differential. The new design improves wear and provides constant contact with the axle slinger, even under vacuum conditions, eliminating virtually all possibility of the introduction of contaminants. The seals can withstand temperatures ranging from -40 to +400 degrees Fahrenheit. Metelues says the extra robustness was designed into the component to meet Nissan’s rigorous 250,000-mile durability test. “Normally these applications are designed to last about 100,000 miles,” Metelues says. “Nissan wanted to go beyond that.”
Dana also worked with Tochiji-Fujii to provide an optional electronic locking differential to the rear axle assembly, to enhance traction in off-road conditions.
The axles will be manufactured at Dana’s Columbia, Mo. facility and delivered on-time to Nissan’s Canton, Miss., assembly plant. Dana also is working with Nissan on a plan to sequence the driveshaft and both axles into the plant on an as-needed basis.
More Stories
RAM Trucks in Toronto: Why CarHub North York Chrysler Delivers the Best Experience
Buying Car Insurance in Toronto? Don’t Make These Rookie Mistakes
Extend Your Range, Maximize Your Storage with FRDM’s 45 Gallon Combo