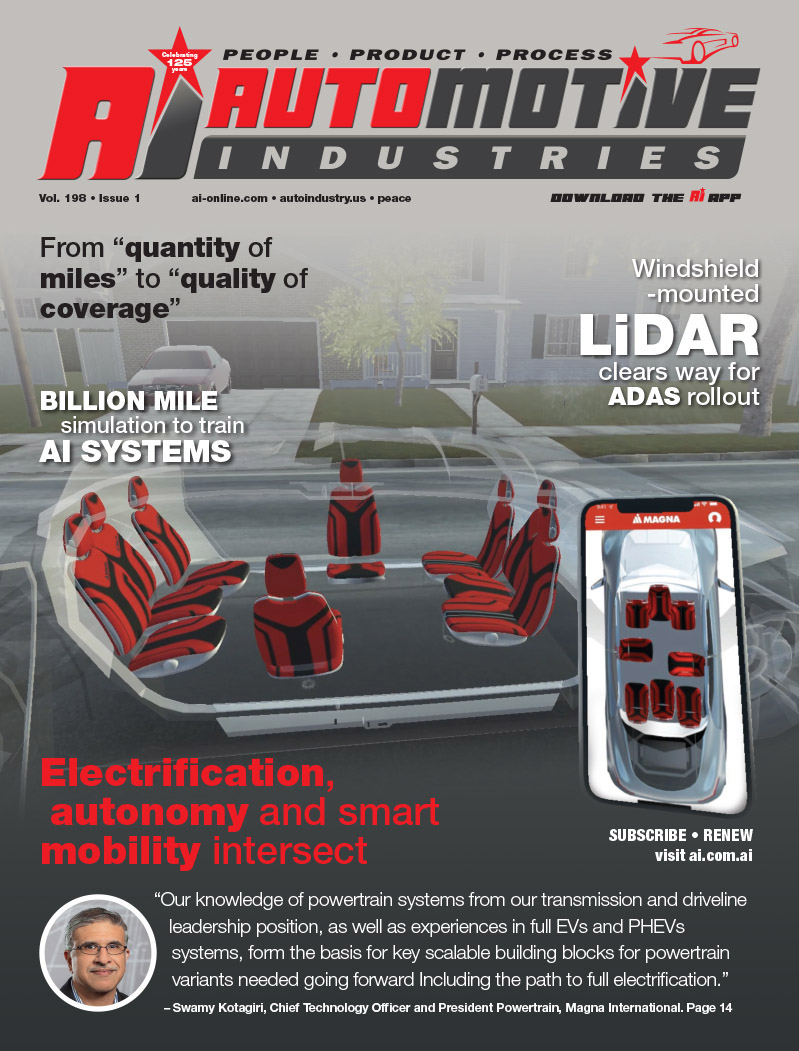
Fastener thread form designed to withstand diesel stresses.
A special internal thread form developed by Spiralock Corp. is being used by diesel engine and vehicle manufacturers to help accommodate the extreme temperature and vibration of enginepowered equipment, while minimizing thread loosening, assembly and service costs.
![]() |
A special internal thread form developed by Spiralock Corp. is being used by diesel engine and vehicle manufacturers and can be used in a range of fastener configurations. |
Traditional methods of preventing joint loosening, such as nylon rings, adhesives and deformed threads, often can’t accommodate the high temperature, high vibration diesel engine environment.
“At high engine operating temperatures, nylon-coated fasteners will melt or burn, and adhesives aren’t effective either,” adds Sam Sutthiwan, a designer for Peoria, Ill.-based Caterpillar. “Split washers and standard thread-type fasteners tend to yield over repeated cycles of heating and cooling and require lock tabs to prevent them from losing their fastening ability. Prevailing torque fasteners can present assembly and service challenges, especially with stainless steel.”
Threaded fasteners can face limitations in diesel truck engine applications, particularly those with high performance turbo requirements, as they can be susceptible to shock, vibration, loading, as well as thermal expansion and contraction.
![]() |
A schematic showing how the 30 degree wedge ramp female thread securely connects the standard male thread forms. |
Friction-induced thread galling, or fusing, can also create assembly and service problems when high-resistance prevailing torque nuts are used with high-speed assembly equipment and stainless-steel fasteners. Due to galling, prevailing torque nuts may “freeze” before fully tightened during assembly, leading to exhaust leakage, gasket failure, reduced engine performance and a reduction in fuel economy.
Through the geometry and physics of the thread itself, Madison Heights, Mich.-based Spiralock developed its alternative thread form designed to address fastener loosening and stripping under high temperature and vibration. Instead of the traditional 60 degree vee thread design, the Spiralock thread form is a 30 degree “wedge” ramp cut at the root of the female thread. Under clamp load, the crests of the threads on any standard male bolt are drawn tightly against the wedge ramp. Since the Spiralock thread form is a mechanical solution to the loosening problem, it’s more tolerant of cyclic temperature changes than 60° threads using nylon or adhesives. It allows for both thermal expansion and contraction without slippage.
The 30 degree wedge ramp not only eliminates sideways motion that causes vibrational loosening, the company says, but also distributes the threaded joint’s load throughout all engaged threads. This claim, Spiralock says, is supported by a research study conducted by the Massachusetts Institute of Technology. Other studies show the load percentage on the first engaged thread with a Spiralock thread form is significantly lower, which further reduces possible bolt failure and improves product performance. Using this thread design, bolts spin freely until clamped to a final torqueretaining position, which eliminates galling during assembly and needed service repair.
![]() |
This photoelastic comparison of a connection using a Spiralock thread and a conventional thread indicates how the load carried by each engaged thread is more uniform with the Spiralock design. |
“Upon inspection every 250 hours, the Spiralock fasteners maintained joint integrity without losing torque for 15,000 cycles. “After their adoption, none have failed in the field to my knowledge,” Werner adds. “They’re not only self-locking but also re-usable during service without damage to the nut or stud. The Spiralock fasteners are now used on every Mack turbocharger mount across our vocational truck line and on the EGR valve mount on our highway truck line.”
Caterpillar has also adopted Spiralock fasteners for diesel engine applications such as turbocharger mounts, exhaust manifold joints and attachments, after thorough testing by its technical center.
“The Spiralock fasteners stay put under engine vibration, and withstand high temperature,” says Sutthiwan. “This improves reliability, upholds our reputation with customers, and lowers the need for service repair.” Gary Svidron, a design engineer for International Truck and Engine Corp., a Warrenville, Ill.-based manufacturer of trucks, buses and diesel engines, also sought fastener resistance to vibration and shock. He faced a design challenge in securely fastening a turbocharger to an exhaust manifold on a sixcylinder diesel engine used in trucks and buses, where fasteners had to retain clamping power at high temperatures.
During pre-production testing, standard nuts and other traditional fasteners came loose due to sustained road vibration, and adhesives simply didn’t work because engine-operating temperatures were too high.
“Joint integrity on the turbocharger/exhaust manifold was critical to prevent gasket leaks, warranty costs and exhaust leakage, which can cause particular problems in states like California with strict emissions standards,” says Svidron. “Moreover, truckers and bus drivers can’t tolerate downtime, since staying on the road is their livelihood. To keep them on the road and warranty costs down, we needed fasteners that quickly and securely clamped in place for the life of the engine. This would make it easy for our dealers’ service technicians who have to keep our customers on the road.”
After pre-production dynamometer and field testing, International Truck replaced standard flange nuts with stainless steel Spiralock fasteners. “We’ve not only solved the joint integrity problem, but also avoided potential assembly issues with prevailingtorque- style fasteners and improved assembly production,” says Svidron. “Since the Spiralock fasteners spin freely until it’s time to tighten them, they take significantly less time to tighten than resistance-heavy locking methods such as prevailing torque nuts.
“With four fasteners per assembly on volume of many thousands of engines per year, we’re saving a large amount of assembly time,” adds Svidron.
The international market is turning to the Spiralock thread form, the company says. Recently Shanghai Diesel Engine, one of the largest engine manufacturers in China, found deformed thread nuts unsatisfactory for its turbocharger outlet clamp assembly and turbocharger mount to exhaust manifold for use in trucks, buses and other applications.
“The deformed thread nuts were costly, difficult to assemble, and often damaged bolt threads during assembly,” says Jessie Zhang, a senior engineer at Shanghai Diesel Engine. “Damaged bolt threads meant the clamp assembly couldn’t be used because the bolt was welded to other parts. Without the clamp assembly, the engine wouldn’t properly connect to the exhaust pipeline, which could hurt engine performance, damage the gasket and cause injury.”
While Zhang was looking for a better machining process for the deformed thread nuts, she was contacted by Spiralock of China. “The design works like using a wedge to keep a door open,” says Zhang. “The thread form offers locking performance and vibration resistance in high temperature. It protects the bolt threads and clamped assembly from damage during assembly or service.
“In the past few years, we’ve produced tens of thousands of diesel engines with the Spiralock thread form, with very good results for the Chinese and international markets.”
More Stories
Buying Car Insurance in Toronto? Don’t Make These Rookie Mistakes
Extend Your Range, Maximize Your Storage with FRDM’s 45 Gallon Combo
How to Install a Ford Bumper Yourself (Step-by-Step Guide)