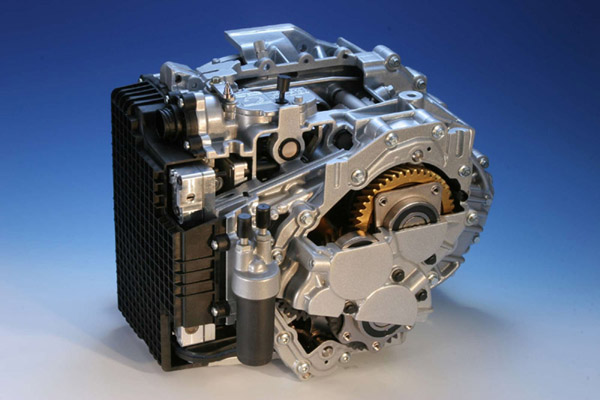
Invariably, the focus in hybrid vehicles falls on the power supplies – the driving force behind the vehicle, be it electric, fuel or gas.
There is, however, a second – equally important – challenge, which is transferring the power to the wheels. In order to find solutions, Getrag has teamed up with the Robert Bosch group, which recently opened its hybrid house in Ludwigsburg, 30km south of Getrag’s corporate headquarters in Untergruppenbach.
Delivering an annual volume of more than three million transmissions and a million axles, Getrag is the world’s largest independent manufacturer of transmissions, while Bosch is also a leader in its field.
The companies say their competencies complement each other. Getrag offers a broad product portfolio covering the entire drive train and especially dual-clutch transmission technology. As a leading supplier of engine and transmission management systems, while Bosch brings to the partnership comprehensive know-how in electrical machinery and the necessary power electronics.
Dieter Schlenkermann, Chairman of the Board of Management of the Getrag Group, says : “The cooperation we have established with the world’s largest supplier to the automotive industry is highly promising for the future development of hybrid drive technology. The know-how of both companies will put us in the position to offer our customers throughout the world cutting-edge solutions for future drive concepts.â€
Dr. Bernd Bohr, member of the Bosch Board of Management and Chairman of the Automotive Group, adds: “Together we can offer automobile manufacturers a highly integrated and compact hybrid system that will enable low fuel consumption and excellent vehicle dynamics.â€
The cooperation agreement covers the development and marketing of parallel hybrid systems in conjunction with dual-clutch transmissions and electrical final-drive units. Key aspects of the collaboration include the integration of mechanical and electrical components and the development of appropriate software. Hybrid drive systems combine an internal-combustion engine with an electric drive. In the case of parallel hybrids, the electric drive is fitted directly into the power flow of the drivetrain.
The electric drive is used as a motor when accelerating and is used to convert kinetic energy into electrical energy when braking. The dual-clutch transmission enables easy and energy-efficient automatic shifting. Collaboration work betweem the two companies also involves the development of final-drive units with directly integrated electric motors. Hybrid drive systems can significantly reduce fuel consumption, particularly in urban traffic. Depending on the system design, fuel savings of up to 20 percent can be achieved in the New European Driving Cycle (NEDC) as compared to drive systems relying exclusively on conventional gasoline engines.
Solutions being developed by Getrag and Bosch include:
Permanent synchronous drives.
According to Getrag, synchronous drives provide better power density than asynchronous machines. The power electronics module is at present placed in its own box. However, in order to combine functions such as the cooling of the electric motor and power electronics, Getrag has also developed integrated solutions where the power electronics are placed at or around the electric motor. This integration will, however, only be profitable along with standardization and high volumes, the company warns.
Parallel hybrid
Getrag and technology partner Bosch favor the parallel hybrid. With this system the power produced by the combustion engine and the electric motor work in parallel in the drive train. With serial hybrids the combustion engine drives a generator and it is the produced electricity only that powers the actual driving motor, which is a second electric motor.
Getrag and Bosch believe that there are two main factors supporting their technology. The first is that new combustion engines have a relatively wide range of low specific consumption, so the operating point optimization of the serial hybrids loses importance and makes the permanent double energy transformation uneconomic. Secondly, the hybridization is based on a conventional drive train. Thus one can react to the market acceptance of hybrids with smaller expenditure and particularly with fewer risks.
Electric axle
Another solution developed by the two partners is the electrical axle. With this system, the conventional drive train is supplemented by an axle that is propelled by electric motors. The big advantage of this variant – which is called, “through the road hybrid†– is that the conventional drive train can be used without modification.
For full hybrid functionality however, certain adjustments are needed, such as the stop/start capability or the engine switch-off during recuperation. Such a hybrid concept works particularly well with front wheel driven vehicles. With this hybrid variant the customer gets the interesting added value of an all-wheel drive without the additional weight of a transfer case and a prop shaft. The all wheel functionality is only limited by the capacity of the electrical storage.
Focus on efficiency
Getrag says, in the long run, it will not be crucial whether the electric motor has a few kilowatts more or less, but rather the efficiency of the hybrid system in use. Hardware is only second in importance to the management systems of the hybrid. And in this aspect the co-operation Getrag Bosch believe they are well positioned.
Getrag believes that hybrid is a technological innovation, where “evolution†has not yet substantially influenced the variety of technological variants. The actual situation is rather that each successful hybrid system initially supports the market success of the competing systems.
Dual clutch
The company says it is, however, “firmly convinced†that its approach of a Flexible Modular Hybrid based on a dual clutch transmission and the electrical rear axle – will establish itself and last the distance.
At the core of this concept is the use of a dual clutch transmission (DCT), which can also be used in the vehicle without hybridizing. One or two electric motors can be attached to this DCT in several ways.
The power and torque of the electric machines can be adapted to the respective targets- mild or full hybrid – without having to change the basis transmission. Thus the commercial risk of hybridization is considerably more manageable for the OEM and the transmission supplier. Hybrids are a highly complex technology, where vehicle manufacturer, transmission supplier and electrical specialist must co-operate very closely in order to be able to realize a successful system, the company warns.
Getrag developed dual clutch transmissions (DCT) for Inline and transaxle drives with torques from 250 Nm to more than 600 Nm. Apart from the good driving comfort the dual clutch transmissions are characterized by high efficiency and sporty shifting dynamics. Moreover, the ratios of the different gears can be adapted individually to the desired driving dynamics or to consumption and emission-optimal gradations of the target vehicle. With 6 or 7 forward gears the company says it can find a suitable solution for almost every application.
Getrag has extensive experience in the hybridization of automated transmissions and dual clutch transmissions. Projects include 42V technology, downsizing, different electric motor designs and electrical storage. “This engagement in the highly complex topic of hybrids has generated a lot of know-how that we share now in a co-operation with a competent electrical partner, says the company.
Focus on the customer
All considerations and concepts for hybridization have to be focused on customer benefits, believed Getrag.
Only then a system will be successful at the market and be able to contribute to the reduction of CO2 emissions. On the other hand the customer acceptance is a large unknown quantity in the hybrid calculation, the company says.
More Stories
Acoustic sensor systems and Fraunhofer measurement technology for in practical testing ͏
OSI Systems Receives $10 Million Order for Cargo and Vehicle Inspection Systems
Mitsubishi Electric Automotive America Launches Guardian Generation 3 Trial with Seeing Machines in North America