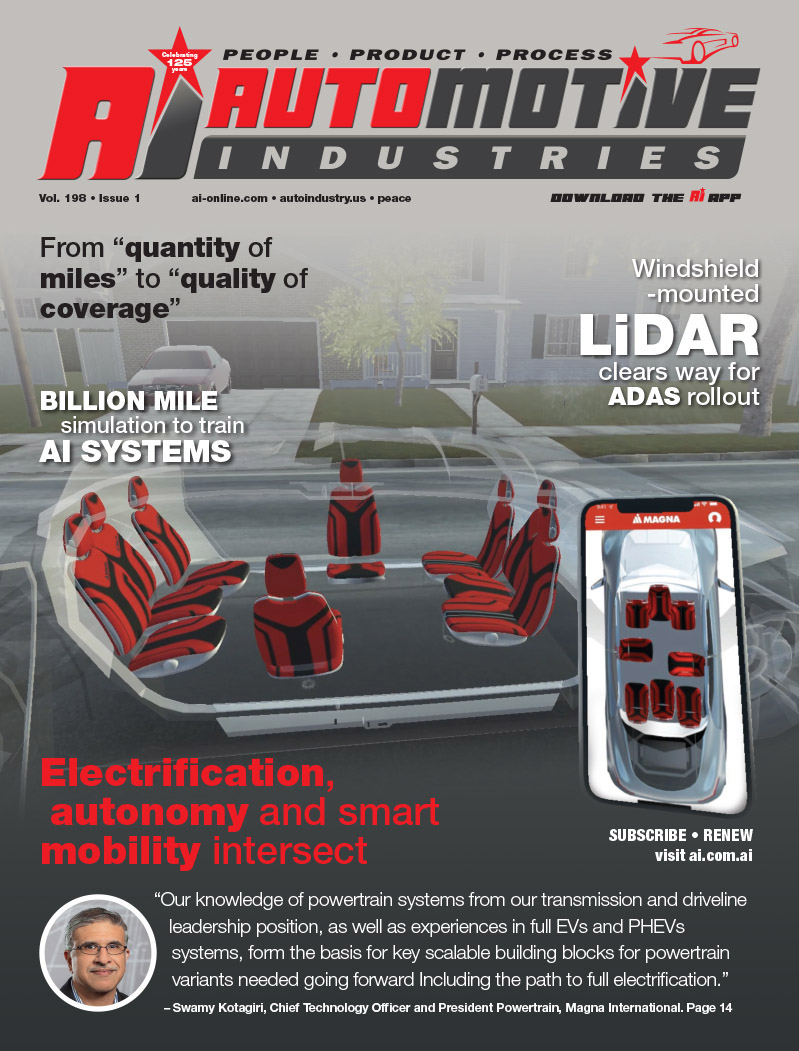
Over the last decade the automotive industry has increased the efficiency of diesel engines by decreasing the size of motors while enhancing the power. These down-sized motors achieve higher power per cubic inch as they have less weight and friction compared to their equivalent older technology motors.
However, higher performance per volume also means higher concentrations of the regulated nitric oxide (NOx) in the exhaust emissions. There are three main technologies use to limit temperature and the consequent NOX emissions.
NOx vs. Fuel Consumption.
The laws of thermodynamics dictate that smaller motors will result in higher combustion temperatures as we increase the motor efficiency. But, higher temperatures cause exponential increase in NOx emissions.
The industry is now faced with a dilemma requiring a cost effective, technologically feasible balance between elevated temperature for efficient combustion and the regulatory emission control of NOx and CO2. . These opposing objectives are forcing international competition in seeking technology solutions, to get the most efficient engine while meeting emission regulation at a reduced cost.
Historically emission level testing was done in the laboratory under a defined drive cycle, however, with the advent of mobile devices that allow emission monitoring in the drive mode. This is now trending towards both government regulatory agencies and the public, requiring companies to ensure balance between engine efficiency and emission under all driving conditions – the highest possible fuel efficiency while controlling the emission levels.
The emerging solution to this problem of controlling emission limits during normal driving operations is by combustion temperature reduction using regulated Exhaust Gas Recirculation (EGR), with particle filtering and chemical treatment of exhaust gases using additives such as AbBlue, and reduction of NOx by means of an SCR converter.
Reduced temperatures through EGR causes a decrease in efficiency as measured by power and fuel economy. The emission levels are now required to be met under all drive conditions.
The Solution: Temperature Reduction through Exhaust Gas Recirculation (EGR)
One efficient method of reducing cylinder temperatures is to minimize the amount of harmful NOx by Exhaust Gas Recirculation (EGR) where, a part of the exhaust gas is recycled to the cylinder after cooling. The combustion process produces temperatures far over 2000°F, and the cooler EGR functions as a ballast causing a reduction (from the non EGR 2000oF, in cylinder exhaust temperature). The EGR also reduces the O2 content in the cylinder, causing slower combustion at lower temperatures. The EGR concept for temperature reduction can be visualized by thinking about the addition of cold water to a hot drink. Lowering combustion temperatures by as little as 100-200°F results in significantly lower levels of NOx.
Current and future emissions regulations established by the EPA and the European Union require a verifiable measuring of the EGR rate for regulation purposes within the engine control unit. This requirement means, that measurement using a model is no longer a possibility.
There are various ways, however, to measure the EGR rate, either directly or indirectly
Use the Differential Pressure Principle to Measure EGR Mass Flow
Many US manufacturers of commercial vehicles have prioritized a direct measurement of the EGR. To accomplish this task, a Venturi is installed into the EGR flow in combination with an EGR-compatible differential pressure sensor. To measure the EGR rate, a filling-model of the motor is added to the equation, which calculates the total amount of gas flowing into the cylinder.
The direct measurement of the EGR mass flow offers advantages in that inaccuracies in the flow measurement has minimal influence on the EGR rate because of the low proportion (10-30%) of EGR compared to the fresh air.
Direct measurement of the EGR, however, does have a series of drawbacks: The extremely large pulsations of the EGR flow require fast sampling rates and high performance ECU calculation. These high rates cannot be supported by the inherently slow response of the dp-sensor-elements and the available µ-processors. These limitations result in measurement deviations significantly above 10% requiring complex engine map compensations. Based on speed, torque, and position of the EGR valve. Exacerbating these drawbacks, is the practical constraint in that it is not even possible to take a direct EGR reference measurement at the test bench –the measurement must instead be calculated indirectly using carbon balances. The EGR flow path, within the motor, is impacted with fouling from a sticky mix of condensates, soot, and ash. Over time, it becomes increasingly difficult to achieve an exact measurement of the EGR using Venturis, because of the obstructions caused by the accumulations on the walls of the tubes during the life span of the motor. In the worst case, pressure sensors become clogged and EGR measurement fails completely.
Manufacturers’ goal of achieving an EGR rate with an uncertainty of 10% or better can be accomplished with this method, but in order to be most effective, testing must be done at the test bench using clean measuring tubes. It is not effective during lifetime vehicle operation.
Use Thermal Air Mass Flow Meters (HFM) to Measure Air Mass
Thermal air mass flow meters are another method to directly measure air mass. Similar to the previous method, a filling model is needed to determine the EGR mass flow and the EGR rate.
However, unlike the method above, the air path is subject to far lower levels of contamination and deterioration than the EGR path. This prevents the extreme fouling problems that the EGR sensor encountered. Heat transfer flow meters (HFMs) are cost-effective and for cost reason widely employed by the passenger vehicle industry.
HFM meters accuracy for new units is worse than 5% and this accuracy deteriorates over time requiring highly complex and time consuming bench calibration for new units and drift compensation over life. HFM meter accuracy, without drift compensation by adjusting Lambda values, can be greater than 15%.
The high drift allowances and limited life span of HFMs (typically 70,000 miles) can be explained by looking at their measurement principle which infers flow rate based on the air flow cooling of a heated resistance element. The cooling rate of the resistor is proportional to the air flow rate. This measuring principles accuracy is highly sensitive to heat transfer variation caused by fouling, condensation or resistor corrosion
To minimize the fouling cause measurement issues, HFMs are generally installed either inside or directly downstream from the air filter. But this in turn results in the calibration of the HFM being dependent on the particles size, and moisture clogging of the air filter. Therefore Volkswagen introduced an inlet flow straightener for the HFM as a part of their solution to the DieselGate event.
Using HFMs is particularly problematic, though, especially in commercial vehicle applications: The HFM’s short lifespan is highly unsatisfactory for manufacturers of commercial vehicles—commercial vehicle motors are designed to last up to 1 million miles. Second, it is difficult to efficiently adjust the complex calibration of the HFM sensors for commercial vehicle motors because the air path is engineered differently for each type of vehicle. Finally, commercial vehicle motors are often manufactured in relatively small lot sizes and then adapted to many different types of vehicles. It would be a time-consuming and expensive process to develop a customized engine map for each specific vehicle.
Use the Differential Pressure Principle to Measure Air Mass
We now present a differential pressure based MAF smart sensor TFI4 developed by systec Controls in Puchheim, Germany. The TFI4 contains three sensors: Temperature, absolute pressure, differential pressure and a computer chip with our leading algorithms that compute and transmit, over CAN, accurate flow value under various flow conditions such as pulsations. Also, given the multiplicity of sensors and software modification capability, the TFI4 can be considered as a Swiss knife which provides the flexibility of using the CAN transmitted data for diagnostics, detecting misfires, observing the operating conditions both in operation and development. TFI4 offers durable and long lasting life which is a must for the dirty tractor operating conditions while transmitting the OBD messages to the Engine Control Unit. All the diagnostic and flow computations are performed by the TFI4 smart sensor, and the result transmitted over the CAN bus. This relieves the main vehicle engine control processor from the burden of performing any flow or flow correction functions. Additionally all the problems associated with analog signal such as aliasing and noise corruption are avoided.
TFI4 Sensor mounted on charged air pipe with integrated nozzle
Compared to the methods outlined above, using the TFI4 to measure air mass flow has several distinct advantages:
Increased Precision at Close Proximity to Motor
TFI4 measures pressure, temperature, and flow rates at intervals exceeding 1000 times per second. Pressure and flow-through pulsations are measured in real time, then reprocessed, filtered and transmitted with digital precision to the control unit via CAN.
Results at engine test benches are accurate to within 2% Full Scale: TFI4 can be installed directly at the motor either preceding or after the turbocharger, after the charge air cooler, or even after the throttle valve. This flexibility means, that air mass precision levels throughout the entire engine map are better than 2%, and in the case of medium to high mass flows they even reach levels of better than 1%.
The values illustrated in the following diagram illustrate a typical commercial vehicle engine map at a position in close proximity to the motor as outlined above. It only takes a few days’ time to integrate the TFI4 sensor into an application and at an engine test bench, because complex engine maps are unnecessary. Sensor precision is, to a great degree, not affected by load, EGR rates, rotational speed, or throttle valve position.
The ability to package the sensor in close proximity to the motor, alleviates the need for engine map calibrations for different commercial vehicle applications – a huge test and calibration labor savings.
Sturdy and Durable
Measurement of the air mass with nozzles, pitot tubes, or Venturis is not impacted at all by general conditions of fouling or deterioration within the air flow. Even Blow-By (crankcase exhaust) or temporary reverse flows of the EGR do not have a negative influence on the measured values. Occasionally, when sensors are installed directly into the EGR, some of the same limitations regarding fouling arise as were described above.
The pressure sensor technology on the TFI4 is media -compatible, low-drift, and durable. The TFI4 sensor platform was specifically developed and tested to address the requirements and challenges of commercial vehicles.
Minimal Pressure Loss
During the development of the TFI4 sensor technology, particular attention was paid to marginal remaining amounts of pressure loss. In order to assure high levels of precision in situations involving minimal differential pressures, every individual TFI4 sensor is individually calibrated to compensate for pressure and temperature during the manufacturing process. The result is a zero-point stability which is 200 to 1000 times better than that of an uncompensated sensor.
Because of the zero-point stability at +/-10 Pa, low differential pressures and minimal flow rates can be reliably measured. This makes it possible to have metering ranges of 1:10 with a maximum pressure loss of maximum 1000Pa and metering ranges of 1:15 with a maximum pressure loss of 2200Pa. Since the pressure losses are extremely small, they have virtually no influence on engine performance, even if the TFI4 is placed on the low pressure path in front of the turbo charger.
Precise sensor technology is important, but equally important is the customized design of the differential pressure element (primary element). systec Controls supports motor manufacturers in selecting the best possible mounting position, in selecting and designing the optimal primary element, and in assembling the sensor into the engine test bench. systec has developed specialized primary elements for this very purpose, elements which have been shown to result in significantly lower levels of pressure losses then the ISO 5167 primary elements which are comply with motor’s short straight inlets.
Summary and Looking to the Future
Thermal flow meters are only practical when large lot sizes justify the higher expense of applying the sensors onto the motor and where shorter life spans are sufficient—in other words, in passenger vehicles. Diesel Gate shows that even this increased investment does not always have the desired result, and remediation efforts are required.
Traditionally, the only solution for commercial vehicle manufacturers to determine the EGR rate at close proximity to the motor and thus independent of vehicle type was to measure the EGR directly within the motor. While it is true that EGR sensors and venturis are expensive and that their application onto the motor is labor intensive, it is also true that the high R&D cost has to be performed only once for motors, that are produced for a high variety of vehicles.
Now that it is possible to measure air volume in close proximity to the motor, the way has been paved for an optimal measuring process. Sensors can be integrated directly onto motors at the test bench, within just a few hours , providing precise measurements. The sensors have a long life span. The additional cost of Venturi and our smart sensor (over HFMs) is offset by the elimination of expensive engine map needs and the need for dedicated equipment to measure pressure or temperature. This fact alone makes this method increasingly relevant, especially for medium duty and heavy duty commercial vehicle motors. In the areas of lightweight commercial vehicle motors and personal vehicles, pre-production developers have expressed interest in the new technology and testing is proceeding on vehicles.
More Stories
Automotive Industries (AI) Newsletter April 2025
GlobalLogic Pioneering Software-Defined Vehicles, AI Innovation, and Sustainable Solutions for the Future of Automotive Mobility
Cybord TCI – The Future of Manufacturing Integrity