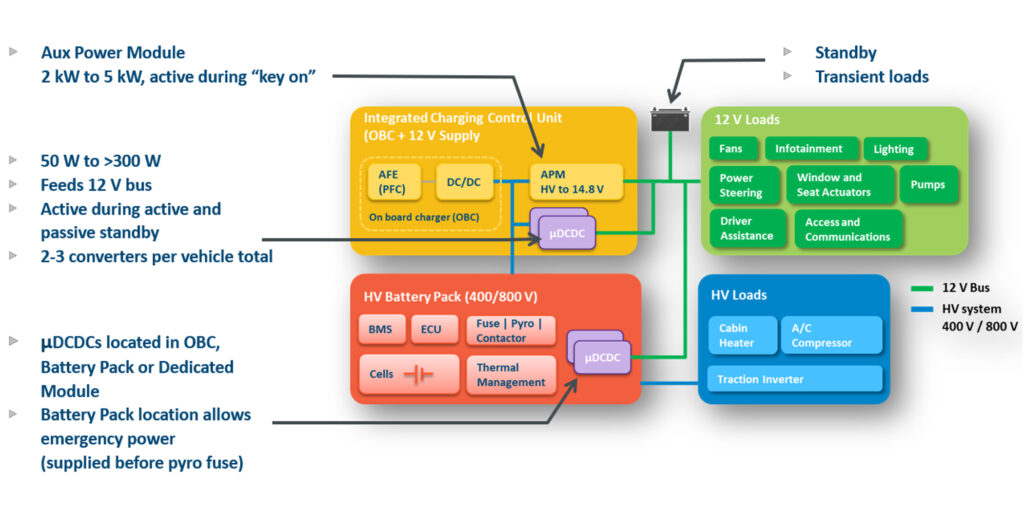
Fig 1: 12 V EV architecture with µDCDC
Fig 1: 12 V EV architecture with µDCDC
Many countries are enacting legislation to increase the number of electric vehicles (EV), with
the goal of phasing out or eventually banning petrol and diesel vehicles. Whilst early adopters
may have been motived by environmental concerns, there remains a sizable portion of the
market that is also concerned with range limitations and charging times of EVs.
The automotive industry is being challenged to innovate and create solutions that appeal to a
larger audience, and this is driving the trend to higher battery voltages. Most of the passenger
EVs on the road today run using 400V batteries. EV busses and trucks are 600V class vehicles
and 800V is starting to be adopted for passenger vehicles.
The introduction of 800V systems, a significant step up from the existing 400V systems, is
happening faster than many predicted. What are the benefits of an 800V system and how do
they help solve some of the problems that have been barriers to consumers and slowed the
roll-out of electric vehicles?
How does an 800V battery impact the vehicle design?
The core of an electric motor is a rotor, driven by generating a changing magnetic field. The
higher voltage, means the motor can run much faster, and be physically smaller. This reduction
in size, not only reduces weight, but frees up valuable space and reduces material costs,
specifically copper, which is currently at a 45 year high. A higher voltage supplies the same
power with less current. Here the voltage doubles, so the current halves, resulting in smaller,
lighter cables, providing a secondary reduction in weight, space and cost. The 800V architecture
provides an increase in power density; the smaller motors can spin faster, up to 20,000 rpm,
creating more efficient motors.
The reduced weight immediately extends the range of the vehicle. Lower weight will also
improve acceleration, valuable in the high-end sports car market. Alternatively, the extra space
can be used for additional batteries, which while increasing the weight, will result in extending
the range due to the increased battery capacity. It’s worth noting here that more batteries will
also increase the charging time. This creates options for the vehicle designers enabling them to
trade acceleration for range (range is more valuable for commercial vehicles) and adapt the
vehicle design to focus on specific markets. The reduction in costs also makes the solution more
accessible to the mid-range consumer market, not just high-performance vehicles.
Range is one of the key items when considering the switch to electric vehicles. For some, it’s a
matter of convenience, and a desire to make long journeys easier. For commercial vehicles
extending the range means more efficient delivery routes, more time out on the road, fewer
vehicles to cover the same area and better operating costs.
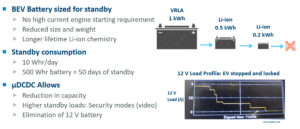
800V enables reduces charging time
Charging time is a challenge for consumers, as well as commercial vehicles. For urban drivers
and commuters, overnight charging at home is often enough. However, planning a longer trip,
especially if it is several times the range of the vehicle, means also planning a route that
provides charging stations at appropriate times. The driver can hope the station is available
when they arrive, and that there is something to do while the vehicle charges. For commercial
vehicles the issue is more complicated, as returning to the depot to recharge, or having the
vehicle sit idle for 90 minutes while it charges in the field, cuts into productivity and directly
impacts the business’s bottom line.
How does an 800V architecture help? As we’ve noted before, doubling the voltage cuts the
current in half for the same power. One of the losses with charging is power lost through heat
dissipation. The heat lost is proportional to the current, and so the heat generated and power
lost is reduced in an 800V system, because the current is reduced. This is referred to as
increased power retention, as less power is lost, more power makes it into the battery,
resulting in a faster charge.
Both Porsche and Kia have new all electric vehicles whose range is starting to approach the
median range for petrol cars, and with charging times more comparable to refueling at a petrol
station with a quick stop to pick up supplies. The newest range of charging stations deployed
have a 400kW max rating, which is more than enough for the 800V architecture.
Porsche’s fully electric sports car, the Taycan has a range of 420 km (260 miles). It uses the
800V battery architecture, and can charge from 5% to 80% in just 22.5 minutes on a fast-
charging station at 300A, (240kW). It’s still capable of using 400V charging stations, which
would take around 90 minutes. Kia’s announced their EV6 800V architecture car, charges from
10% to 80% charging in just 18 mins, using a maximum power of 239kW, and has an extended
range version with 480 km (300 miles).
Fast charging times make a crucial difference to commercial vehicles, that can have a quick
charge to extend their working day, and delay a return to the depot for a full charge until the
evening. Importantly, these faster charging times also fit into the 30 to 40 min mandated rest
periods in many regions.
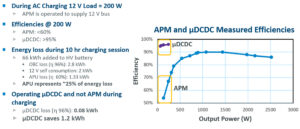
800V adoption has been faster than expected.
The automotive market has adopted the 800V architecture faster that was initially anticipated.
Porsche, Audi, Kia all have 800V sportscar designs. GM are deploying 800V soon, likely in their
trucks. China appears to be standardizing on an 800V architecture. As is typical for the
automotive market, innovations start in the higher-end vehicles and slowly work their way
down to the mass market, as the technology becomes cheaper. The benefits we have discussed,
that the 800V systems bring, include cost savings, that the mid-range consumer market can
utilize much sooner than was first thought.
As the automotive market embraces the 800V architecture, we will undoubtedly see companies
pushing the benefits of higher voltage systems even further. These benefits scale up, and so
900V and beyond can increase these further, pushing range, weight and charging times even
more. The infrastructure will need to keep pace; the new 400W charging stations are already
enabling this direction.
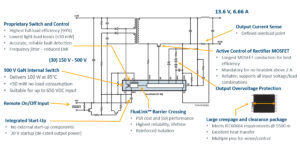
What are some of the design considerations for the power solution within an 800V system?
800V is a significant step up from 400V systems, and requires a different approach than
components derived from AC mains controllers.
800V is the nominal battery voltage, in practice, it is usually specified as 800 +/- 15% (920V) to
allow the battery voltage to lift during regenerative braking or normal charging. If the
application requires a flyback converter, an additional 120 V must be added to allow for the
reflected output voltage on the transformer primary and the transformer leakage inductance
spike. This takes the voltage to 1040 V. If we then allow for the usual 20 % derating, it now
requires a switching device rated at 1.3kV. This is generally achieved using a flyback or buck
control device with an external 1.5 kV automotive qualified MOSFET – apparently these are
quite rare at lower current levels.
Another important design consideration is the need for a low voltage start-up, typically 30 to
40V. The vehicle safety systems need to power up first, to make sure all the control electronics
are operational before anything can start to move, or faults potentially occur. Designing a
power supply that runs from 30V to 1300V can be challenging.
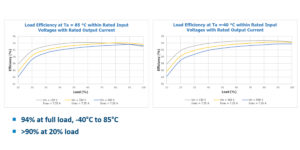
New high voltage solutions from Power Integrations
Power Integrations has released two new AEC-Q100 qualified, 1700-volt rated ICs, adding to its
InnoSwitch tm 3-AQ family. These two new devices solve these design challenges for 800V
systems and bring a host of valuable features needed in the automotive space, and a path to
higher voltages for future designs.
This simple fly-back converter design integrates the silicon carbide MOSFET and both primary
and secondary controllers. The InnoSwitch tm 3-AQ uses FluxLink tm for isolation, allowing the
secondary controller to be the main controller. This unusual architecture means the secondary
side determines when to switch the primary, enabling synchronous rectification without the
usual draw backs, such as incorrect switching time, and covering fault conditions.
InnoSwitch tm 3-AQ has a 30V start-up, critical to power up the safety systems in automotive
applications. Discrete solutions require additional components on the primary side, to make the
30V start-up possible, which comes at quite a cost. Every component attached to the high
voltage rail has to be tested for several failure modes, so PI’s higher integration brings system
savings, reducing tests cases by up to 50%.
Part count reduction is crucial in EVs. Fewer parts results in a reduced failure rate, due to the
parts themselves, but also fewer solder joints – increasing reliability. Board area savings are
even more significant, as this reduces weight, increases the power density, creating more
interior space, which are all valuable commodities in the EV market.
InnoSwitch tm 3-AQ’s unique architecture sees it sit across the isolation barrier, on an area of the
PCB which can’t usually be populated. In practice it can be placed, underneath the transformer.
This design takes up no PCB space which makes a meaningful difference to designers.
The tight output regulation eliminates the need for additional DC-DC converters to produce
lower rails; they can be added directly from the controller. Due to the FLuxLinkt m architecture
and +/-2% regulation, it only takes 2 switching cycles to get from zero load to full load, and slew
the power delivery from zero to max. This means the output capacitors are also much smaller.
With efficiency over 90%, the heat dissipation is reduced enough to eliminate the need for an
external heatsink. These features create further reductions in size, space and component count,
with all the benefits that brings.
The no-load power consumption isn’t often a critical parameter, but for an EV, where the
battery is always connected, this could drain a parked vehicle’s battery. The <15mW offered by
these new InnoSwitch tm 3-AQ parts ensure a passenger returning to their car at an airport won’t
be stranded.
With the addition of the new 50W and 70W output devices, the InnoSwitch tm 3-AQ family from
Power Integrations now has solutions for EV designs using 400V, 600V, 800V and beyond.
For more information on Power Integrations products, please visit power.com
More Stories
What You Should Know Before Filing a Car Accident Claim
Injured in a Car Accident in St. Louis? Here’s What to Do Next
Historic Sportscar Racing (HSR) and Goodyear Announce Multi-Year Partnership