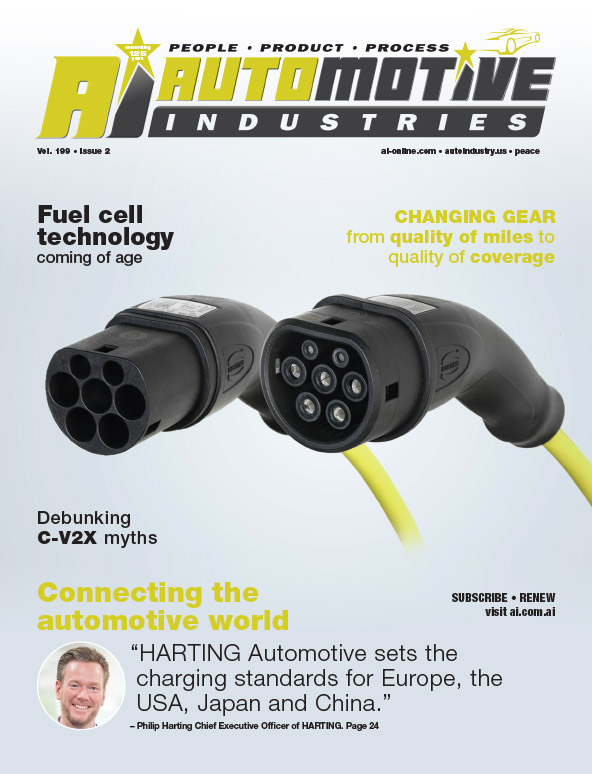
Prolonged charging times are regarded as one of the major obstacles putting the brakes on
electromobility. Now, however, thanks to the 800-volt system from connector specialist HARTING,
charging will hardly take much longer than filling up at the pump.
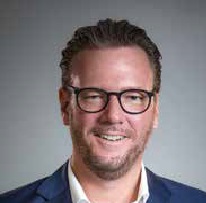
Fielding its extensive range of proprietary connectors, the familyowned and managed company masters the entire value chain – from power generation, distribution and storage all the way through to the vehicle charging plug. Transmission not only involves power, but also information – a key technology for smart power grids.
Electromobility decade
The automotive industry concurs that the 2020s must go down as the electromobility decade. If car manufacturers want to avoid massive penalties the EU imposes on excessively high CO2 fleet values, there is practically only one way out: the share of electric vehicles must increase drastically. Volkswagen, for example, wants to electrify 40% of its models by the end of the decade in order to comply with the EU’s CO2 targets. However, there is one great unknown in these considerations, and that is the customer. Apart from the early adopters, who are totally committed to driving electrically, the number of motorists accepting the disadvantages that electric cars usually entail is modest at best. Hefty price tags, limited range, extended charging times and an inadequate charging infrastructure are the most frequent reasons motorists cite when asked why they have not bought an electric car.
And even those who already drive electric are dissatisfied with the charging situation. According to a survey by the German USCALE management consultancy, only 43% of the 1,200 respondents were satisfied with the charging process. Just 59% would recommend their electric vehicle to others, which is a very low figure compared to the accustomed brand loyalty of German car customers. One thing is clear: the “user experience” must be decidedly upgraded in order to help e-mobility achieve a breakthrough.
Different OEM strategies
Car manufacturers are pursuing different strategies to make electric cars more suitable for everyday use. E-car pioneer Tesla is taking especially large batteries on board in order to ensure a long range. But the battery of an electric car is not only expensive and heavy, its production also pollutes the environment. For example, according to the Agora Verkehrswende, the production of one kilowatt hour of battery capacity causes 145 kilograms of CO2 in the European electricity mix. An electric car must first deal with this climate-gas burden on its life cycle before the environmental balance becomes positive. There is also the question of what happens to the battery at the end of the car’s life. Will it be disposed of as hazardous waste, recycled or used as a stationary power storage unit? The latter is the most sensible option in terms of resource conservation. Instead of opting for an oversized battery, whose capacity is rarely used anyway, some car manufacturers are pursuing a different strategy: if the charging process is shortened to such an extent that it is hardly longer than filling up with gasoline or diesel, the range and battery size are less critical. The Porsche Taycan, for example, is the first electric car to use an 800-volt electrical system instead of the usual 400 volts. The double voltage means that much more power can be transmitted at the same level of current – which not only shortens charging times but also improves driving performance – a welcome additional benefit for a sports car brand.
The Zuffenhausen-based company says a range of 100 kilometers is possible after four minutes “refueling”. Currently, the network of 800-volt/350-kW fast charging stations is growing in Germany. At present, the Ionity joint venture is advancing these. But even with a charging capacity of 150 kW, the Taycan would be fit for around 300 kilometers after half an hour at the charging pole. In addition to Porsche, the South Korean Hyundai Group is committing to the technology, while other manufacturers are likely to follow.
800-volt charging
The HARTING Technology Group ranks as the supplier company that has now enabled 800-volt technology on the charging side. As a Tier 1 supplier, the family-owned and managed company from Espelkamp in Westphalia, Germany, is supplying charging technology for VW’s electric cars and also to BMW. HARTING caters to all the relevant charging standards for Europe, the USA, Japan and China.
“The transmission of energy and information plays a central role in electromobility as well as in mechanical engineering, so it is only logical that HARTING is also involved in this field – with increasing success,” says Philip Harting, CEO of the Group. Over 700 of the 5,300 HARTING employees worldwide are engineers and scientists. The company has developed a technology that allows an electric car to be charged in record time – with up to 1,000 volts. The technology makes it possible to charge an electric car as quickly as refueling with gas or diesel. “Achieving 80% of the vehicle’s range in 15 minutes – that is a genuine quantum leap,” says Marco Grinblats, Managing Director of HARTING Automotive.
High speed charging
HARTING thought out of the box to speed up the charging: “If you want to transfer a lot of energy in such a short time, the cable cross-section has to be larger. But this would make the charging cable too thick and difficult to handle. The alternative is to cool the cable. This was the course we pursued together with our customer. Thanks to the cooling the cable remains flexible and can still transfer 350 kilowatts of power with 800 volts of charging current. HARTING also supplies the entire cooling circuit,” Grinblats told Automotive Industries. The new technology also creates new utilization profiles for electric cars. As Grinblats goes on to comment: “In terms of your daily commute to work, you’ll charge at home, and over longer distances at fast or ultra-fast charging stations. This means that longer distance journeys will also become attractive for drivers of electro-cars”.
With these advances, HARTING is a salient example of how companies originally active outside of the industry inspire the automotive sector to develop new technologies. The ownermanaged family business develops and produces electrical, electronic and optical connectors, transmission and network technology and software, mainly for machine building and plant engineering customers. Since its inception in 1945, the world market leader for industrial connection technology has advanced to become a high-tech company providing solutions for the three “lifelines” of every machine: “Power”, “Signal” and “Data”.
The HARTING Automotive subsidiary develops and produces vehicle charging cables and charging equipment for electric and plug-in hybrid vehicles, while also supplying Mode 2 charging cables, Mode 3 charging cables and DC fast charging connectors with approvals and certifications for all specific markets and legal requirements worldwide.
In addition, the company is active as a technology partner for the entire electrical energy process chain – from regenerative generation and harnessing wind turbines to transformer stations and overhead lines, and all the way through to standard and fast charging stations.
Battery storage
The HARTING Technology Group also has an innovative solution for battery storage modules. The Han® S connector range has been especially developed to cater to the demands of high-volume batter storage modules. “The demand for such storage modules is booming worldwide,” says Jon DeSouza, President & CEO of HARTING Americas. The new range meets the relevant technical requirements stipulated by the latest standards for stational power storage systems (such as UL 4128, for example), and offers users optimal security and safety for the connected units.
HARTING connectors are encountered universally, wherever energy and data are transmitted. “We provide connectors that are predestined for the extraordinary stresses and strains due to location, environment, climate, corrosion and other environmental influences impacting on onshore and offshore facilities and plants,” says Philip Harting.
Battery second life
These competencies also play a role in the secondary use of batteries propelling electric cars. If the lithium-ion cells of a drive battery no longer have sufficient capacity for use in a car, they can still find use in stationary energy storage units. Such storage systems play a pivotal role in the efficient use of wind and solar energy.
The energy transition away from nuclear and coal-fired power generation will only succeed if regenerative electricity can be stored in the grids to cater to peak loads. This is due to the fact that sun and wind often supply energy when it is not needed.
HARTING has developed accessories for such energy storage systems that automatically guide the two sides of a plug connection into the correct position for “blind” plugging. In this way, battery modules can be replaced rapidly and without errors. Using this technology drawer systems for energy storage units can be installed quickly and conveniently. This enables the intelligent secondary use of lithium-ion batteries, thereby further improving the environmental balance of electric cars. Even if the battery is still onboard the vehicle, it can still serve as a power storage unit as a buffer for a heavily loaded power grid. This means that electric cars can store the electricity generated in their own photovoltaic system and feed it back into the grid at night. The drive battery can also be used to stabilize the power grid during voltage and consumption peaks if the charging station has the appropriate intelligence and enables bidirectional charging.
Further innovation
In order to help electromobility achieve a breakthrough, however, further innovations will be necessary – that is, when vehicles are not only electric but also autonomous. But who will be charging vehicles that no longer have drivers? HARTING joined forces with robotics specialist KUKA and came up with an answer to this question: an automatic charging system. This idea was showcased by the Rinspeed “microSNAP”, a vehicle study by Swiss automotive visionary Frank M. Rinderknecht. The idea behind the “microSNAP”: chassis, drive (“skateboard” and superstructures “pods”) can be separated and rapidly exchanged. In this way, a wide variety of superstructures use the currently available “skateboards” – whether for transporting people, packages or food. In this context, the “skateboard” drives autonomously.
Robo-charging
In order to also recharge the battery independently, HARTING developed the corresponding robot-controlled charging station together with KUKA. A KUKA robot inserts the HARTING charging plug and terminates the charging process when the drive battery has reached the required charge level. As a result, the vehicle is ready for use again after a very short time. This solution offers a wide range of potential applications. Automated charging will also be playing a role in the commercial vehicle sector: Electric buses are mainly charged overnight, but they are parked bumper to bumper, in very tight spaces in depots. There is often not enough space to accommodate charging stations and the manual handling of charging plugs. Here too, HARTING is also working on appropriate solutions.
IT security
For years, HARTING has been picking up on Rinspeed’s AutoVisions to demonstrate possible application areas for its innovations – whether it’s the fast charging technology for electric cars or the MICA (Modular Industry Computing Architecture), a powerful small computer that can be employed in many different ways. MICA digitizes machines just like cars, processes data and networks systems with the cloud in order to leverage the information gained. In this way, MICA can be integrated into the charging station. The data of the internal hardware of the charging station (charge controller, smart meter, etc.) are transmitted to the MICA either via Modbus or via the internal Ethernet interfaces. The MICA verifies and encrypts the data and then forwards to the back-end system via LTE modem. In reverse order, the release for the socket of the charging station is sent from the back-end system to the MICA in a tamper-proof manner. If several charging points are used at the same location according to the master-slave principle, the MICA in the master charging point can be harnessed as a tunnel server for the other charging points without necessitating their own Internet connection. Consequently, MICA guarantees a high level of IT security and data protection. The unit also ensures that the billing of the “tanked” electricity complies with calibration law. To date, German calibration legislation has represented one of the regulatory hurdles hampering the expansion of charging infrastructures. In the meantime, however, this roadblock has been dismantled. “Without intelligent and secure electricity grids, neither electromobility nor the energy transition will succeed,” as Philip Harting concludes
More Stories
Automotive Industries (AI) Newsletter April 2025
GlobalLogic Pioneering Software-Defined Vehicles, AI Innovation, and Sustainable Solutions for the Future of Automotive Mobility
Cybord TCI – The Future of Manufacturing Integrity