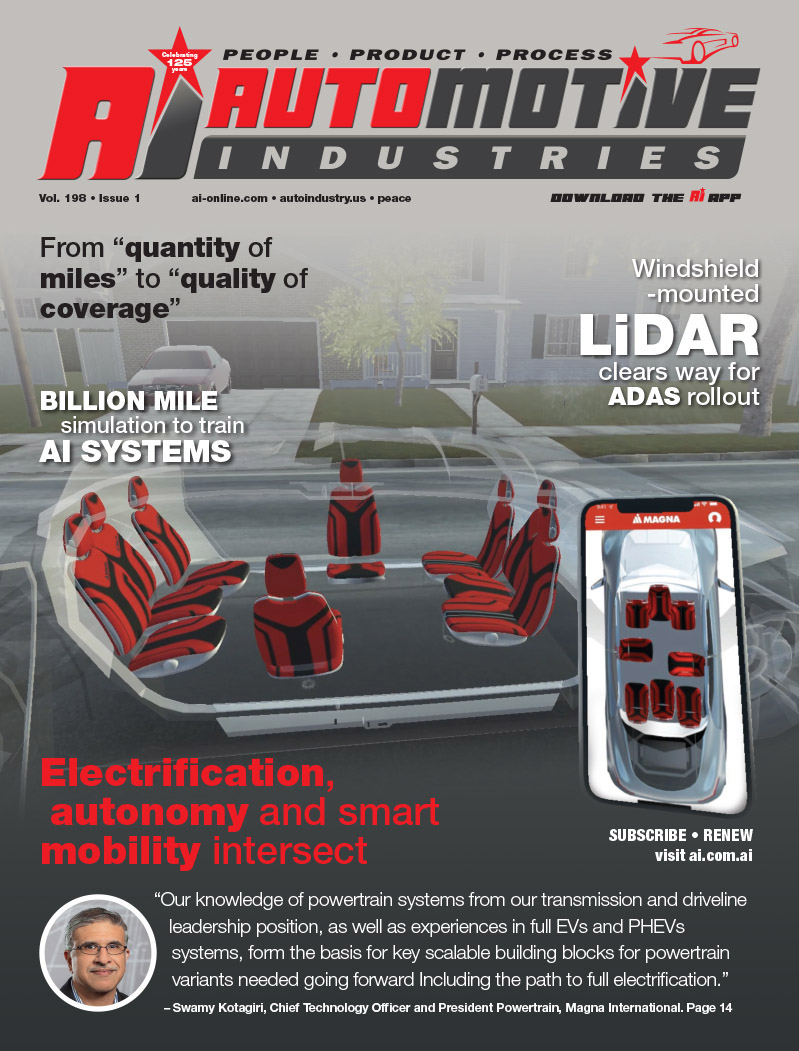
“We have forms to fill out forms,” says a plant manager of one organization.
Another says, “Our quality manager made our system bullet-proof. We pass our audits, but getting work done is often hindered by all of the bureaucracy.”
Does your quality system provide a return on investment above the costs of maintenance? Or, does your quality system consume extensive resources to support certain elements, particularly non-value added activities such as managing the abundance of paper, records and forms?
Case studies reveal some of the primary causes for symptoms such as those described above can be summarized in the following scenario: misinterpretation of ISO/QS-9000 requirements, poorly designed systems that lack a broad focus on business needs and poorly executed systems. It is not uncommon to see quality manuals that align exactly with the table of contents of QS- 9000. The problem is not many businesses are organized in that fashion. A better design would be one that aligns your quality systems with your business processes and drives improvement based on business results.
Your quality system should not be managed separately (i.e., by the quality manager) from your core business processes. This approach may result in a lack of sufficient perspective on broader business needs and cause improvement efforts to be misaligned with your business strategy. Your quality system should be integrated with your key business processes and work seamlessly as a system.
Given the emphasis that ISO 9001 and QS-9000 places on procedures, documentation and records, it is not surprising many quality systems are paper driven. Add to this the common practice of focusing on compliance and passing audits, it is not surprising that well-intentioned people leading the charge to get registered get buried in the details and lose sight of the spirit and intent of the requirements.
If effectiveness and value of a quality system is in doubt, answering the following questions may provide some insight:
- Is there a preponderance of paper in your business systems?
- Does the level of attention and activity increase significantly before audits?
- Do people scramble to “back-fill” forms and records to make the system appear to be working?
- Is there an abundance of data without meaningful analysis and improvement?
- Do internal auditors operate as “quality cops”?
- Are the same nonconformances chronically identified during audits?
- Is there a lack of broad ownership of the system?
- Is there a lack of data driven performance systems?
- Is there a lack of consequence for poor quality?
Another significant distinction is the greatly reduced emphasis on documentation (i.e., only eight documented procedures required). With the reduced requirement for documentation, evidence of conformance must shift from paper to results.
For those organizations using Lean Enterprise as part of their strategy, simplification of documents and information flow is just as important as simplification of manufacturing. To make your organization truly lean, there should be a focus on the entire value stream including document and information flow between production and support, technical and administrative functions. Redesigning your quality system does not have to be a daunting task if some simple and basic themes are followed. Things to consider when designing your quality system should include:
- Develop business and operational performance metrics (e.g., customer satisfaction, product quality, defect rates, returned product, scrapped product, waste, cycle times, sales/profit per employee and delivery performance)
- Identify value streams in your production, support, and administrative systems.
- Use a cross-functional team approach to redesign your quality system.
- Implement a meaningful continuous improvement system linked to performance data and business strategies.
- Identify and phase out procedures that are not needed for compliance and are not adding value.
- Clarify instructions and procedures that are vague or ambiguous.
- Simplify overly complex or detailed instructions and procedures.
- Construct a documentation architecture with a logical document hierarchy.
- Eliminate redundant information and data appearing on multiple forms or records.
- Establish efficient paper and information flow (refer to lean techniques).
- Establish clear linkages between upstream and downstream processes.

It can be done. Data supports that some efforts to achieve a value added quality system were successful. Many companies reported a return on investment from their quality systems of up to seven percent of annual sales above the maintenance costs of their quality system (source: AIAG quality survey). Some companies have designed and implemented quality systems that provide value in terms of better quality, less scrap, less waste and improved customer satisfaction.
With looming deadlines for conversion to ISO/TS 16949:2002 it may be a good time to assess the effectiveness and value of your quality system. The choice is clear; you may continue to accept less than acceptable performance and drown in paper, or take advantage of the transition period to regain control of your business and remove the burden of a quality system that is measured in pounds of paper rather than dollars saved.
Ken Gaunt is a Manager with Plante & Moran’s Process, Program and Quality Management Team.
More Stories
8 Best Plastic Welding Techniques for Automotive Manufacturing
5 Big Reasons to Choose LED Bulbs for Your Car Headlights
How much does it cost to ship a car on Amtrak Auto Train?