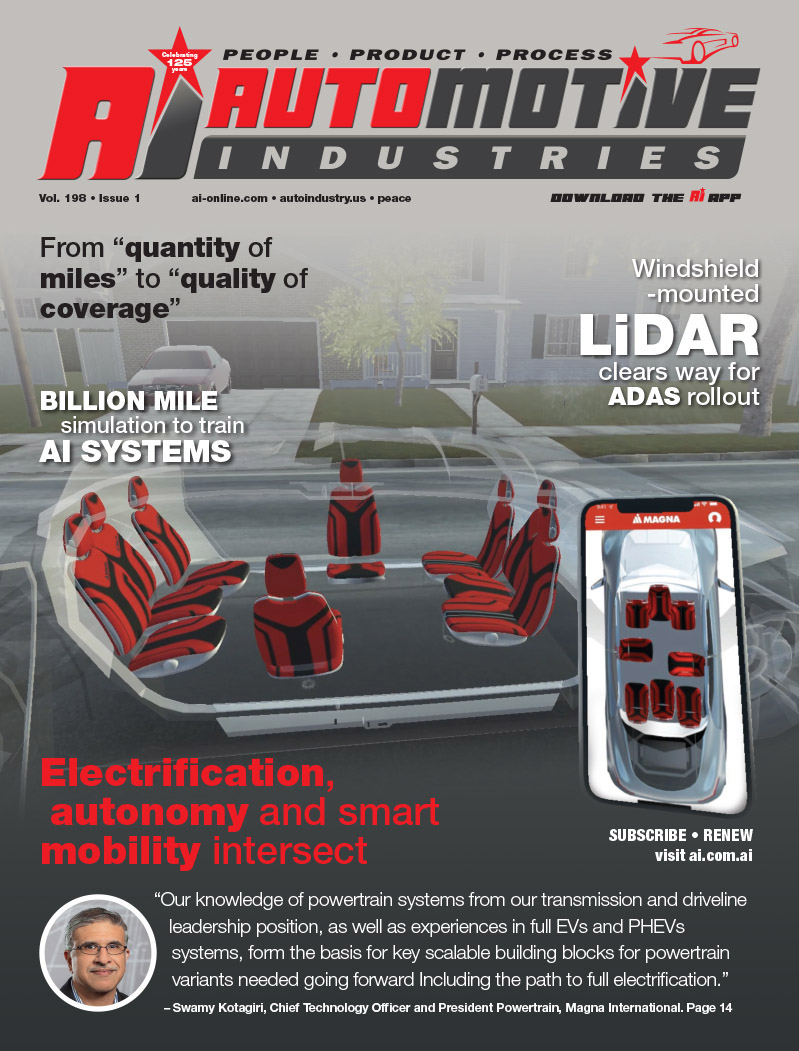
Smart’s new forvision has been described as a “showcase” of technologies for sustainable and holistic electric mobility of the future.
Unveiled at the 2011 Frankfurt Motor Show, it was a platform in which the researchers and designers “intentionally realised a mixture of visionary materials and technologies in the concept vehicle – some of these are still at a laboratory stage, while others have a realistic chance of entering series production,” says the company.
Much of the innovation is the result of a partnership between Daimler and BASF, with the focus on energy efficiency, lightweight design and temperature management.
Automotive Industries (AI) asked Dr. Christian Fischer, president Polymer Research at BASF how well the partnership works.
Fischer: We’ve worked very closely with Daimler for a number of decades. After all, BASF is the largest chemical supplier to the automotive industry with sales last year alone of close to eight billion euro. Our key strengths compared to others are that we have both very broad product and technology portfolios. In the joint project with Daimler we have successfully developed a holistic approach for the electric mobility of the future.
The three pillars we were focusing on were lightweight construction, temperature management and energy efficiency.
AI: What did BASF’s material and system competence bring to the vehicle in terms of lightweight design?
Fischer: The key lightweight materials are: the first all-plastic wheel rim suitable for large volume production. It consists of long-glass-fibre-reinforced Ultramid Structure. The weight saving in comparison to aluminium is three kilograms each, so we are already talking about 12kg of weight savings. The second is the all-plastic lightweight seat developed combining various BASF materials that not only save weight – and thus energy – but also provide more comfort. The load bearing part is made again of the polyamide Ultramid, a one-piece self-supporting seat shell that leads to a significant reduction in weight. With the help of e-textile technology, the seat heating can be directly integrated in textiles and be near the body. This means there is heat directly under a breathable seat cover made of Steron. The seat climate is regulated through the use of Luquafleece moisture absorbers without the use of electrical energy. Elastoflex soft foams in the seats save up to 20% of the weight, and at the same time offer ergonomic advantages through different hardness zones. These are the main features of the seat.
In addition to the tridion passenger cell, components such as the doors are made of carbon-fibre-reinforced epoxy resin. The use of such materials enables a weight saving of more than 50% to be achieved compared with steel or 30% compared with aluminium. Thanks to short hardening times, the Baxxodur resin systems from BASF are also suitable for producing larger volumes.
AI: What is your contribution in terms of temperature management?
Fischer: We introduced a heat shield that has not been previously used for automotive applications. It consists of a new kind of infrared-reflective film from BASF applied in the windscreen and side windows, protecting the car interior from heating up. The metal-free film is integrated between the panes of the safety glass, and ensures that the infrared rays are effectively reflected. Thanks to its high transparency in the visible range, it can also be applied to tinted windows and guarantees an unprecedented level of reflection of sunlight and heat. Unlike metalized films, which are already used in some vehicles, the new film reflects only the infrared rays of the sun. Radio waves needed to use GPS, Bluetooth, mobile phones or for toll collection pass through the glass unhindered.
AI: One factor slowing market adoption of electric vehicles is the relatively short driving range associated with current batteries. How do your new generations of cathode materials will enable to increase the driving distance?
Fischer: Batteries are the key technology for the electromobility of the future. Over the next five years, BASF will be investing a three-digit million euro sum in researching, developing and the production of battery materials. Part of the investment is being channelled into the construction of a production plant for advanced cathode materials in Elyria, Ohio. This new facility is scheduled to supply the market with cathode materials for the production of high-performance lithium-ion batteries from mid-2012. In addition, BASF has entered the field of electrolyte development. High-quality tailored electrolytes are essential for battery performance. We are also researching future battery concepts such as lithium sulphur and lithium-air. As a future system supplier we will be able to support our customers in the electromobility field.
AI: By how much is it possible to extend the range of a battery-electric driven vehicle using your expertise?
Fischer: The total of all technologies integrated in the concept vehicle make a perceptible contribution to increasing the range. This is always at the centre of discussions relating to battery-electric driven vehicles. With maximum energy efficiency, intelligent temperature management and consistent lightweight construction it is possible to increase the range by up to 20%.
AI: Which of the technologies that were on show at the IAA are ready for a series production, and when can we expect them on the marketplace?
Fischer: It varies from product to product and from application to application. Very promising is of course the all-plastic wheel rim. Regarding the seat, we have four products already, namely Ultramid, Steron, Luquafleece and Elastoflex – and we can offer other possibilities. For the light reflecting coating including so-called “cool pigments”, it is more or less close to launch. It is very promising that we can offer quite a number of innovations to the market in short to mid-term. For the mid to long-term are energy efficient applications such as OLED modules and organic color solar cells.
This was our intention from the very beginning, to offer the right mix between close to series production realistic technologies and products that are really visionary. That’s why Daimler and BASF chose the name “forvision”. It is a visionary concept, but not science fiction.
AI: What are your plans for the future?
Fischer: For us the automotive industry is – and will remain – a key sector. The automotive industry is really eager to bring innovations to the market, and very clearly plastics have a bright future in the car – not only for weight reduction, but also for acoustic management.
More Stories
Automotive Industries (AI) Newsletter April 2025
Bangkok International Motor Show 2025 – The Talk of Sensuous Automotive
GlobalLogic Pioneering Software-Defined Vehicles, AI Innovation, and Sustainable Solutions for the Future of Automotive Mobility