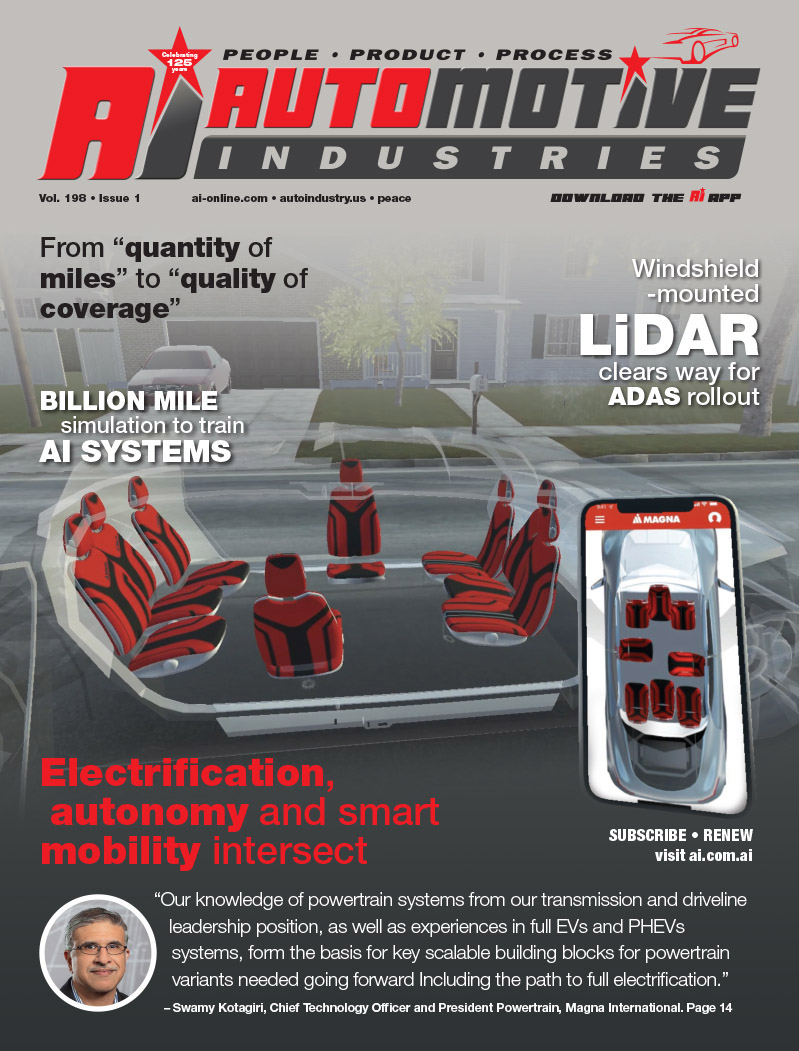
Damages to goods in transit globally are estimated to amount to around US$28 billion a year – but that does not have to be a cost of doing business, according to packaging specialist Sealed Air.
In one of its projects the company reduced damage to windshields shipped from the OEM to dealers from one in five to less than 1%. In a blog Sealed Air President, Product Care, Ken Chrisman, writes: “sustainable packaging practices aren’t as simple as swapping out peanuts for something recyclable or biodegradable – it’s much bigger than that. It’s about damage.
“Reducing damage isn’t just a customer experience imperative – it’s also a sustainability imperative. There is no amount of recyclable, biodegradable, reusable packaging that any of our expert engineers in any of our labs around the world could design that can counteract the increased carbon footprint of a damaged item. Damaged items have to get back on a truck or back on a plane and go back to their origin point.
Damaged items have to get rebuilt, repaired, restocked, rehandled, and sometimes they just get relegated to the landfill. Damaged items have to get reshipped, making another journey through the supply chain, in another box filled with packing materials that will have to be reused, recycled, or disposed of”. Through its data-driven packaging design process Sealed Air estimates that it keeps two million pounds of excess packaging out of landfills a year.
“If you want to be a more sustainable company, reducing damage is the most impactful thing you can do. If you want to be a more sustainable company, reducing damage is the most impactful thing you can do. If you can do it with packaging materials that are also reusable, recyclable, and responsible, so much the better. Performance and sustainability are not and should not be mutually exclusive,” says Chrisman.
Packaging redesign can reduce logistics costs, according to Sealed Air. Research has found that 85% of the total cost of a shipped package goes into transport, damage and labor. US companies pay an estimated US$550 million a year in additional shipping costs due to incorrect packaging. Savings of up to 30% a year on freight and storage costs are possible in many cases with the right packaging. “Sealed Air helps the automotive, aviation, and aerospace industries reduce costly damage to headlights, radios, wheels, jet engine trim, aircraft generators and other high-value components with engineered packaging solutions that provide superior protection,” says the company.
Design is undertaken in five North American Packaging Application Centers using a five-step approach. “We don’t just focus on a single package. We apply our operational excellence methodology to the entire fulfilment process. Our mission is to help customers package items more efficiently by increasing throughput, reducing damage and minimizing cube dimensions. We design packages that optimize material usage, create minimal waste, and maximize protection for the items inside. Right-sized packages lead to lower freight costs and greater efficiencies, resulting in a more sustainable global supply chain,” says the company. Sealed Air’s Packaging Application Centers complete more than 12,000 design projects a year, and the testing facilities meet the requirements of the International Safe Transit Association (ISTA)
Block
Sealed Air Packaging solutions
Bubble Wrap® IB is a flexible, protective air-cellular solution that can be inflated on-demand in whatever quantity is required. Bubble Wrap IB drastically reduces the impact of freight costs and carries a significantly smaller carbon footprint.
NewAir I.B. Flex™ is the next generation of on-demand inflatable cushioning systems with the agility to produce air cushioning materials ranging from ultra-light for source reduction to heavy duty for damage protection that rivals the performance of foams.
SpeedyPacker® for high-volume packaging applications delivers cost-effective, superior product protection.
iMold System creates engineered, pre-molded Instapak ® foam cushions for immediate use or to be transferred into storage bins for batching applications.
Medium and high-density foams with color and thickness options to meet any packaging or non-packaging application.
More Stories
Automotive Industries (AI) Newsletter April 2025
GlobalLogic Pioneering Software-Defined Vehicles, AI Innovation, and Sustainable Solutions for the Future of Automotive Mobility
Cybord TCI – The Future of Manufacturing Integrity